What is anodizing?
Anodizing is a key step in manufacturing aluminum CNC machined parts. An electrochemical process that involves coating a metal part with an oxide surface layer, anodizing gives the part additional sturdiness and a more attractive finish. While anodizing is most common with aluminum, other substrates can be anodized, including magnesium and titanium.
Anodizing ensures a part can resist corrosion and wear and tear from prolonged use, and that it retains its cosmetic appearance under any conditions. In many cases, manufacturers send parts to a third-party service provider specialized in anodizing, similar to when you need heat treatment, tempering or electroplating.
The most common types of anodizing are Type I (Chromic Acid Anodize), Type II (Sulfuric Acid Anodize) and Type III, also known as Hardcoat. Each type of anodizing is ideal for different materials and serves its own distinct manufacturing parameters. Despite each type’s specific advantages and drawbacks, they all work relatively the same way.
In this article, we explain how the general process of anodizing works, common manufacturing parameters and key advantages and disadvantages for several applications. If you’re ready to get your parts into production, head here to learn more about our surface finishing services.
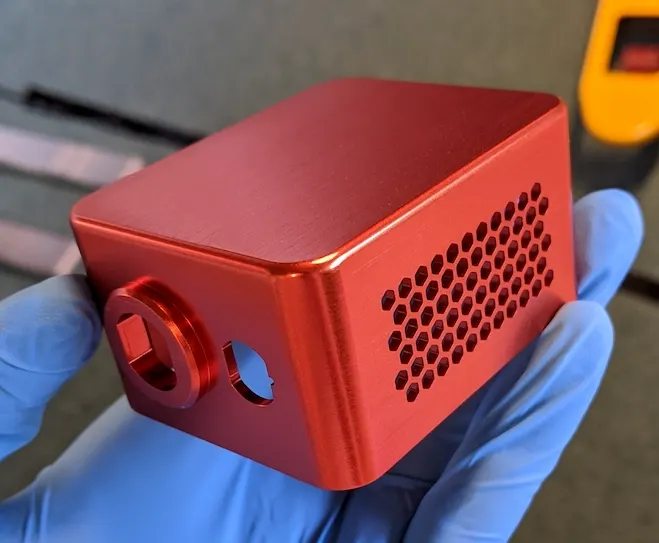
Did you know we offer local sourcing for CNC machining?
How does anodizing work?
The simplest way to understand how anodizing works is in the name. To anodize a part, you connect it to a positive terminal of an electrical circuit, also called an anode. You then submerge the part in an acidic electrolyte bath solution. This solution contains chemical compounds, such as sodium phosphate, which fill the bath with positive and negative ions.
Once the part is submerged and secured to a hanger so it doesn’t move around, you apply the negative end of the circuit, or cathode, to a metal electrode in the bath. When you send voltage through the circuit, the negative electrode attracts positive ions (cations) from the part, and the aluminum part attracts negative O2 ions (anions) from the solution.
When positive aluminum ions leave the part’s surface, it becomes porous, reacting with the negative O2 ions to grow a layer of aluminum oxide.
Let’s break the process down into these simple steps:
-
Turn the part into an anode with a positive charge
-
Turn the metal plates into the cathode with a negative charge
-
Submerge both in the acidic bath
-
Apply voltage
-
Subtract aluminum ions from the part, creating pores
-
Attract oxygen ions to the part’s surface
-
The reaction forms a hard, corrosion-resistant aluminum oxide layer
How do you anodize aluminum?
Here is a detailed introduction to anodizing and why it’s an ideal finishing process (and essential for custom aluminum parts ). We cover correct racking, cleaning and etching, desmutting, coloring, sealing, curing and wrapping.
What are the parameters and properties of anodizing?
Here are the parameters to consider with anodizing:
-
Time
-
Voltage
-
Electrolyte composition
-
Current density
-
Temperature
-
Anodizing regime
-
Pre-treatment
When you tweak these parameters, the material properties modified by anodizing include:
-
Hardness
-
Color
-
Porosity
-
Thickness
-
Corrosion resistance
-
Biocompatibility (e.g. for medical implants)
In terms of thickness, parts being anodized develop deeper pores and a thicker layer of aluminum oxide the more time they spend in the acidic solution. Anodized coatings range in thickness from 8-16 μm, or up to 35-50 μm for hardcoating.
For more information on choosing the right anodizing process, check out our Surface Finish Service page or head to our Help Center.
