Snap-fit joints are a quick and easy way to connect two 3D-printed components by using interlocking features. Not only are they a low-cost and time-saving connection method, but they can also reduce the number of parts needed in an assembly. Plus, they offer the possibility of rapid assembly and disassembly.
This article covers the basics of snap-fit joints (also called connectors and clips) for 3D printing, what to consider when designing snap-fits with plastics and thermoplastics and which 3D printing process is optimal for manufacturing the best snap-fits.
Watch before you read: does Protolabs Network have a snap-fit tutorial?
The answer is yes: we do have a tutorial to help engineers design perfect snap-fits. Before (or after) diving into this comprehensive guide, check out this nifty video with detailed instructions for 3D printing snap-fits in style.
What are snap-fit joints (or connectors/clips)?
A snap-fit joint is a cost-effective and relatively simple method of attaching two 3d-printed plastic components. Also known as a connector or clip, a snap-fit generally consists of a small and bendable protrusion, like a bead, stud, or hook, and a mating depression that deflects and catches the protruding feature. The two features clicking into place create a robust interlocking connection.
Once the features have clicked into place, an undercut holds the two components of the snap-fit together. Depending on the shape of this integral undercut, snap-fit assemblies can also be designed to make the interlocking connection permanent. A well-designed snap-fit joint with the right material can be used quite a number of times without any noticeable mechanical fatigue.
There are plenty of types of snap-fit types and geometries that follow the basic principles of two interlocking components.
Common types of snap-fits: cantilever and annular joints
The two most widely used and commonly effective types of snap-fit connectors are cantilever and annular joints. Let’s break these down.
Cantilever snap-fit joints
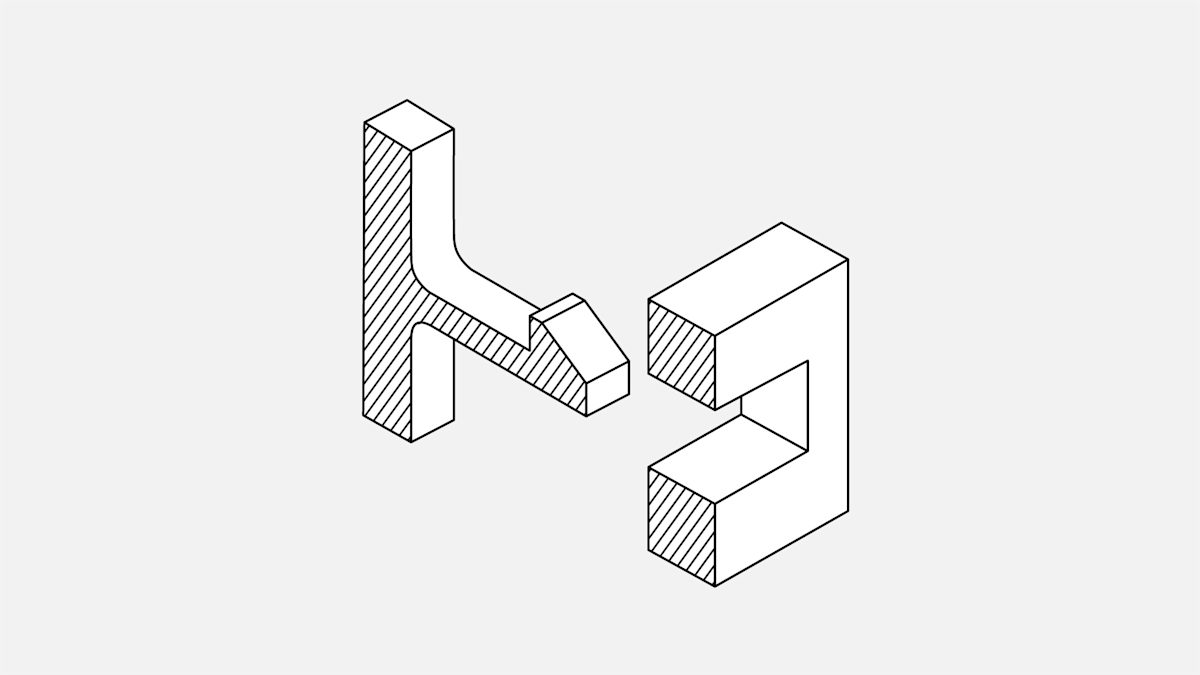
The most common snap-fit joint is the cantilever, consisting of a protrusion (some type of bead or hook) on one end of the component and a structural support feature at the other end. This protrusion is placed into an opening and bends back to lock the connection into place.
