Industrial SLA/DLP vs. desktop SLA/DLP
SLA/DLP technology is used by both low-cost desktop 3D printers as well as high-end industrial 3D printers. This article will help you select the right type of machine for your application.
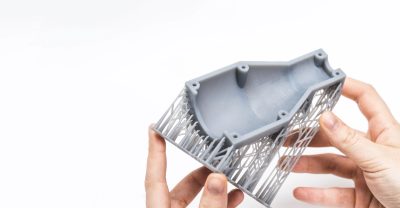
Introduction
Stereolithography (SLA) and digital light processing (DLP) printers make use of the oldest 3D printing technology - vat photopolymerisation. Both technologies use light to cure and harden specific areas of resin to form a solid part. SLA printers do this with a laser that travels over the cross sectional area of each layer of the part while DLP printers use a digital light projector screen to flash a single image of each layer all at once. There are a large range of SLA & DLP printers available, suitable for applications ranging from small enclosures to full scale car bumper prototypes.
This article will discuss the main differences between the typical desktop and industrial SLA/DLP 3D printers and offer guidance on selecting the right machine for an application.
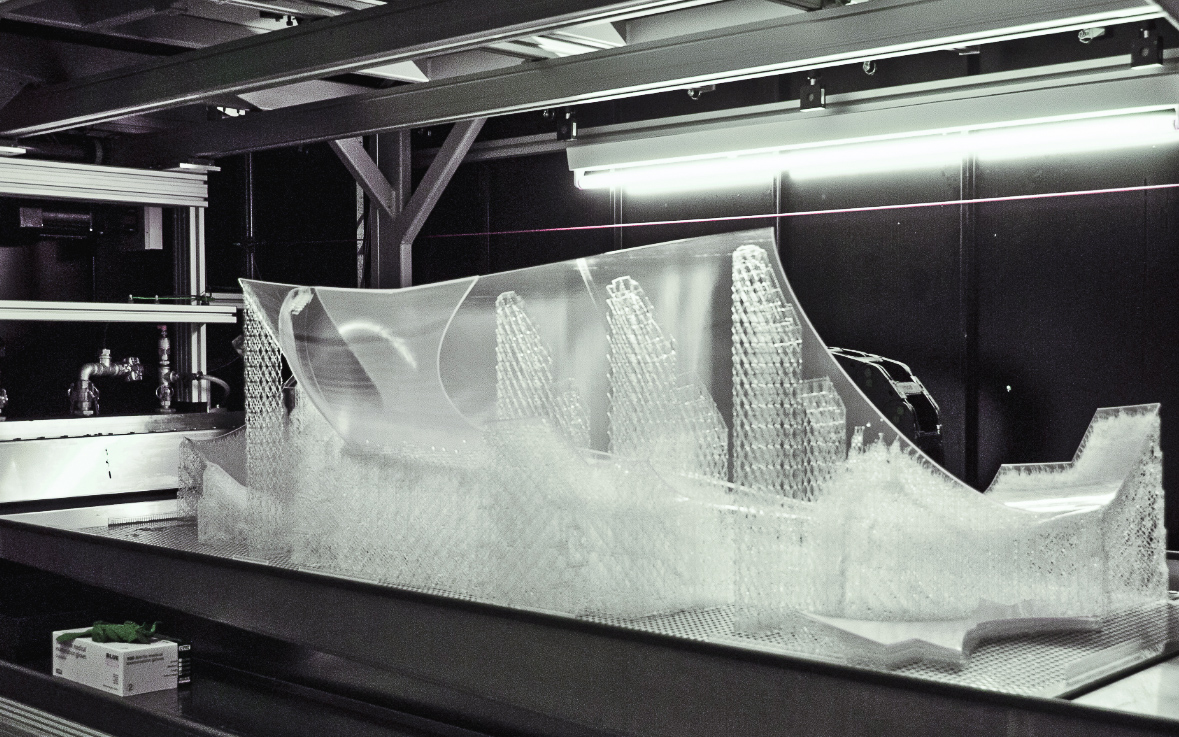
Accuracy
Industrial SLA and DLP printers are capable of producing more accurate parts than desktop machines. Industrial machines typically produce parts in a controlled environment, use machine specific materials and are constructed from high cost components. While desktop SLA or DLP are able to produce parts with a tolerance of 150 - 300 microns (with this increasing significantly over larger parts), industrial machines are capable of tolerances as low as 30 microns for any build size.
