In computer numerical control (CNC) machining, whether you want to create a single prototype or go to large-scale production, the main priority is often reducing manufacturing costs. Fortunately, design decisions can help keep pricing down. By simply following certain Design for Machinability (DFM) rules, you can manufacture affordable parts that still comply with functional design requirements.
This article provides extensive tips to help optimize your design. We begin by examining what drives costs up in CNC machining. We then present comprehensive guidelines, offering proven design tips to reduce the cost of your project.
Did you know we offer local sourcing for CNC machining?
How much does CNC machining cost?
A quote for CNC-machined parts is determined by the following factors:
-
Machining time: The longer it takes to machine a part, the more expensive it is. Machining time is often the main cost driver in CNC, especially for large-scale productions where simple design mistakes can hurt economies of scale.
-
Start-up costs: Related to computer-aided design (CAD) file preparation and process planning, start-up costs are significant for smaller volumes. Fortunately, they are also fixed. If the design and the surface finish are suitable for cost scaling, you can lower the unit price by applying economies of scale principles.
-
Other manufacturing costs: To define tight tolerances or design parts with features that are difficult to CNC machine (e.g. very thin walls), you may need special tooling, closer quality control, and more processing steps at lower machining speed. This also impacts total manufacturing time and cost.
-
Material cost: The price of the bulk material and the ease with which that material can be machined greatly affect the overall cost in CNC. Optimizing your design while carefully considering your material can reduce costs.
By understanding what drives the costs of CNC machining, we can optimize design to lower the budget.
How to reduce CNC machining cost
1. Add a radius in internal vertical edges
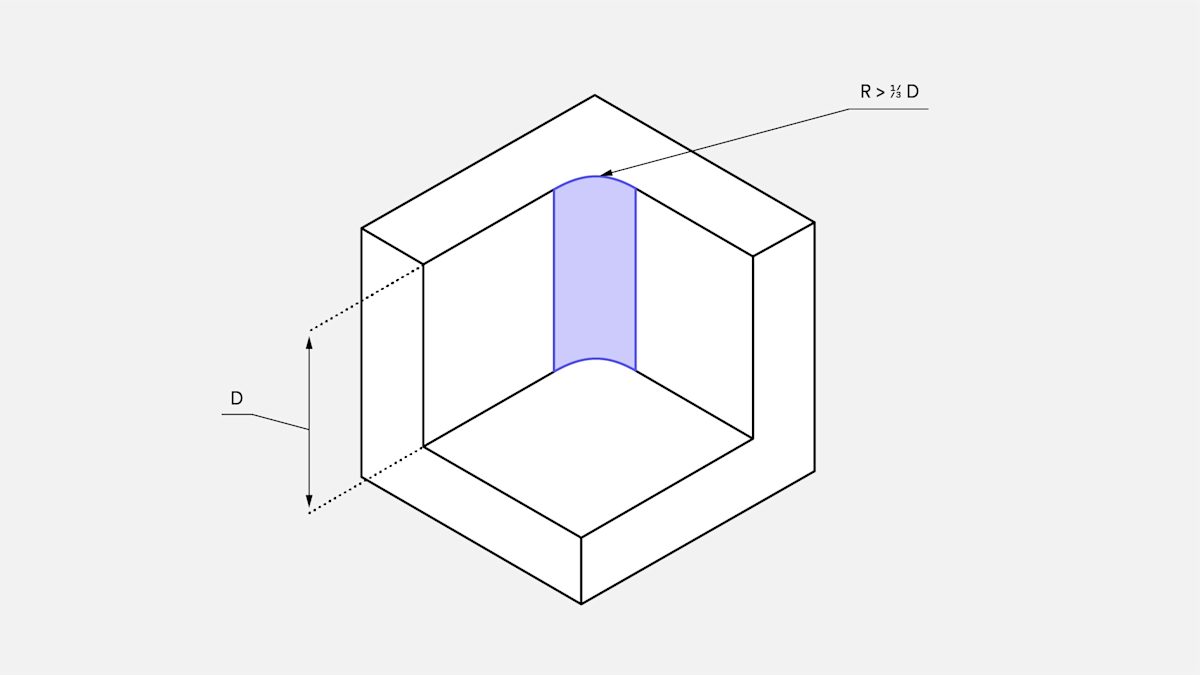
All CNC milling tools have a cylindrical shape and create a radius when cutting the edge of a pocket. A corner radius can be reduced by using a tool with a smaller diameter. This requires multiple passes at lower speed because smaller tools cannot remove material as quickly as larger tools in just one pass. This increases machining time and cost.
To minimize cost:
-
Add a radius of at least one third of the depth of the cavity—the larger, the better.
-
Use the same radius for all internal edges to eliminate the need for tool changes.
-
On the floor of the cavity, use a smaller radius (.5 or 1mm) or no radius at all.
Good to know: Ideally, the corner radius should be slightly larger than the radius of the tool used to machine the cavity. This reduces the loads on the tool and thus manufacturing cost. For example, if your design has a cavity that is 12mm in depth, add a 5mm (or larger) radius at the corners. This allows a tool with an 8mm diameter to cut at a faster speed.
Pro tip: If you need internal edges with sharp corners (e.g. when a part with a rectangular shape needs to fit in the cavity), instead of reducing the internal edge’s radius, use a shape with undercuts like those shown in the image below.