Cantilever snap-fits are easy to design and intuitive when it comes to assembly and disassembly. For many applications and cases, cantilevers are the most cost-effective way to connect to components.
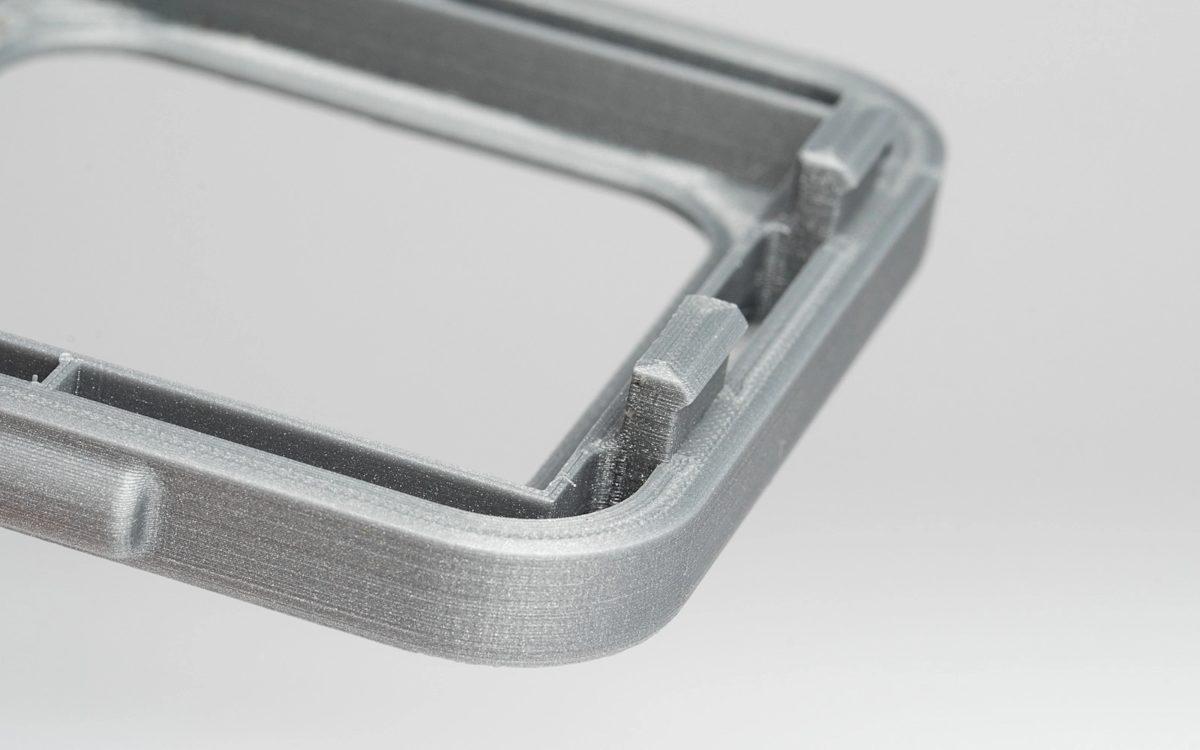
Annular snap-fit joints
Annular snap-fit joints use a hoop strain to hold a pressed part in place. Common examples of annular snap-fits are bottle and pen caps. With annular snap-fits, it’s possible to create a waterproof seal around the joint.