To accurately produce parts both SLA and DLP desktop and industrial printers require support material. If accuracy of part is critical, optimising support location and geometry is very important. Advice on designing parts for SLA can be found here.
Selection tip: Industrial SLA or DLP printers are more accurate than desktop and maintain better accuracy over larger builds. All prints produced via SLA or DLP require support.
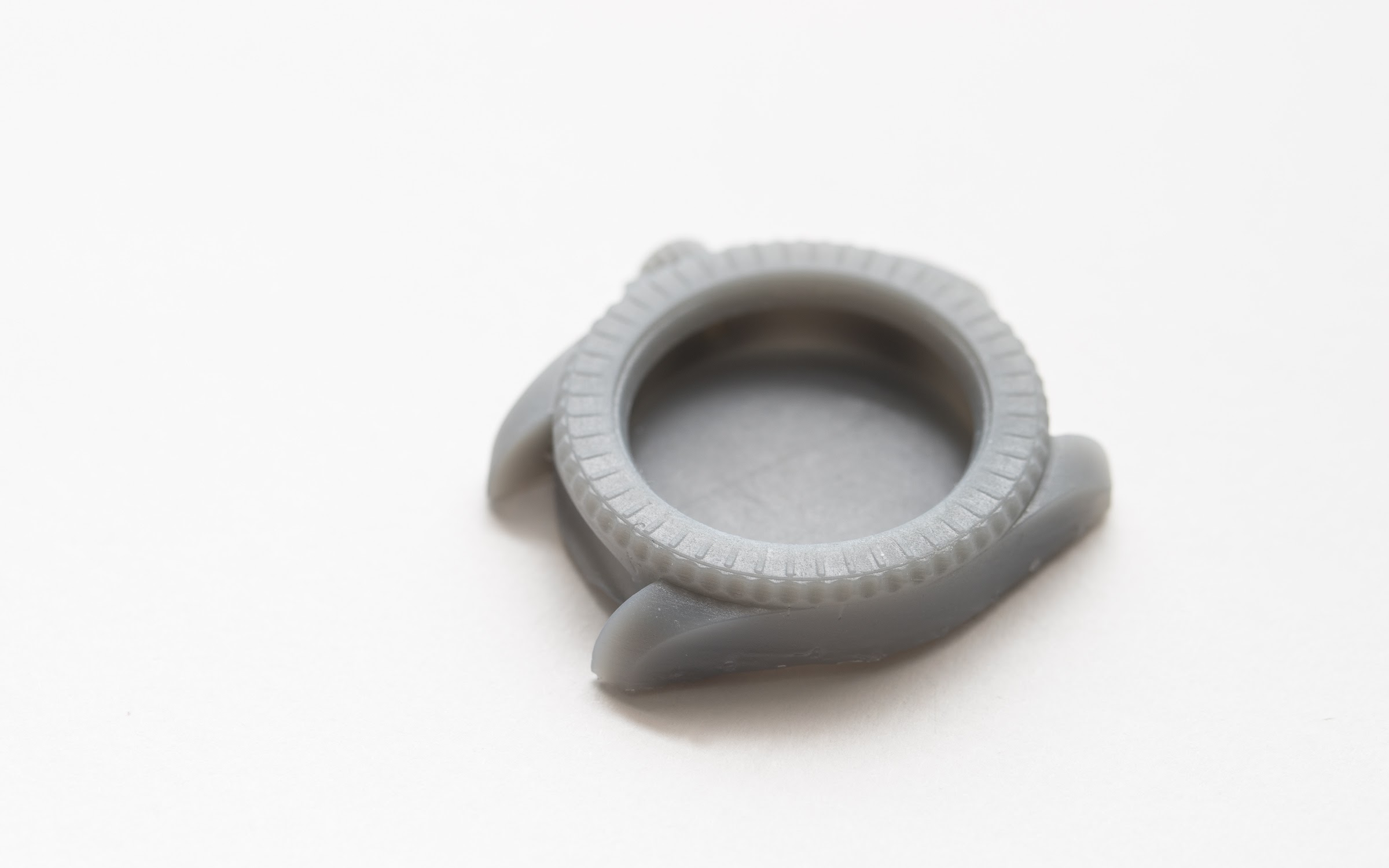
Materials
One of the biggest advantages of industrial SLA/DLP over desktop machines is the range of materials that industrial printers are able to print with. While desktop printers may offer a flexible resin, industrial machines offer a large range of flexible resins each with varying mechanical properties (Shore Hardness, high temperature etc.). SLA and desktop machines offer the most extensive range of materials out of all of the 3D printing technologies.
Resin type | Desktop | Industrial |
---|---|---|
Castable | VisiJet FTX Cast, VisiJet SL Jewel, Formlabs Castable | Accura Amethyst, Accura CastPro, Accura Sapphire, DWS DC 700, DWS RF, EnvisionTEC EC500, EnvisionTEC EC500, EnvisionTEC PIC100, Somos Element |