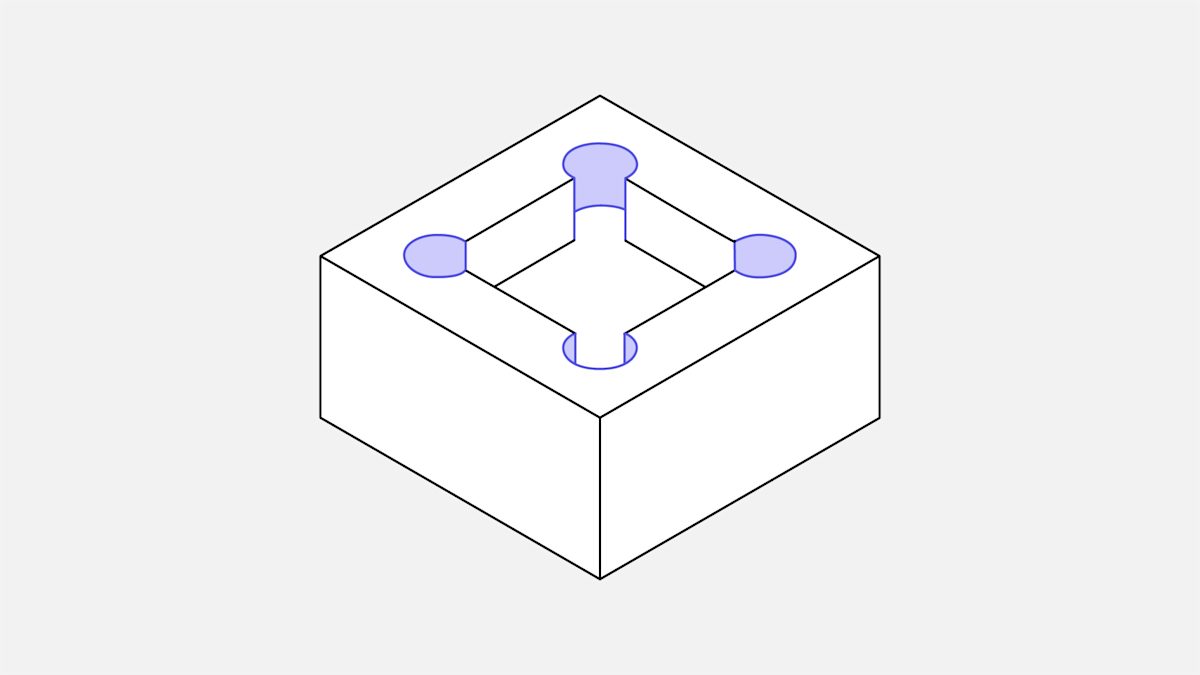
2. Limit the depth of cavities

Machining deep cavities affects the cost of CNC parts dramatically because a lot of material must be removed. This is both time-consuming and wasteful.
CNC tools have a limited cutting length. They typically work best when cutting cavities with a depth of up to two to three times their diameter. For example, a milling tool with a 12mm diameter can safely cut cavities up to 25mm in depth. It is possible to cut deeper cavities (up to four times the diameter of the tool or greater), but this drives up cost because special tooling or multi-axis CNC systems are required.
To minimize cost:
-
Limit the depth of all cavities to four times their length—that is, the largest dimension on the XY plane.
-
Adjust the internal corner radii accordingly. Use the advice in tip number 1 if needed.
3. Increase the thickness of thin walls
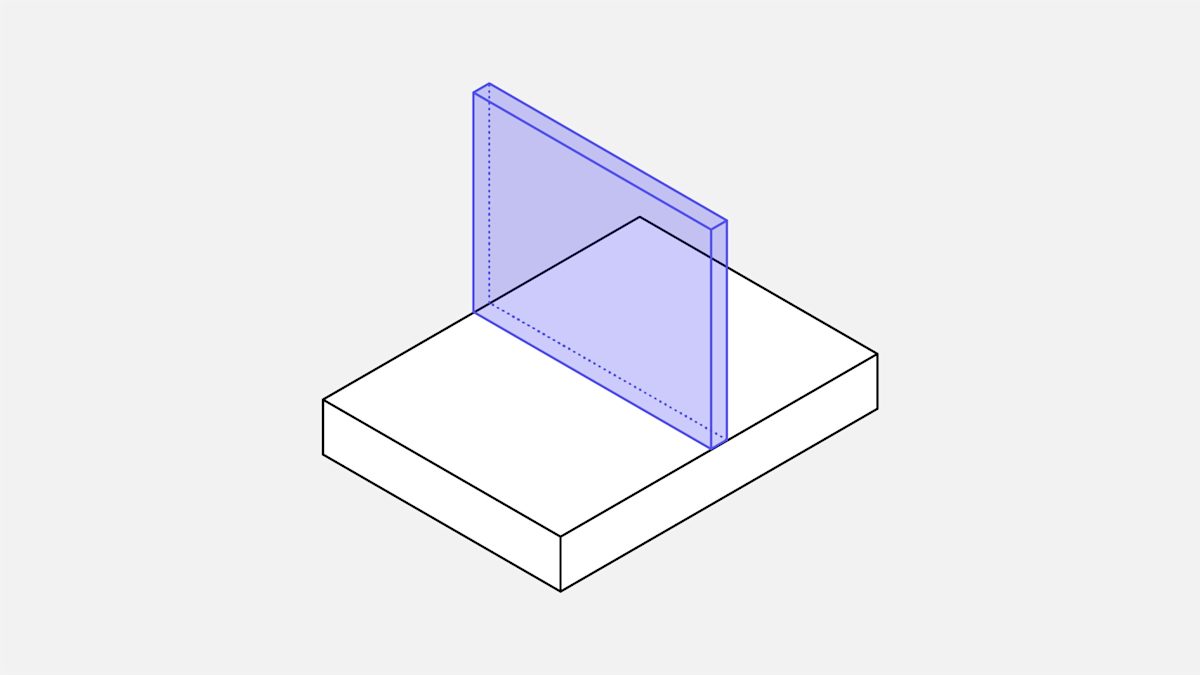
Unless weight is a major concern, manufacture thick solid sections because they are more stable and less expensive to machine. To avoid deformation or fractures when machining a thin wall, use multiple passes at low cutting depths. Thin features are also highly prone to vibrations, so machining them accurately is challenging and increases machining time considerably.