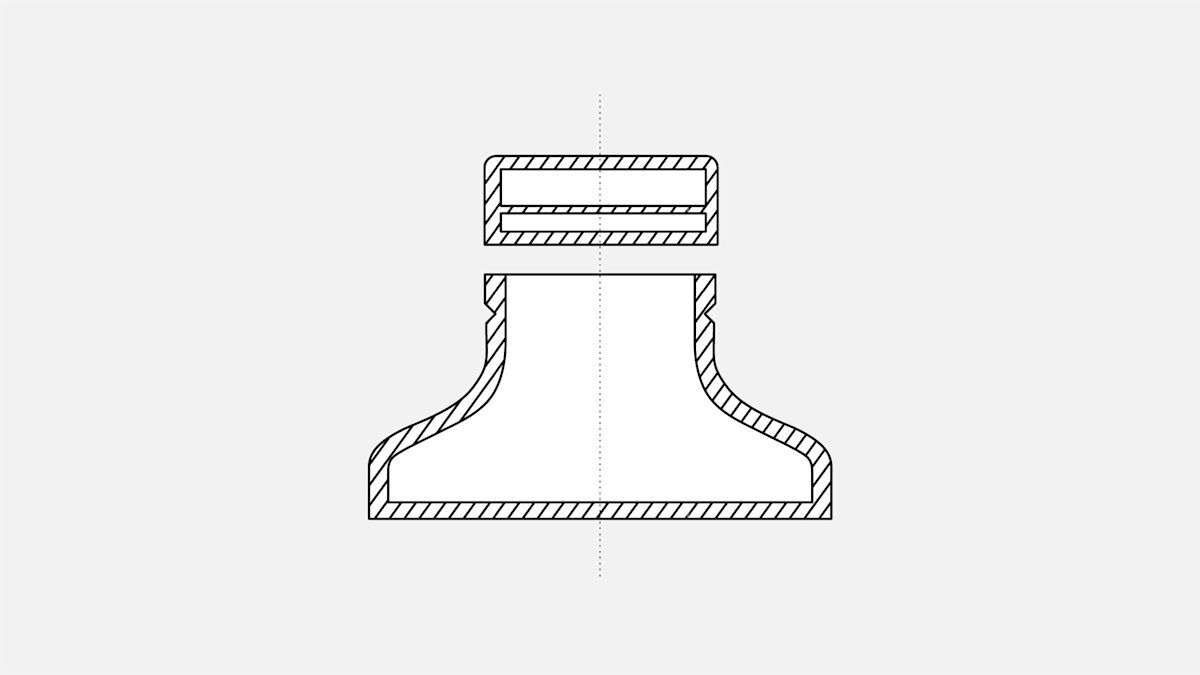
What are the advantages of snap-fitting with 3D printing?
While injection molding is often seen as the more robust way to produce snap-fit joints, 3D printing is a viable alternative (and even a go-to) with the right design and materials.
3D-printed snap-fits don’t have any of the design limitations associated with injection molding—for instance, draft angles, separation lines, wall thickness and undercuts—and can be designed and altered with ease. This makes them ideal for rapid prototyping, where clearance and fit are critical. This is why designers generally use 3D printing for snap-fits in enclosures.

What materials are used for 3D printing snap-fit joints?
Every 3D printing process has its pluses and minuses when it comes to producing parts with snap-fit connectors. This is due in part to the materials used with each of the major additive manufacturing technologies.
FDM is the most cost-efficient way to manufacture snap-fit connectors. While it’s definitely effective, the process has lower accuracy than other printing methods. If you choose FDM, we recommend using strain-resistant materials, such as ABS, Nylon and TPU.
SLA resins are also a viable option for making snap-fit joints, but they are relatively brittle. Using resins may increase the chances of the snap-fit breaking after repeated use. We recommend durable SLA resin if you print snap-fits with this technology.
SLS is more suitable than FDM and SLA for printing functional snap-fit prototypes and end-use parts that will be opened and closed many times. The best material for maximum tear resistance is SLS Nylon.