Clear | VisiJet FTX Clear, VisiJet SL Clear, Formlabs Clear | Accura 60, Accura ClearVue, Asiga PlasCLEAR, EnvisionTEC E-Glass 3SP, Somos 9120, Somos WaterClear, Somos Watershed |
ABS/polypropylene-like | VisiJet SL Tough, Carbon3D RPU 60, Formlabs Tough | Accura Xtreme, Accura 55, Accura ABS, Accura PP, DWS AB, EnvisionTEC ABS, Somos 9420, Somos 14122, Somos EvoLVe, Somos NeXt |
Dental | VisiJet e-Stone, Formlabs Dental SG | Accura e-Stone, Detona Pro3dure, DWS DS2000, DWS RF, DWS RD095 |
Flexible | Carbon3D EPU 40, Formlabs Flexible | EnvisionTEC ABS 3SP Flex, DWS GM08 |
Curious about the cost of SLA and the available material options?
One of the limitations of most industrial machines is that they produce parts using a top-down approach resulting in the need for large resin tanks (over 100L). This makes swapping between materials difficult and can increase lead time on parts. This also makes these machines more expensive to maintain.
All SLA and DLP resins are susceptible to UV degradation over time, however, coatings applied after printing can help to mitigate this.
Selection tip: For designs where appearance is more important than function desktop printers are generally adequate. If engineering properties like temperature resistance, castability, transparency etc. are required then industrial properties offer a greater range of solutions.