To minimize cost:
-
For metal parts, design walls thicker than 0.8mm—the thicker, the better.
-
For plastic parts, keep the minimum wall thickness above 1.5mm.
Good to know: The minimum wall thickness that can be achieved for metals is 0.5mm. For plastics, it is 1mm. Assess the machinability of such features case by case.
Important: Thin walls are often an issue when placing holes (and threads) very close to a part’s edge. Take this into account when designing for CNC machining.
4. Limit the length of threads
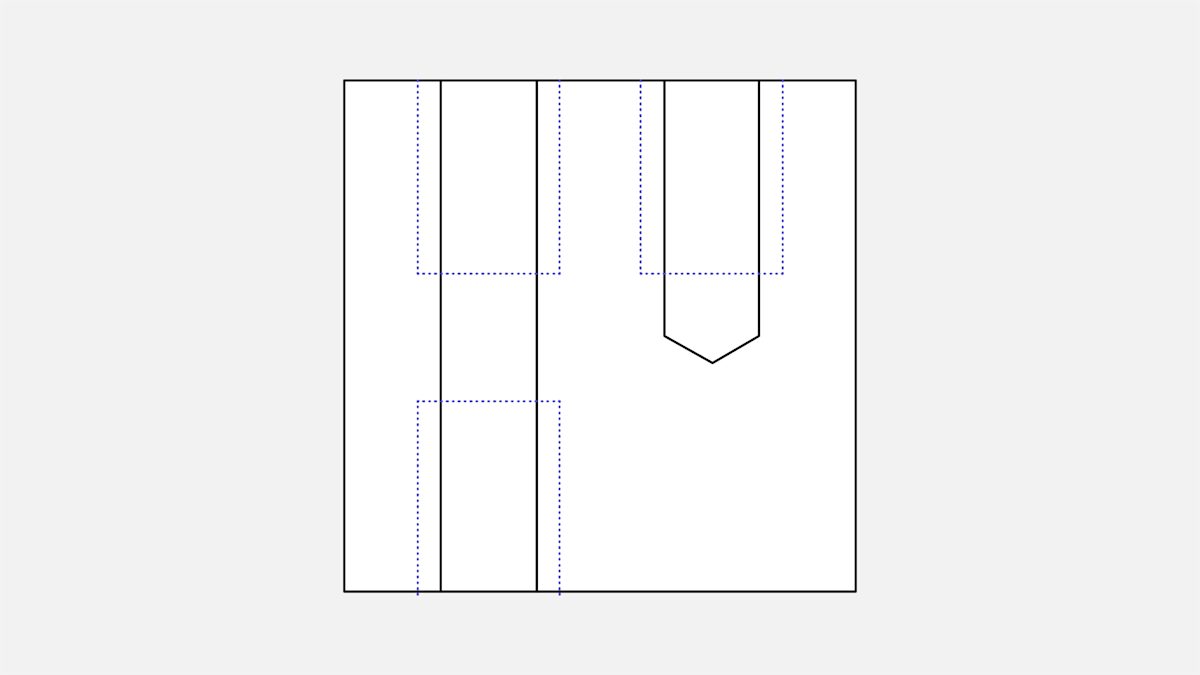
Including threads that are longer than necessary can increase the cost of CNC parts because special tooling may be required. Threads longer than 1.5 times the diameter of the hole do not enhance a connection’s strength.
To minimize cost:
-
Design threads with a maximum length of up to three times the hole diameter.
-
For threads in blind holes, add at least half of the diameter of the unthreaded length at the bottom of the hole.
