3D printing is a clear fit for many prototyping and end-use applications within the aerospace and aviation industry. Parts produced via additive manufacturing can be stronger and lighter than those made using traditional manufacturing.
Aerospace was a very early adopter of 3D printing and still continues to contribute heavily to its development. Companies in this industry began using 3D printing in 1989, and in 2015, aerospace accounted for 16% of additive’s $4.9B global revenue.
In this article, we explore how 3D printing has made an impact on the aerospace industry. We go over design requirements for parts used in airplanes and give design recommendations for common and more niche aerospace and aviation applications. As well, we cover the best materials for 3D printing parts for this industry and examine one of our favorite case studies.
Implementing 3D printing in the aerospace design workflow
Designers and engineers creating new products in aerospace and aviation can implement 3D printing at all stages of the design workflow. Let’s break down all the major stages.
Design communication
Designs in the aerospace industry often begin as concept models showcasing a component of an aircraft. These are often also regularly used for aerodynamic testing, which is of critical importance for aerospace. SLA printing and Material Jetting are used to produce high detail and smooth scale models of aerospace designs. Accurate models allow design intention to be clearly communicated and showcase the overall form of a concept.
Validation
Prototyping using 3D printing is now commonplace in the aerospace industry. From a full-size landing gear enclosure printed rapidly with low-cost FDM, to a high-detail, full-color control board concept model, there is a 3D printing process suited to every prototyping need. Engineering materials for 3D printing also allow for full testing and validation of prototype performance.
Pre-production
One of the areas where 3D printing has been most disruptive and valuable is the production of low-cost rapid tooling for injection molding, thermoforming and jigs and fixtures. Within aerospace, this allows for tooling to be quickly manufactured at a low cost and then used to produce low to medium runs of parts. This validation mitigates the risk when investing in high-cost tooling at the production stage and can also provide production components for quantities up to 5,000 to 10,000 parts.
Production
Production volumes in the aerospace industry can reach more than 70,000 parts per year, so 3D printing has predominantly been used in the past as a prototyping solution rather than the manufacturing of end-use parts.
Today, improvements in the size of industrial printers, the speed they are able to print at and the materials that are available all make 3D printing a viable option for more medium-sized production runs, particularly for high-end interior build-outs.
Customization
3D printing technologies significantly impact the aerospace industry when a substantial improvement in aircraft performance can justify the cost of highly complex one-off components.
The average corporate aircraft travel 75,000 miles per month and a single component that was designed and manufactured with 3D printing can reduce air drag by 2.1%, reducing fuel costs by 5.41%. And that’s just the impact of one 3D-printed part.
Parts can be tailored to a specific aircraft (custom, lightweight bracketry) or type of aircraft (cargo, passenger or even helicopter). 3D printing also provides part consolidation and topology optimization of many custom aerospace components.
How is 3D printing used in aerospace engineering?
Jigs & Fixtures
Big benefits exist for several more mundane 3D printing applications, including the production of jigs and fixtures. For each individual aircraft, companies have hundreds of fixtures, guides, templates and gauges 3D printed, generally with 60 to 90 percent reductions in cost and lead time compared to other manufacturing processes.
Surrogates
Surrogates are placeholder parts used throughout production that represent components that are later installed in final assemblies. Surrogates are mainly used for training. NASA and several Air Force bases commonly use surrogate parts on the production floor.