Similar to SLS, MJF (HP's Multi Jet Fusion) is optimal for manufacturing snap-fit connectors. MJF produces robust parts from Nylon PA 12 and a few other nylon and polypropylene options. What’s important to remember with MJF is that there are several design guidelines to follow to achieve the best results. For instance, we recommend a minimum thickness of 1 mm at the base of the cantilever and a minimum common overhang depth of at least 1 mm.
What are common problems with designing snap-fit joints?
The snap-fit design process isn’t the same for all technologies, materials and applications. Engineers faced with snap-fit design for 3D printing often encounter a few key challenges. Here we cover the main ones.
-
Sharp corners in the design may add stress to a cantilever, which may raise the probability of the joint breaking off.
-
Constant stress on plastics and thermoplastics tends to cause creeping (deformation). Creep will eventually weaken the snap-fit or even compromise it entirely.
-
Misplaced gaps in parts will cause tolerance issues, in turn making it harder for components to fit together.
-
The more you assemble and disassemble snap-fit joints, the more likely you are to come across fatigue failure.
In general, snap-fits will encounter the most stress during attachment and should return to their neutral position once the joining process is completed. Depending on the shape of the undercut, snap-fit assemblies can also be designed to make them permanent. A well-designed snap-fit with suitable material can be used many times without any noticeable fatigue.
What are the right tolerances for snap-fit joints?
3D printing properties can vary quite a bit, from printer calibration and materials to the printer technology itself. Because of these varying factors, there are no strict tolerancing rules for printing snap-fit joints and connectors.
While there are no set rules, we do recommend the following optimal tolerances for different types of 3D printers.
-
For FDM (fused deposition modeling): 0.5mm
-
For SLA (stereolithography), SLS (selective laser sintering) and MJF: 0.3mm
What are the best practices for designing 3D-printed snap fits?
When designing snap-fit joints for 3D printed parts, it is important to consider features that will reduce stress and strain on the snap-fit assembly. Here are some of our best practices for designing snap-fit joints for 3D printing.
Taper the design
A snap-fit cantilever with a constant cross-section has an uneven distribution of strain. We recommend reducing the cross-section of the cantilever beam over its length. This uses less material and results in more even distribution of strain across the entire cantilever.
Fillet the base of the cantilever:
Adding a fillet at the base of a cantilever will help distribute stress over a broader area, resulting in a stronger connection between snap-fit components. The radius of the fillet should be at least 0.5 times the thickness of the cantilever’s base.
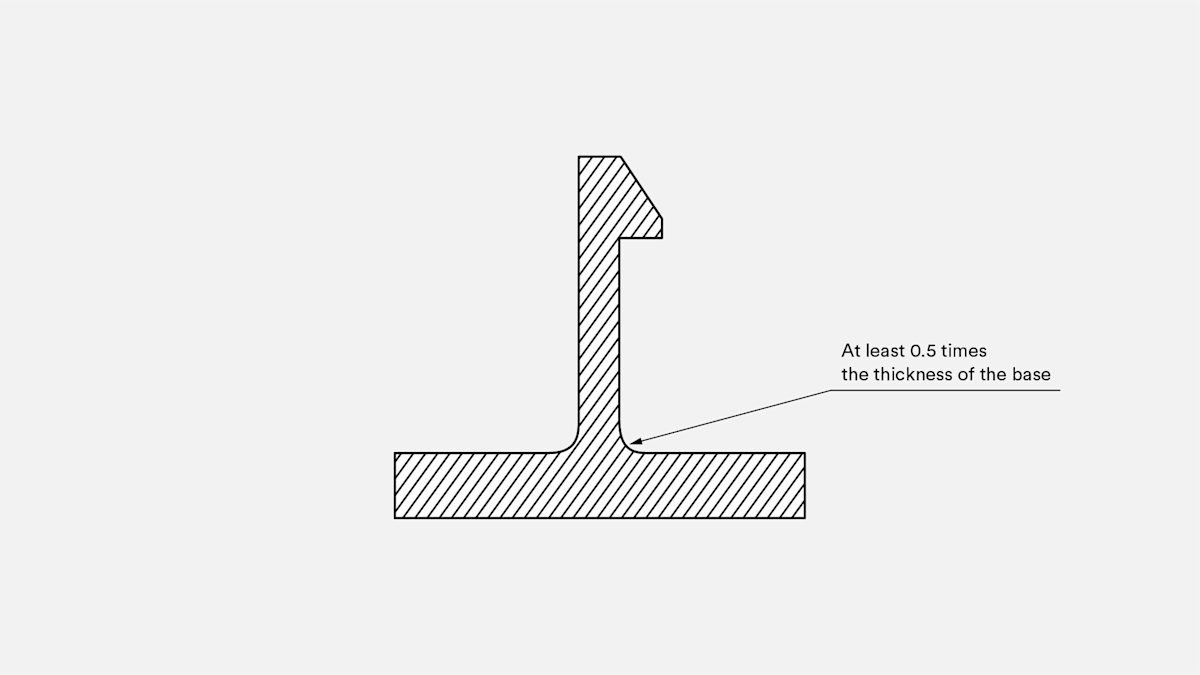
Increase the width:
Increasing the width of the clip, if it’s feasible given any design constraints, makes the design stronger. You may need to iterate several times to get the right part stiffness, and remember that the clip should be at least 5mm wide.