5. Use standard hole sized
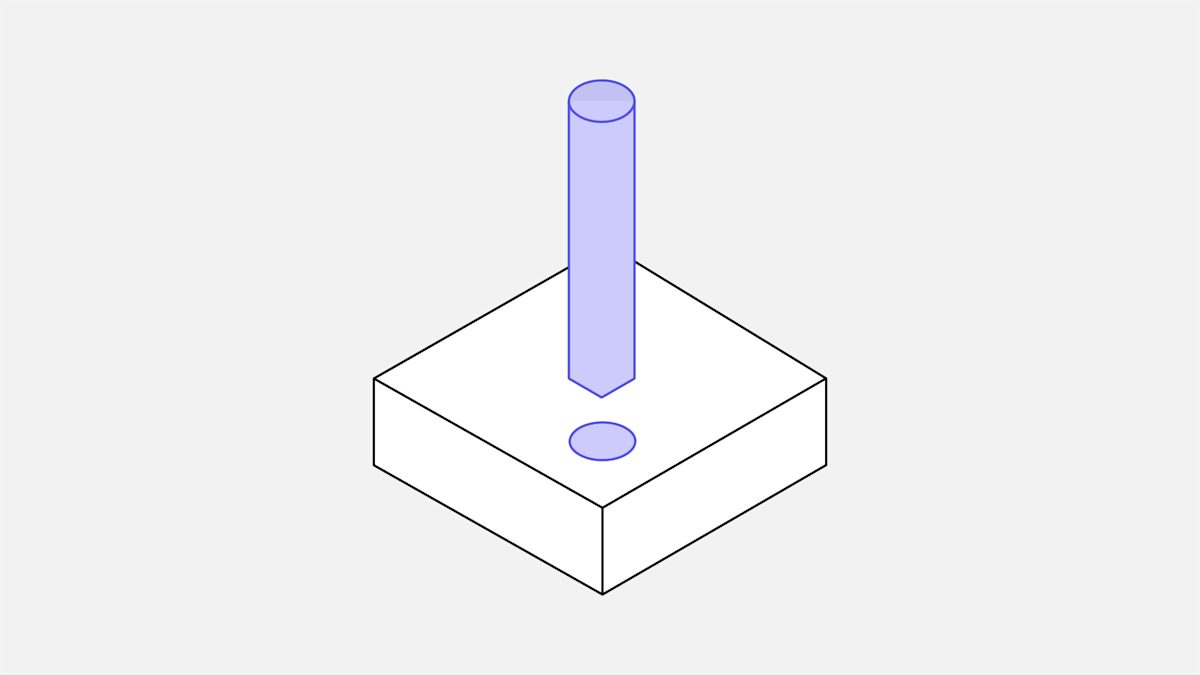
Holes can be CNC-machined quickly and to great accuracy using standard drill bits. For non-standard sizes, an extra machining step is required, which drives up cost.
When possible, use through holes instead of blind holes because they are easier to machine.
Limit the depth of holes to four times their diameter. Deeper holes (up to 10 times the diameter) can be manufactured, but they are likely to drive up cost because they require more time to machine.
To minimize cost:
-
Design holes with a diameter that is an increment of 0.1mm for diameters up to 10mm. For those above 10mm, use an increment of 0.5mm.
-
When designing in inches, use conventional fractions of an inch or refer to a fractional-inch drill bit sizes table.
As an added bonus for cutting down on lead times, try using standard thread sizes in your CNC designs. This will reduce the time it takes to machine your parts, which will also lower costs.
6. Only specify tolerances when necessary
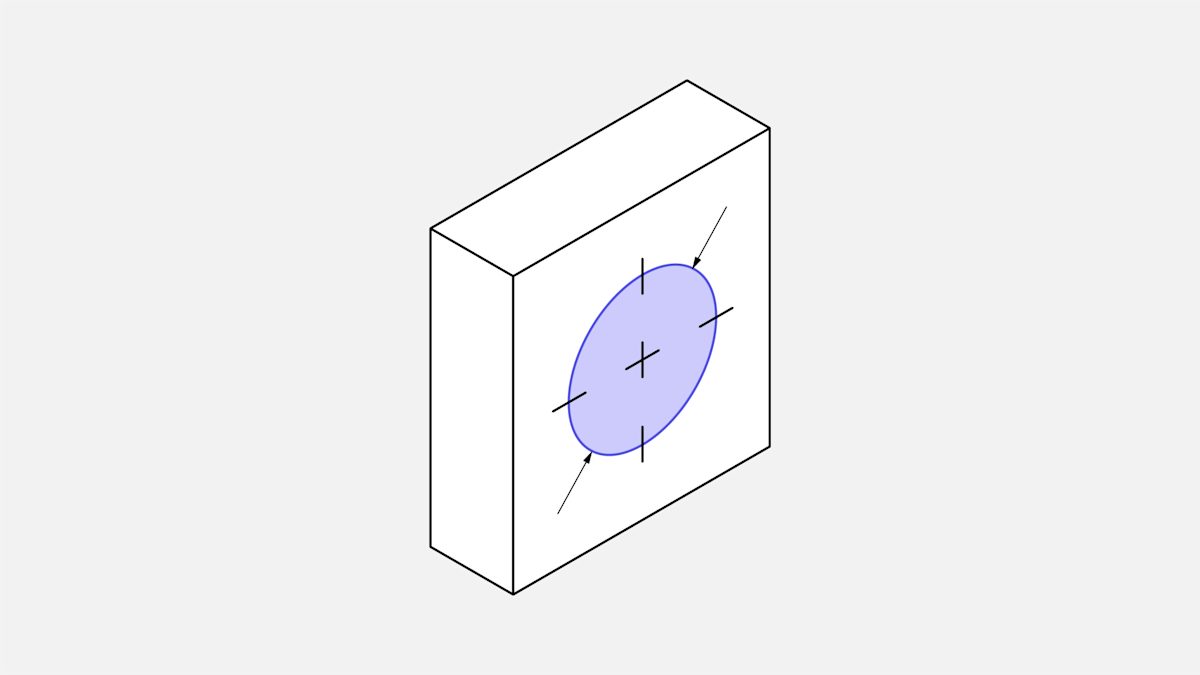
Defining tight tolerances increases the cost of machining a feature, so it should only be done when absolutely necessary. If a specific tolerance is not defined on the technical drawing, the parts are machined using the standard tolerance (± 0.125mm or better). This is sufficient for most non-critical features.