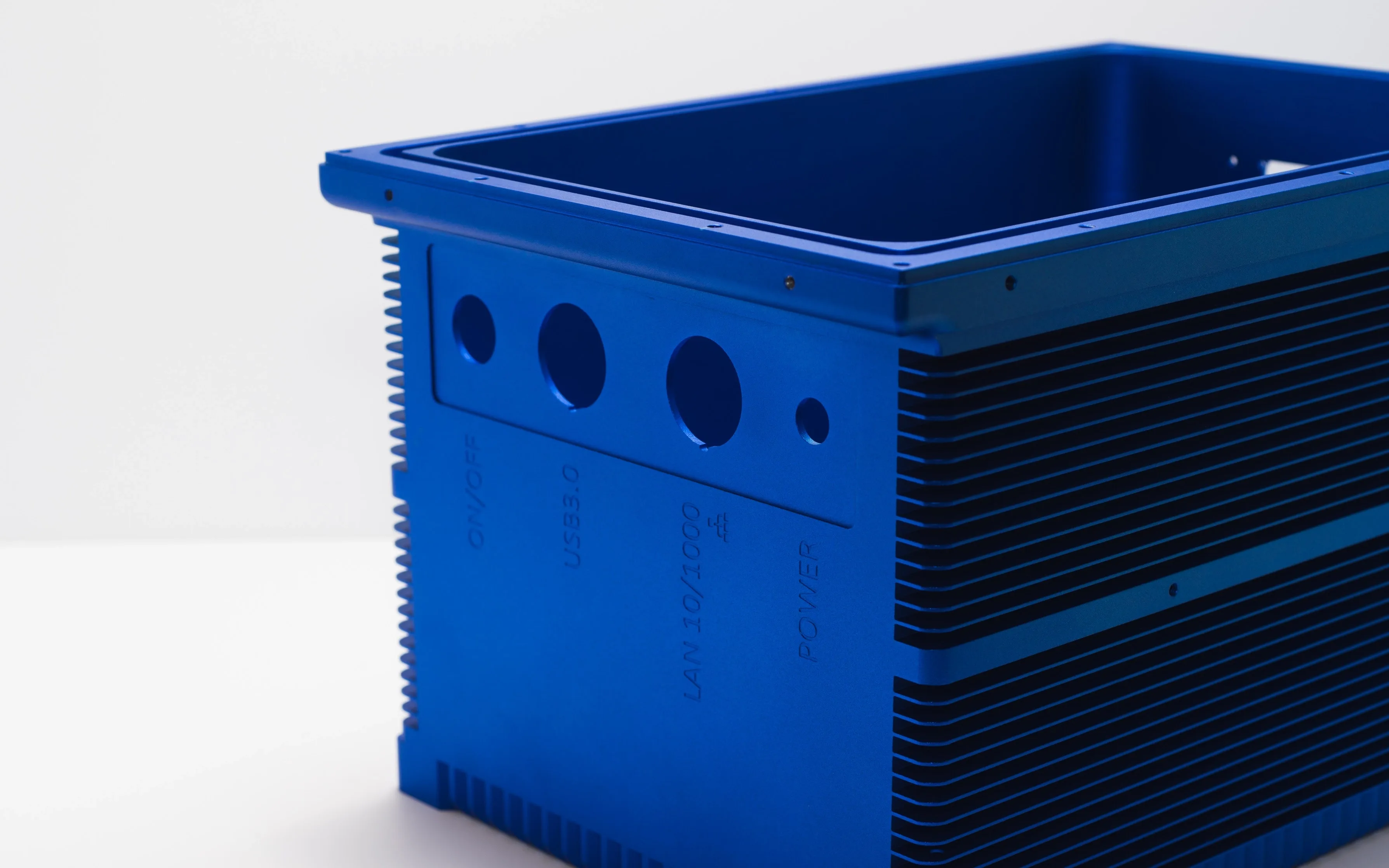
What’s the difference between anodizing and electroplating?
If you’re familiar with electroplating, you may recognize that anodizing is similar in many ways. Comparing the two processes definitely helps to understand anodizing as a unique and important step in fabricating CNC aluminum parts.
Similar to anodizing, electroplating involves placing the part in an electrolyte bath and applying a charge to it. The key difference is that with electroplating, the part gets negatively charged, becoming the cathode instead of the anode.
The anode is applied to a piece of the desired plating material, such as gold. As with anodizing, this circuit allows positively charged ions to flow to the cathode (the part). These ions coat the part with a thin, even layer.