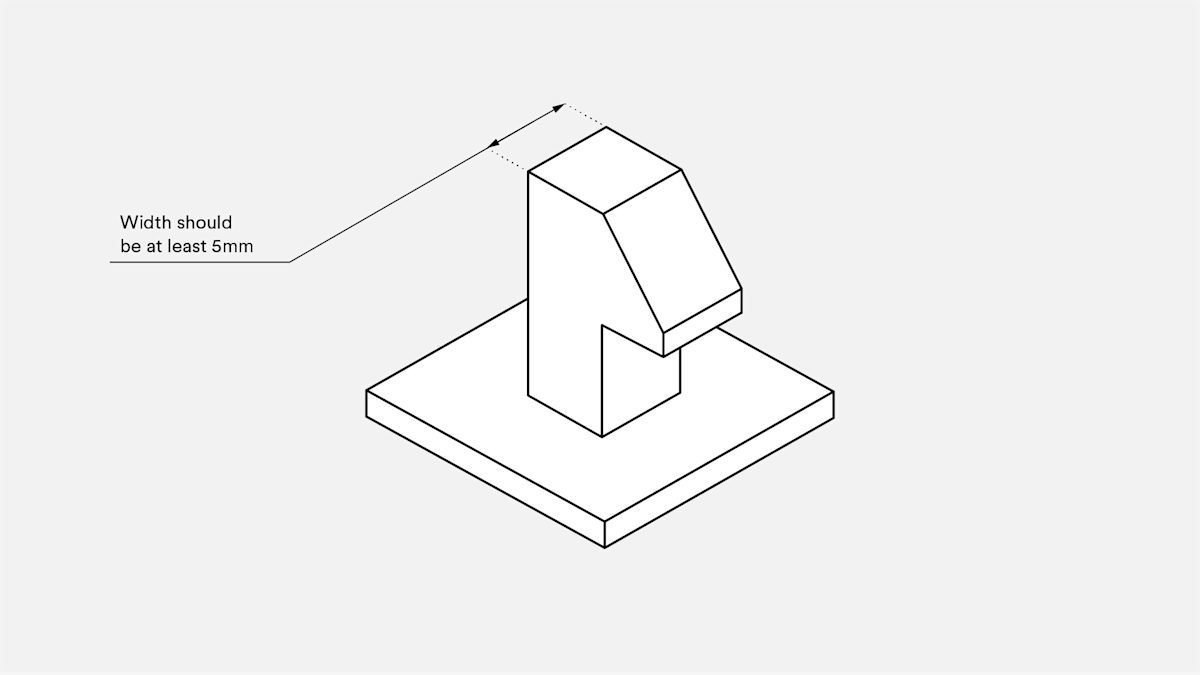
Deflect during assembly:
To help reduce stress and improve the strength of the connection, make sure that the snap-fit cantilever is only deflected during assembly rather than when the components are connected.