To minimize cost:
-
Only define tighter tolerances when it is absolutely necessary.
-
Define a single datum (e.g. the cross-section of two edges) as a reference for all dimensions with tolerances.
Pro tip: Use Geometric Dimensioning and Tolerancing (GD&T) in technical drawings to reduce the cost of CNC machining. GD&T includes features such as flatness, straightness, circularity, and true position. It often defines a looser tolerance, although it requires advanced design knowledge to apply effectively.
7. Minimize the number of machine setups
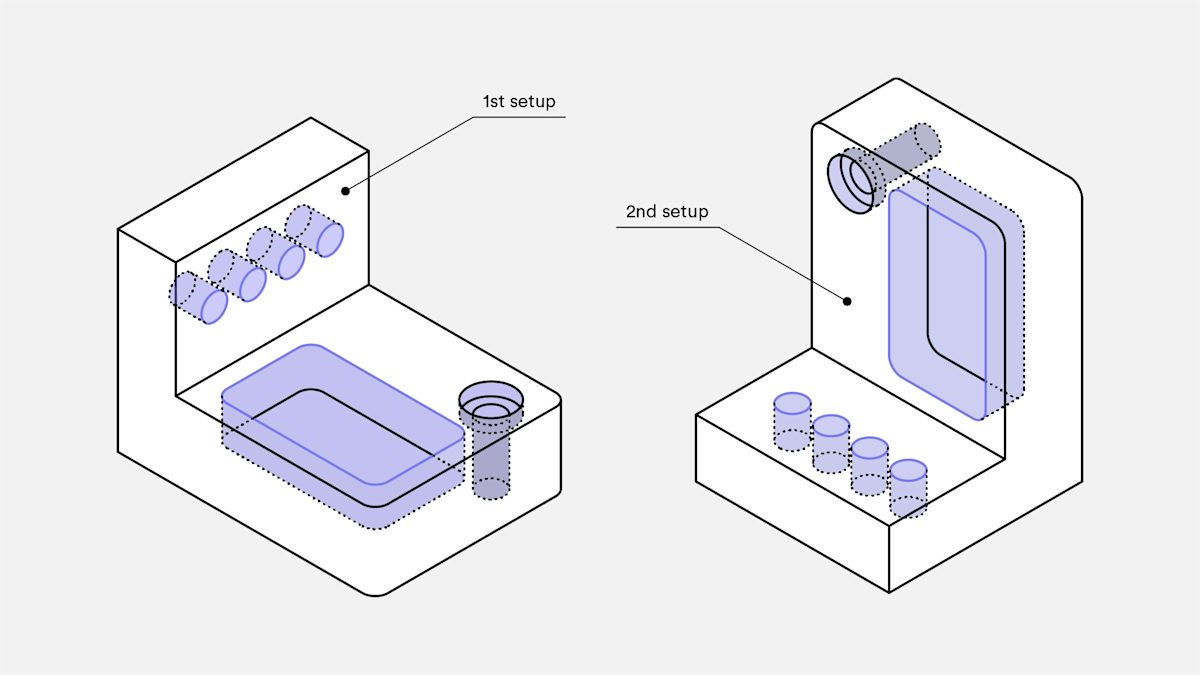
Design parts that can be machined in as few machine setups as possible. Ideally, use only one setup. For example, a part that has blind holes on both sides must be machined in two setups because it needs to be rotated for access to both sides.
Rotating or repositioning a part drives up manufacturing cost, as it usually must be done manually. Moreover, intricate geometries might require a custom fixture, increasing costs. Especially complicated geometries might require a multi-axis CNC system, also increasing cost.
Consider separating the part into multiple geometries that can be CNC-machined in a single setup and that can be bolted or welded together later. This also applies to parts with very deep pockets.
To minimize cost:
-
Design parts with a simple 2.5D geometry that can be manufactured in a single CNC machine setup.
-
If this is not possible, separate the part into multiple geometries that can be assembled later.