How does anodizing work in practice?
Anodizing follows the same broad strokes as many other finishing processes. In practice, this means that you should follow this process:
-
Prepare the surface
-
Anodize
-
Clean the parts
-
Add color
-
Seal the pores
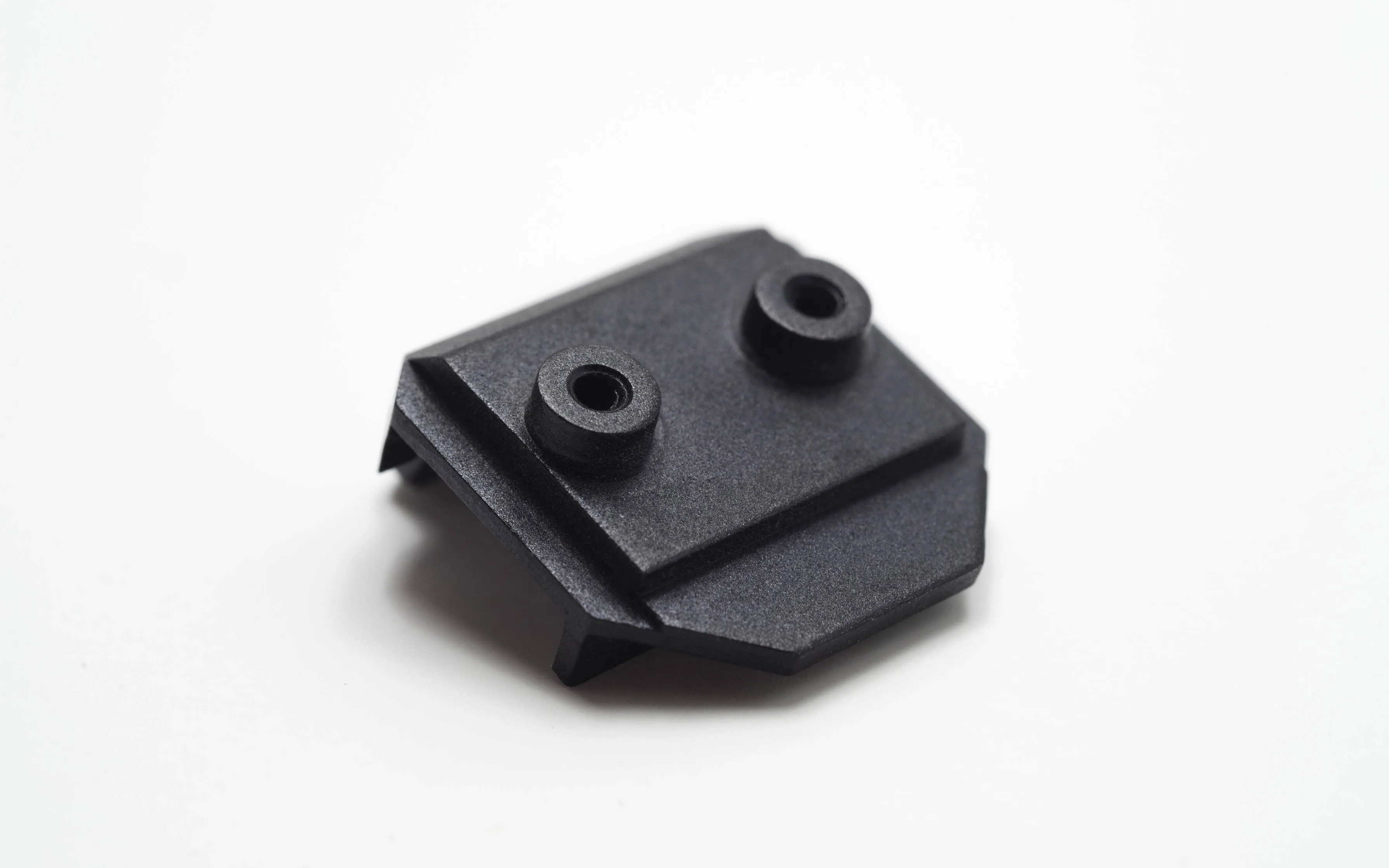
Prepare the surface
Before you anodize a part, you have to prepare its surface through mechanical and chemical means. First, polish or bead blast the surface to ensure your part has the desired visual appearance. Bead blasting will give your part a natural matte finish, while brushing will give your part a brushed appearance.