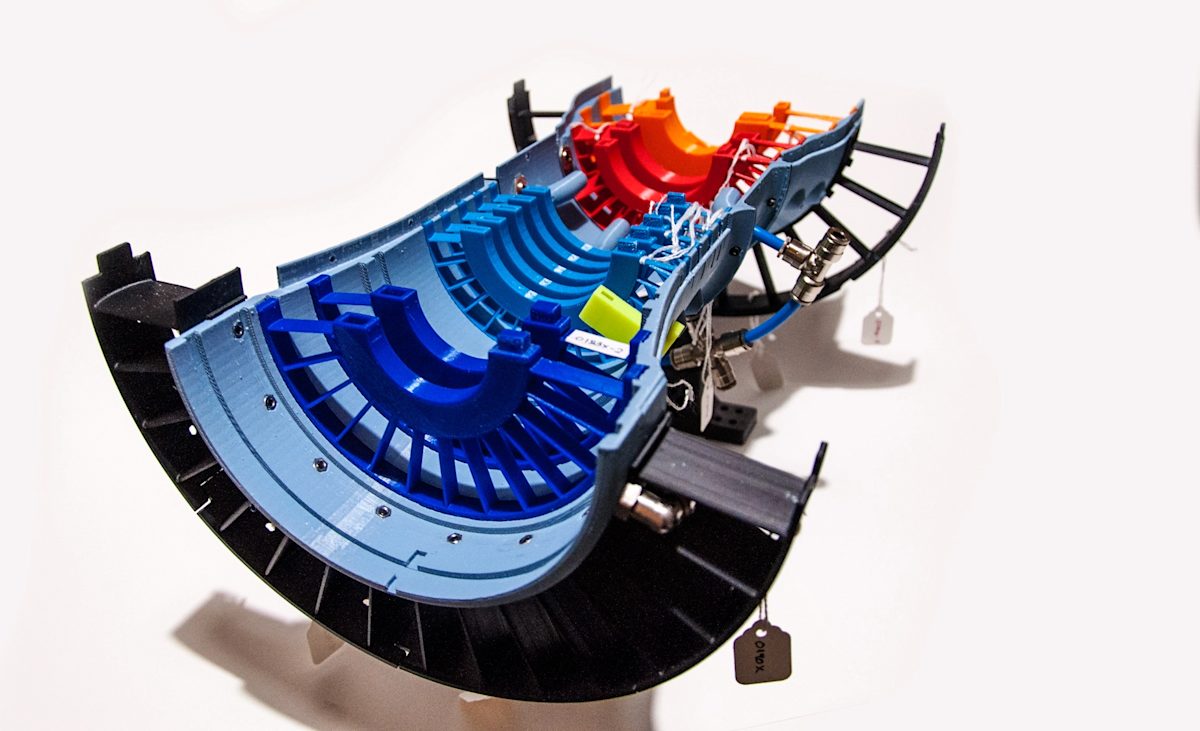
Mounting brackets
3D printing is commonly used to manufacture structural, low-volume metal brackets (with DMSL/SLM) that mount complex life-saving systems to the interior wall of a plane.
High detail visual prototypes
3D printing with Material Jetting is able to produce multicolor designs with a surface finish comparable to injection molding. These visually appealing models allow designers to get a greater understanding of the form and fit of a part before making important production decisions.
This highly accurate method of prototyping is also ideal for aerodynamic testing and analysis, as the surface finish you get with 3D printing is often representative of a final part.
3D printing is used routinely to manufacture aerospace components that rely on aesthetics over function, such as door handles and light housings to control wheels and full interior dashboard designs.
How does 3D printing improve aerospace manufacturing?
Geometric design freedom
Aerospace applications make use of advanced engineering materials and complex geometries in an attempt to reduce weight while improving performance. Aerospace parts frequently include internal channels for conformal cooling, internal features, thin walls and complex curved surfaces.
3D printing is capable of manufacturing such features and allows for the fabrication of highly complex and lightweight structures with high stability. This high degree of design freedom enables the topological optimization of the parts and the integration of functional features in a single component.
Also, certain 3D printing technologies, such as SLS, DMSL/SLM and Binder Jetting, are capable of small batch production at reasonable unit costs.
Consolidating assemblies into a single part
The design freedom you get with the 3D printing process also helps to consolidate multiple parts into a single component. This leads to weight savings (and thus cost reduction) and also reduces the amount of inventory kept at any time.
Surface finish
Having the right surface finishes is critical for the aerospace industry, and 3D-printed parts can be post-processed to a very high surface finish. Some technologies, such as Material Jetting, can produce parts with a smooth, injection-molding-like finish off the printer with little post-processing needed. High-performance metal parts produced with DMSL/SLM or low-cost metal parts produced with Binder Jetting can also be smoothed and polished (or even CNC machined) after printing to improve their accuracy and surface finish.