8. Avoid small features with high aspect ratio
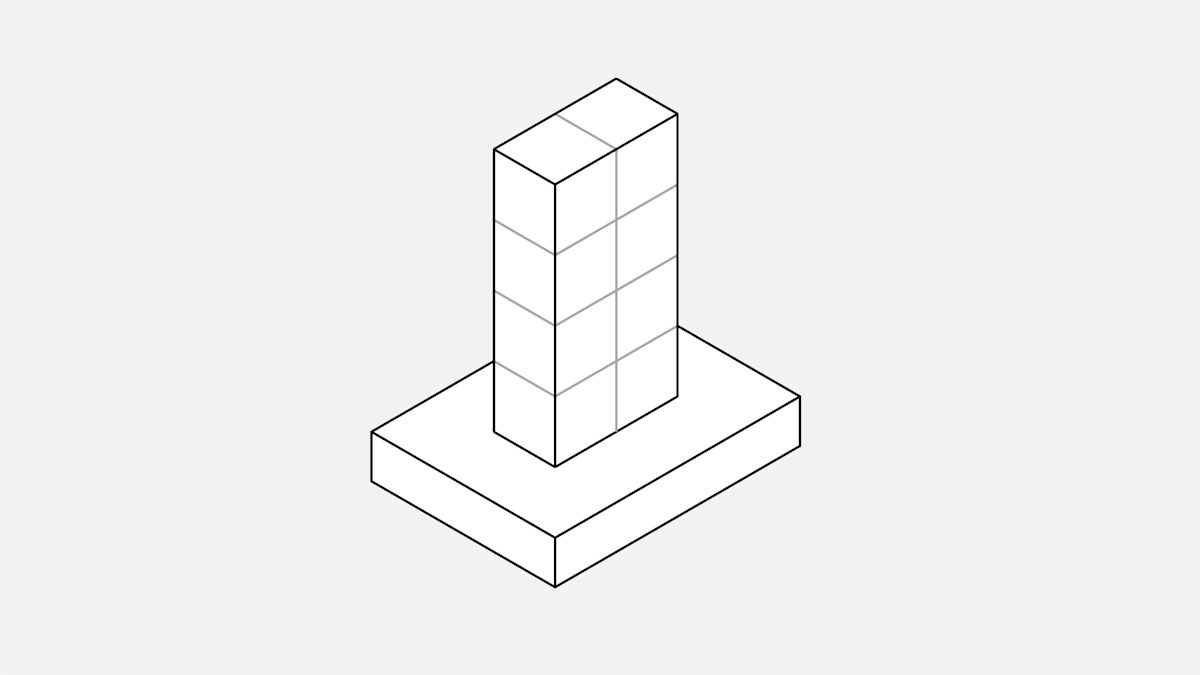
Small features with a high width-to-height aspect ratio are prone to vibrations and are thus difficult to machine accurately.
To minimize cost:
-
Design features with a width-to-height aspect ratio of less than four.
-
Add bracing support around small features or connect them to a wall to improve their stiffness.
9. Remove all text and lettering
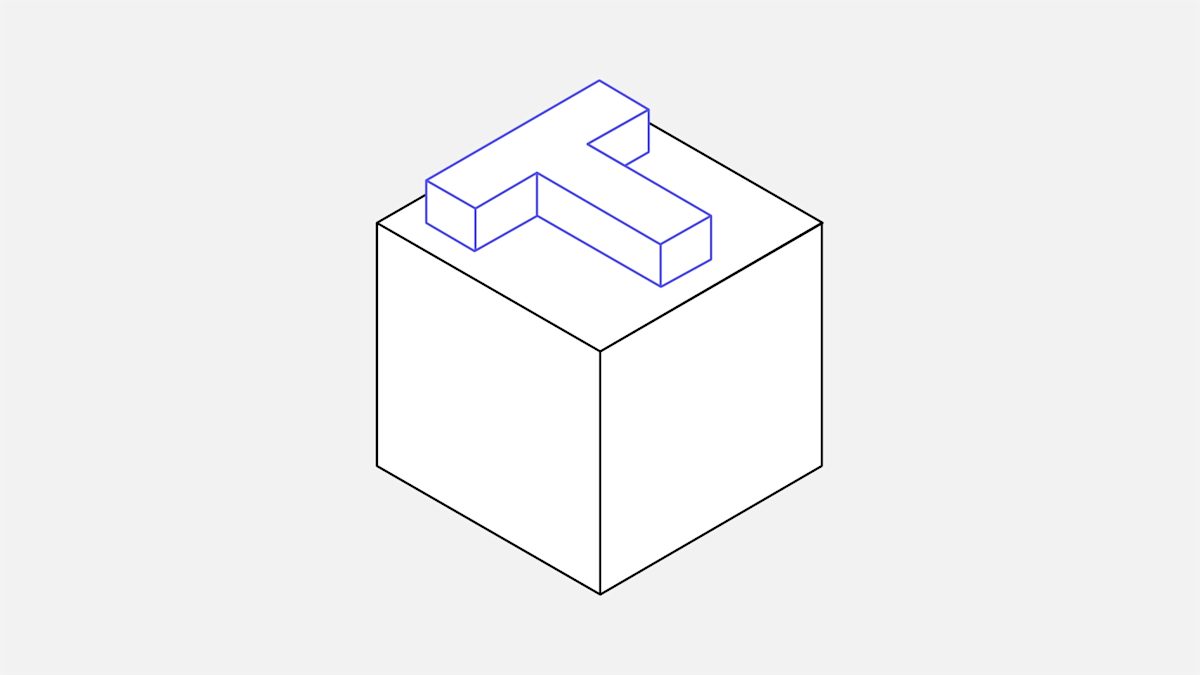
Adding text on the surface of a CNC-machined part can significantly drive up cost because it requires additional machining steps, which takes more time. Surface finishing methods, such as silk screening or painting, are a more cost-effective way of adding text on the surface of a CNC-machined part.
To minimize cost:
-
Remove all text and lettering from your CNC-machined parts.
-
If text is necessary, choose engraved over embossed lettering.
-
Use a minimum of size-20 sans serif font (e.g. Arial or Verdana).