The chemicals you use prior to anodizing will influence the glossiness of your part. Etching, for instance, will give your part a smooth satin finish. For a glossy finish, you’ll want to go with bright dipping or chemical polishing.
Next, rinse the part with deionized water and other solvents to remove impurities, including machining residues like oils and coolant. Place the rinsed parts in a chemical bath of sodium hydroxide (NaOH) and nitric acid (HNO3) to scour the top layer of the metal. If you’ve already treated the part mechanically, this step isn’t always necessary.
You can also mask areas of a part to prevent an anodizing surface from forming there.
Anodize
Next, place the part or parts in the anodization bath, connected to the electrical circuit. Parameters can vary based on the desired properties described above, including the solution composition, temperature, current density, voltage and time.
Clean the parts
After anodization, you have to clean the part with deionized water and solvents. Don’t forget to dry the part after. This removes excess solution and readies the part for its chromatic finish.
Add color
You can control the color of the part during anodizing. The wavelengths of the visible spectrum of light, measured in nanometers, can reflect differently depending on the thickness of the oxide coating. Different parameters achieve a variety of colors.
To give your part a bronze or black finish, immerse the part in a solution of metallic salts. These react with the surface to fill the pores with a black or bronze chemical compound. This process is called electrolytic coloring.
If you want another color, you can use dip coloring, which fills the pores with a dye solution. After dipping your part in the dye, place it in heated DI water to halt any further reactions. Dip coloring is the least durable of the coloring options detailed here, as the color may degrade when exposed to UV light over time.

Seal the pores
After anodizing, you have to seal the microscopic pores on the surface of the part to prevent further corrosion and improve performance. Without sealing the pores, anodized parts may feel sticky to the touch. As well, open pores can collect dirt, contaminants and stains.
These are three common processes for sealing pores:
Hot DI sealing:
With this method, you immerse the part in deionized water heated to almost boiling. The water reacts with the part to form hydrated aluminum oxide or boehmite. Boehmite takes up more space than aluminum oxide and fills the pores.
This process is simple and easy to standardize. However, it comes with a high energy cost, and can cause dye bleed and color leaching on dyed parts.
Mid-temperature sealing
Less energy-intensive than hot sealing, this method uses metal salts in solution, such as salts of nickel, magnesium or cobalt, to react with the surface and fill the pores.
This method is better for dyed parts and reduces sealing smut or surface mineral deposits. It’s more difficult to control, though, and trickier to repeat with the same accuracy.
Cold or room-temperature sealing
Cold sealing chemistries typically include nickel-fluoride formulations designed to react with the porous aluminum oxide layer and deposit as a sealed layer of fluoro-aluminate on the surface.
This process etches the surface for better adhesion and performance. It also meets some mil-spec and automotive specifications. However, it can be slow, and may require a hot water bath to speed curing, making it harder to control.
What does anodizing do and why should you do it?
Anodizing is hugely beneficial if you want high-quality and durable aluminum parts. Because the oxide layer is fully integrated with the material surface, it won’t chip, peel or crack over time. The same can’t be said for paint or powder coating. Anodized finishes have a very long life span thanks to the superior bonding and adhesion of the finish.
Anodizing also hardens the part’s surface up to Rockwell 70C, which ensures the part can handle a lot of use. Because anodized parts are so durable, they don’t often require oiling, conditioning or repainting. Additionally, hard-anodized aluminum is an electrical insulator and serves as a viable insulating material when others prove insufficient.