Part orientation
For functional parts that will bare load, part orientation in the build platform is very important. Due to the layer-by-layer nature of 3D printing, most parts will have anisotropic mechanical properties and will be weaker in the Z direction. This should be taken into consideration during the design process.
Support structures
Support structures are used in 3D printing to provide a solid base for depositing material above overhangs or at walls with steep angles (above 45 degrees). Support is also crucial in metal 3D printing, as it anchors the parts in the build plate and protects against warping.
The areas printed on supports will have a lower surface finish and some marks from the support removal. If this is suboptimal for your parts, there are processes that do not require support structures, such as SLS and Binder Jetting.
What are the best materials for 3D printing aerospace and aviation parts?
Check out this table for a more in-depth comparison of materials used to 3D print custom aerospace and aviation components.
Application | Example part | Requirements | Recommended Process | Recommended Material |
---|---|---|---|---|
Engine compartment | Tarmac nozzle bezel | Heat resistant functional parts | SLS | Glass-filled Nylon |
Cabin accessories | Console control part | Customized functional knobs | SLA | Standard Resin |
Air ducts | Air flow ducting | Flexible ducts and bellow directors | SLS | Nylon 12 |
Full size panels | Seat backs & entry doors | Large parts with smooth surface finish | SLA | Standard Resin |
Casted metal parts | Brackets and door handles | Metal parts casted using 3D printed patterns | SLA & Material Jetting | Castable Resin or Wax |
Metal components | Suspension wishbone & GE Jet Engine | Consolidated, lightweight, functional metal parts | DMLS/SLM | Titanium or Aluminum |
Bezels | Dashboard interface | End use custom screen bezels | Material Jetting | Digital ABS |
Lights | Headlight prototypes | Fully transparent, high-detail models | Material Jetting & SLA | Transparent Resin |
3D printing in practice: Printing parts for satellites
Satellite designs include geometrically specific brackets that link the body of the satellite with reflectors and feeder facilities mounted at each end. Manufacturing these critical brackets comes with two distinct challenges.
These brackets must affix reflector and feeder facility components securely to the body of the satellite. As well, these brackets must be able to withstand the stress of insinuating against temperatures ranging from -170 to 100 degrees celsius. Very few materials can meet the requirements for the amount of stress these brackets endure.
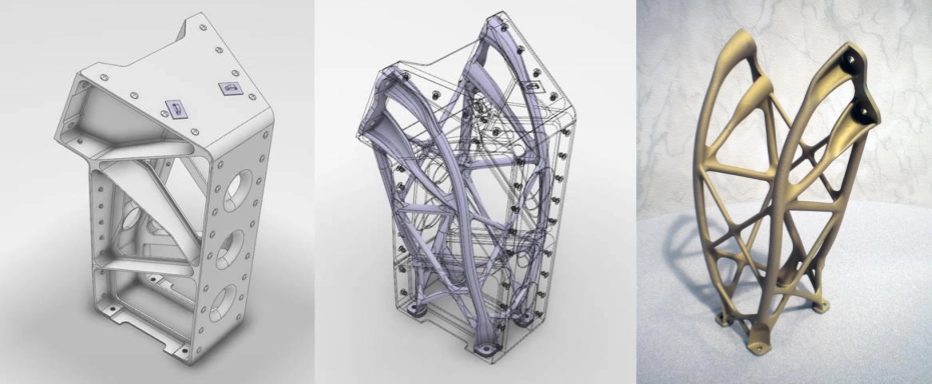
Engineers at Airbus overcame these challenges by 3D printing these brackets using titanium. By opting to manufacture the brackets the additive way, the engineers at Airbus cut down on material waste, consolidated parts (making assembly easier and less labor-intensive), optimized part geometries and ended up with lighter-weight components. 3D printing helped reduce costs to produce parts and will save fuel over the life cycle of the satellites thanks to the lighter weight of the components.
Ready to make custom parts faster & lighter?
Explore our 3D printing capabilities Get a free, instant quote today