10. Consider the machinability of the material
Machinability refers to the ease with which a material can be cut. The higher the machinability, the faster a material can be CNC machined, thereby lowering cost. Machinability depends on the physical properties of each material. Typically, the softer and more ductile a metal alloy, the easier it is to machine.
C360 brass is the alloy with the highest machinability, allowing for high speed machining. Aluminum alloys (e.g. 6061 and 7075) can also be machined very easily, though require slightly lower speeds.
Stainless steel has 10 times lower machinability than aluminum and will take at least twice as much time to machine. Different steel grades have different machinability. For example, 304 stainless steel has a machinability index of 45 percent, while 303 stainless steel (an alloy with very similar chemical composition) has an index of 78 percent, making it easier to machine.
The machinability of plastics mainly depends on their thermal properties and stiffness because they are prone to melting and bending during machining.
POM (Derlin) is the easiest plastic to machine, while ABS comes in a close second. PEEK and nylon 6 are common engineering plastics that are more difficult to machine.
To minimize cost:
-
If you have options, choose the material with better machinability, especially for larger orders.
11. Consider the price of the bulk material
The price of the bulk material is another factor that can greatly affect the cost of CNC-machined parts.
The table below summarizes the price of metal alloys and plastic materials commonly used in CNC for a sheet with dimensions of 6'' x 6'' x 1'' (or approximately 150 x 150 x 25mm).
Material | Price |
---|---|
Aluminum 6061 | $25 |
Aluminum 7075 | $80 |
Stainless steel 304 | $90 |
Stainless steel 303 | $150 |
C360 brass | $148 |
ABS | $17 |
Nylon 6 | $30 |
POM (Derlin) | $27 |
PEEK | $300 |
Source: McMaster
Aluminum 6061 is by far the most cost-effective way of creating metal prototypes because of its low cost and very good machinability.
Metals that offer greater machinability, such as stainless steel 303 and C360 brass, cost more and are thus better suited for larger volume production. In this case, economies of scale come into play because the higher material cost is outweighed by the much shorter machining times.
When it comes to plastics, ABS, nylon, and POM (Derlin) cost approximately the same as aluminum 6061. They are more difficult to machine though, so expect a higher cost. PEEK is very expensive material and should be used only when absolutely necessary.
To minimize cost:
-
Choose a material with low bulk price, especially for low-volume orders.
12. Avoid multiple surface finishes
Surface finishes improve the appearance of CNC-machined parts and their resistance to harsh environments, but they also drive up cost. Requesting multiple surfaces finishes on the same part further drives up cost because it requires extra steps (for example, masking the surfaces). An article summarizing the benefits of each surface finish for CNC parts can be found here.
To minimize cost:
-
Choose the “as machined” surface finish.
-
Request multiple surface finishes only when absolutely necessary.
13. Account for blank size
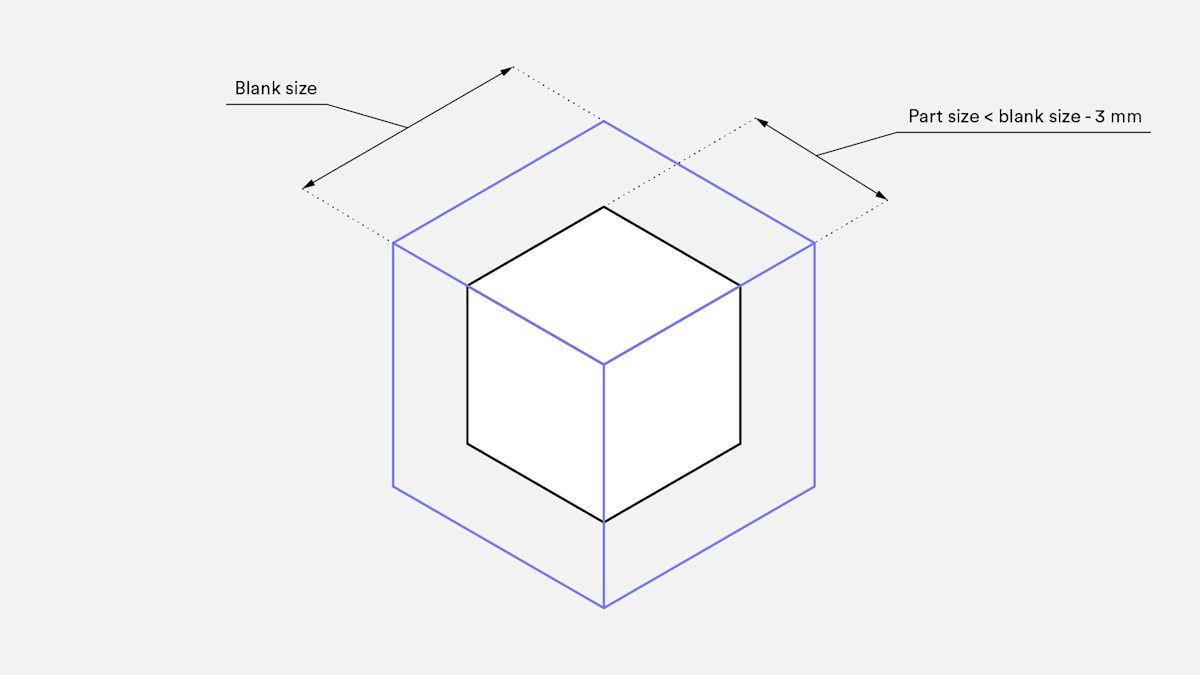
The size of the blank—that is, the stock material—may impact the overall cost. As a rule of thumb, the blank must be a minimum of 3mm larger than the end part. To ensure accuracy, some material must be removed from all edges of the part.