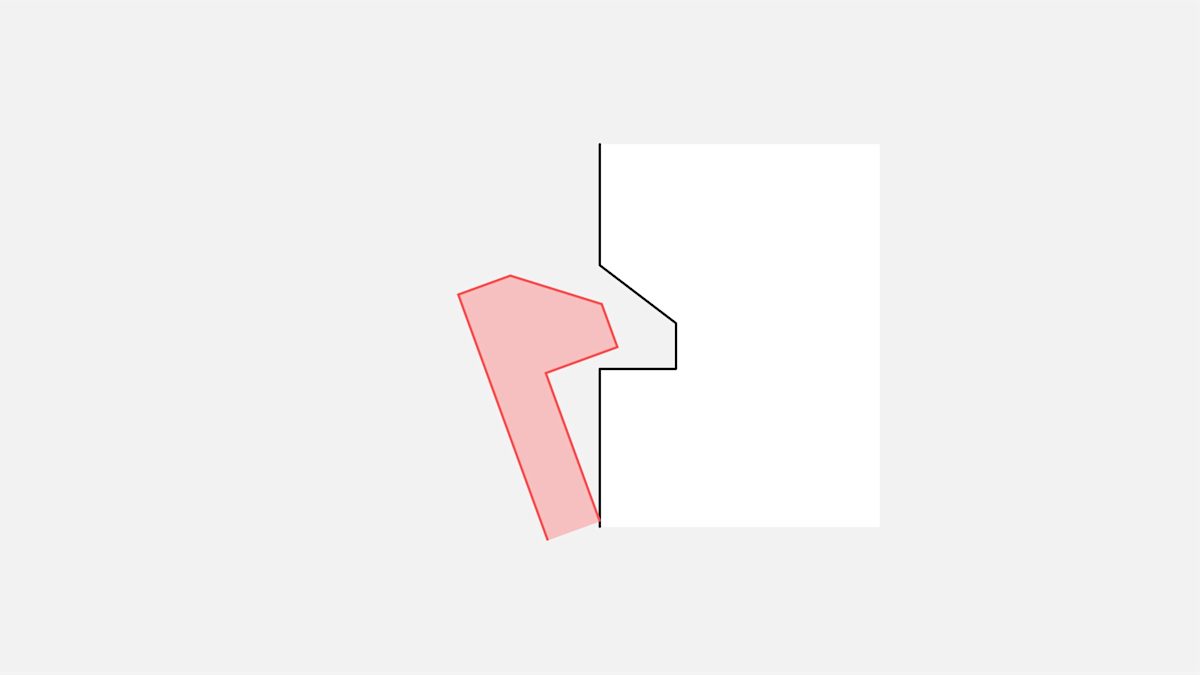
Consider build direction:
If possible, avoid designing snap-fit cantilevers that are built up vertically (in the z-direction). These are inherently weaker due to the anisotropic nature of 3D printing.