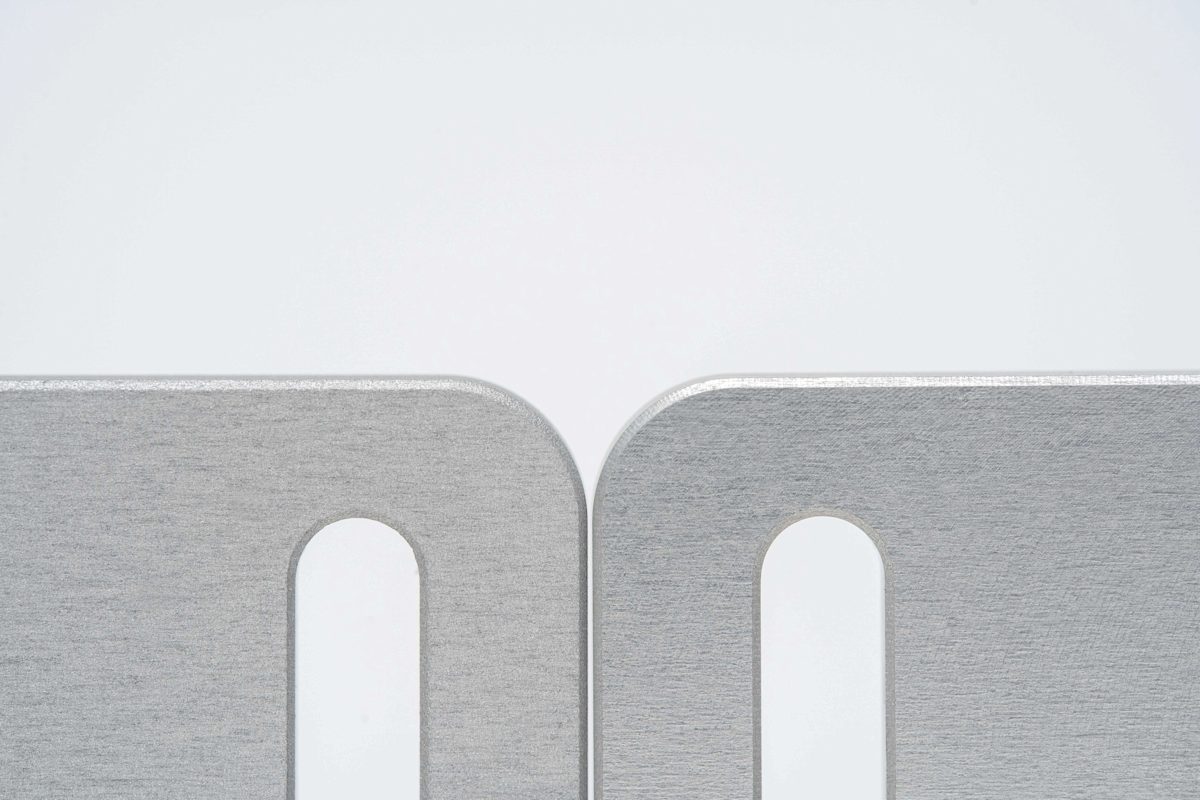
When you use anodizing to give parts a specific color, these colorants and dyes don’t sit precariously on a flat surface. The coloring agents seep into the hollow pores created by the anodizing reaction. This means that the part doesn’t lose its color to abrasion, wear, UV exposure and other sources of damage. Depending on the type of anodizing you are using, there’s also a wide variety of color finishes to choose from.
On top of these advantages, the process itself is cost-efficient, as is the cost of maintaining the part over its lifecycle. Not only that, anodizing is relatively safe, and produces fewer harmful or environmentally damaging by-products than other finishing processes.

What should I know before anodizing parts?
While anodizing is integral to manufacturing high quality aluminum parts, there are a few things to keep in mind before going ahead with the process. Of course, not all materials can be anodized. You will likely only ever anodize aluminum, though titanium, zinc, tantalum and niobium may also need a swift anodizing round.
To anodize a part, you have to fully submerge it into the solution. Usually, this requires you to mount the part on hangers, meaning that your part will include design features that do not make contact with the solution to be anodized. As a result, a part can never be fully anodized across 100% of its surface.
Another factor to keep in mind is that the geometric dimensions and tolerances of your part may change with anodization. Anodizing builds up a layer on the part, so remember that when you’re in the design process. As well, anodizing will affect the surface roughness of your part.