As an example of how the blank size affects pricing in CNC, consider designing a part that has an envelope of 30 x 30 x 30mm. These dimensions would require a larger blank to be used, which in this case is typically cut from a sheet that is 35mm thick. If the part had an envelope of 27 x 27 x 27mm, however, then a 30mm sheet could be used, saving a lot of material.
To minimize cost:
-
Design parts that have a dimension 3mm smaller than a standard blank size.
14. Take advantage of economies of scale
In CNC machining, quantity greatly affects unit price. This is because start-up costs are relatively high and, when quantities are small, they represent a big percentage of the cost. With large quantities, however, the per-unit costs decrease.
In the graph below, we plot the average unit price of 12 different parts machined in stainless steel 304.
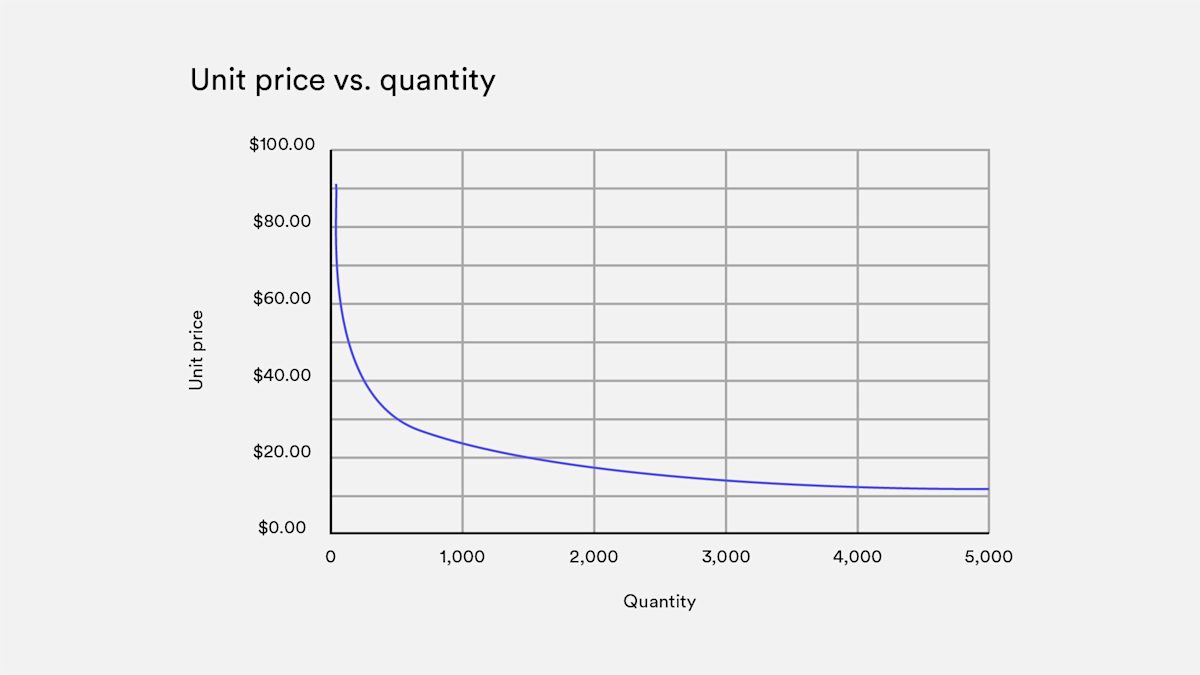
The drop in unit price is almost exponential, meaning that even increasing the volume from one to five can cut the unit price in half. Also, ordering very high volumes (> 1,000 parts) reduces the unit price by five to 10 times.
To minimize cost:
-
Take advantage of economies of scale by ordering higher quantities.
Best practices for lowering CNC costs
In conclusion, keep your CNC machining simple.
Complexity has a high price in CNC. Geometries that require special tooling or fixtures, multiple machine setups, or special materials cost more.
So to keep costs down, before you submit an order for quoting, ask the following questions:
-
Is my part optimized using designing for machinability guidelines?
-
Are all features in my model absolutely necessary? Or can I remove or simplify while retaining the part’s full functionality?
-
Can my design be separated into multiple parts that are easier to CNC machine and assemble later?
-
Is there a way to modify my design to eliminate the need for multiple machine setups or special tooling?
-
Is there a material that is less expensive or easier to machine that can fulfill my design requirements?
The present & the future of CNC machining
The capabilities of CNC machining are constantly expanding. For example, recent advances in CNC tooling enable modern CNC systems to thread holes throughout their length, and holes of any diameter can be CNC machined, without a significant effect on the price, by using a plunging CNC tool and using profile interpolation (i.e. a helical tool path).
In this article, we focused on general designing-for-manufacturability tips that have a universal application, no matter what CNC system is used. Interpret these tips as general good practices that can help you design parts more efficiently.
Download the CNC checklist for reducing costs
If you found this article useful and want to take it offline, you can download our essential CNC machining cost reduction checklist.