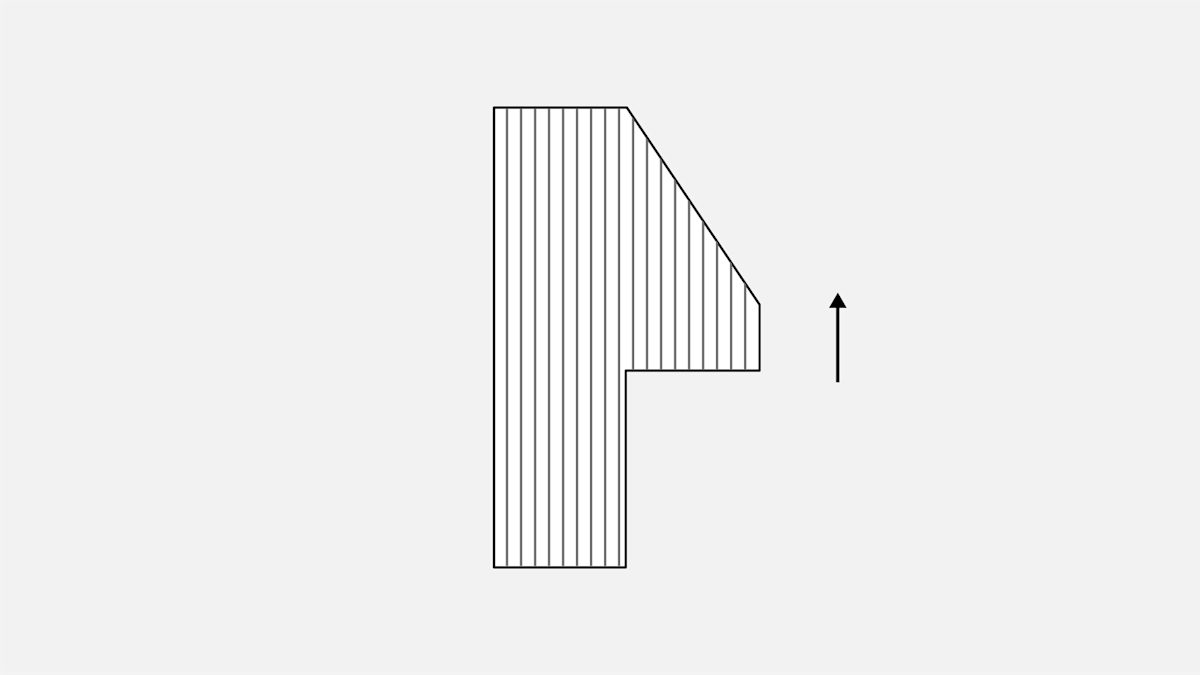
Add lugs:
Consider adding lugs to your assembly to assist with the alignment of components and to transfer some of the shear load your snap-fit clips may be subjected to.

Our top tips & tricks for designing snap-fit joints
-
Sound design principles can make or break your snap-fit joints. Remember to implement good design practices that reduce stress (fillets, build direction and locating lugs) and strain (tapered profiles and cantilever width).
-
Choose the right tolerances for different 3D printers. Use 0.5mm tolerances for FDM snap-fit connectors and 0.3mm for all other 3D printing processes.
-
Do your materials homework beforehand. Prototyping plastics are ideal for design confirmation, but they are typically weaker than SLS or material jetting materials. Think about functional or end-use materials for applications where the connector will be opened and closed repeatedly.
To explore 3D printing further, check out our full guide for a comprehensive overview and detailed design and manufacturing tips.
If you're ready to get your parts into production, you can head straight to the Protolabs Network platform to get an instant quote and explore our onboard DFM analysis. You can also reach out to networksales@protolabs.com for more information and get matched with a specialized account manager.
Frequently asked questions
What are snap-fit joints used for?
Snap-fit joints are used to simply and cost-effectively connect components of 3D-printed and injection molded plastic parts.
How long do snap-fit joints last?
Because of the bending motion required for functionality, snap-fit joints have a limited lifespan. This lifespan depends a lot on the technology and materials used, though it’s important to note that proper design and printing methods can produce snap-fits that easily rival injection-molded connectors.
What materials are best for designing snap-fit joints?
Flexible materials like ABS, PETG and Nylon are optimal for snap-fit connectors, as opposed to more brittle materials like PLA and standard SLA resins. You can use any of these materials, depending on the type of snap-fit you’re hoping to produce.
What are the right tolerances for snap-fit joints?
If you’re using FDM, use a tolerance of 0.5mm. For all other 3D printing machines, use a tolerance of 0.3mm.
Is 3D printing better than injection molding for producing snap-fit joints?
3D printing snap-fit joints comes with far fewer design limitations than injection molding, which makes it especially optimal for rapid prototyping applications.
How do you design better snap-fit joints for 3D printing?
If you’re designing snap-fit joints for 3D printing, the name of the game is to reduce stress on the assembly. Ways to do this include tapering the design, filleting the base (for cantilever joints) and adding lugs to the design.
What's the best material for 3D printing snap-fit joints?
For many applications, we recommend using SLS nylon for its impressive tear resistance.