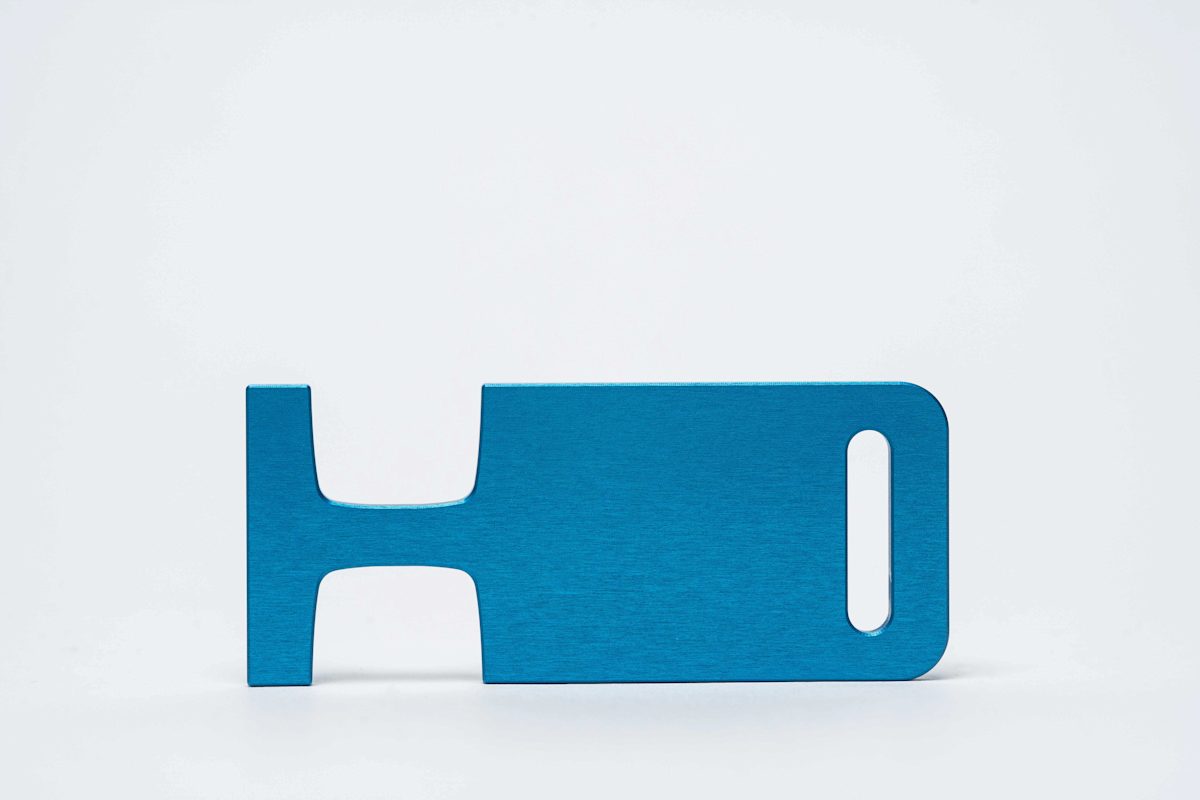
Frequently asked questions
Why do you anodize parts?
Anodizing is a necessary step in manufacturing aluminum parts. The process improves the part’s mechanical and aesthetic properties, making the part resistant to wear and tear and giving it an attractive finish. It also improves corrosion resistance - the best part about anodizing is that it keeps your aluminum parts safe from corrosion.
How does anodizing work?
Anodizing works by immersing a metal part into an acid electrolyte bath and electrifying both the part and the solution. It’s an electrochemical process that turns the part’s metal surface into a durable and attractive anodic oxide finish.
How do I assess the quality of anodized parts?
To assess the quality of anodization, you should test how resistant the part is to abrasion and corrosion. If the material finish bleeds when tested with alcohol or specialized sandpaper, the quality is likely not up to the desired standard.
Why should I include jig marks in my design?
When designing a part that will be anodized, it’s important to clearly include and distinguish between the A and B sides. One side will have jig marks where the part is fixed in the solution, so you’ll want to indicate in the design which side will end up with those unfinished areas (most likely the B side).
Is anodizing conductive?
Anodizing is not conductive. If your part requires conductive features, you may need to apply a clear chemical conversion coating. This means that you’ll need to mask those to-be-conductive features on your part during the anodization process.
What materials can I anodize?
Anodization is key for all grades of aluminum, and can be used for other metals, including titanium, zinc, tantalum and niobium.
Is anodizing expensive?
Anodizing costs depend on the quantity, dimensions, color and shape of your part, as well as the anodizing type. While anodizing can get expensive, it’s important to remember the high value that comes with the price tag.
Will anodization wear off?
While anodizing leaves a very durable surface finish on your part, an acid wash or general use can wear off anodize eventually.
What chemicals does anodizing use?
To anodize aluminum parts, it’s most common to use either chromic acid, oxalic acid or sulfuric acid. Phosphoric acid and boric sulfuric acid mix are now part of aerospace’s anodizing process.
What’s the difference between Type II and Type III anodizing?
Type II anodization is the more standard process of using sulfuric acid, while Type III (hardcoat) involves more demanding conditions to achieve harder coating that’s more resistant to abrasion. Type III coating is applied directly to a surface as machined and is more suitable for functional applications. Refer to our article on types of anodizing.