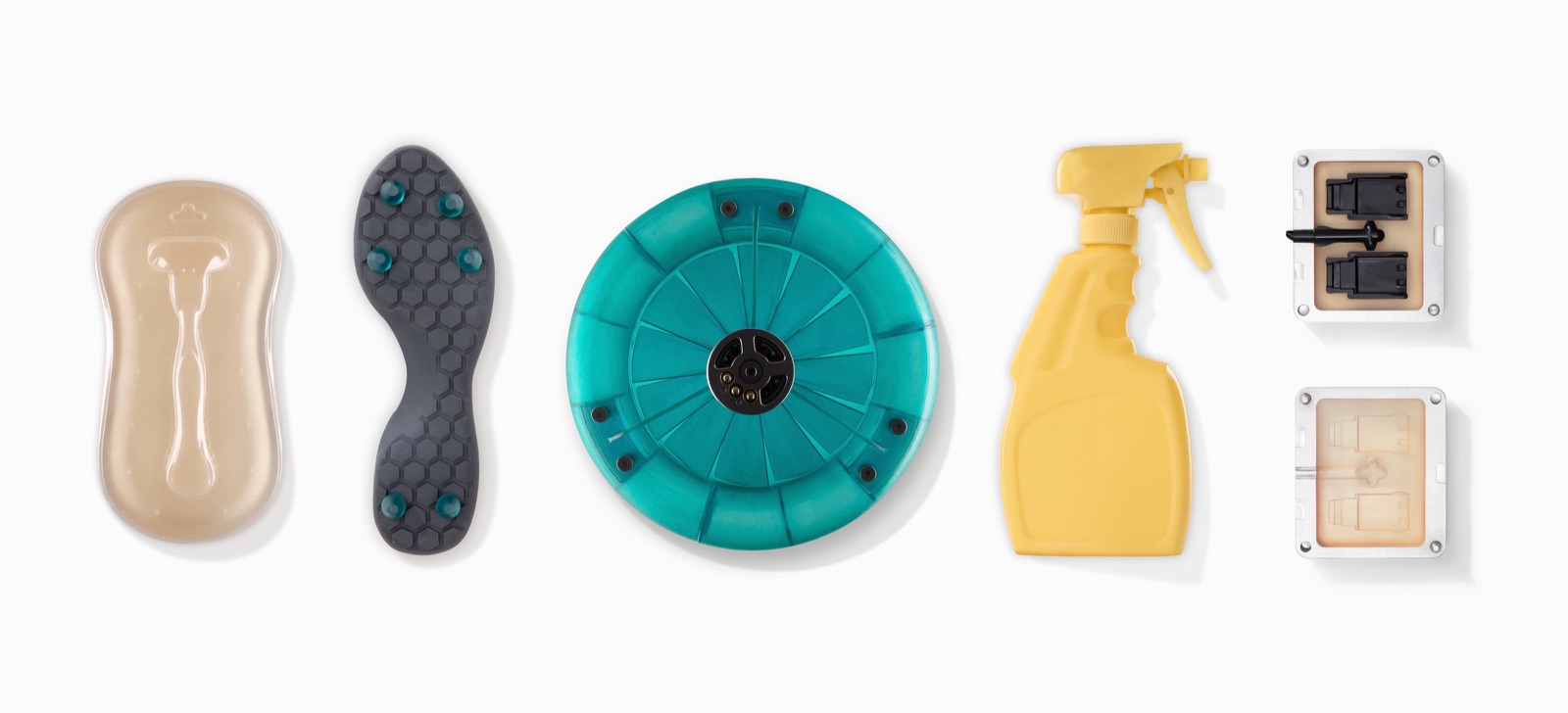
Production capabilities and cost
One of the benefits of 3D printing is that the layer by layer method of production allows for multiple parts to be created in a single build. One of the advantages of SLA and DLP printers is that there is no loss of quality when producing multiple parts on a single build platform. The parts produced are generally homogeneous and do not experience any of the anisotropic issues that relate to other 3D printing technologies.
Compared to desktop printers, industrial machines are designed for repeatability and reliability. They can often produce the same part over and over again and do not need the high level of user interaction that desktop machines typically require.
Industrial SLA and DLP machines are also capable of printing models without visual build lines requiring almost no post-processing (other than support material removal), which, when compared to other 3D printing technologies can greatly reduce lead time. Desktop printers require a high level of user maintenance and more post-processing of the prints.
The ability to batch produce intricate, customized parts make industrial SLA and DLP a popular method of manufacturing small parts, low-run production.
Selection tip: The bigger build volumes offered by industrial printers has seem them adopted as a viable means of batch manufacturing in the dental, jewelry and hearing aids industries.
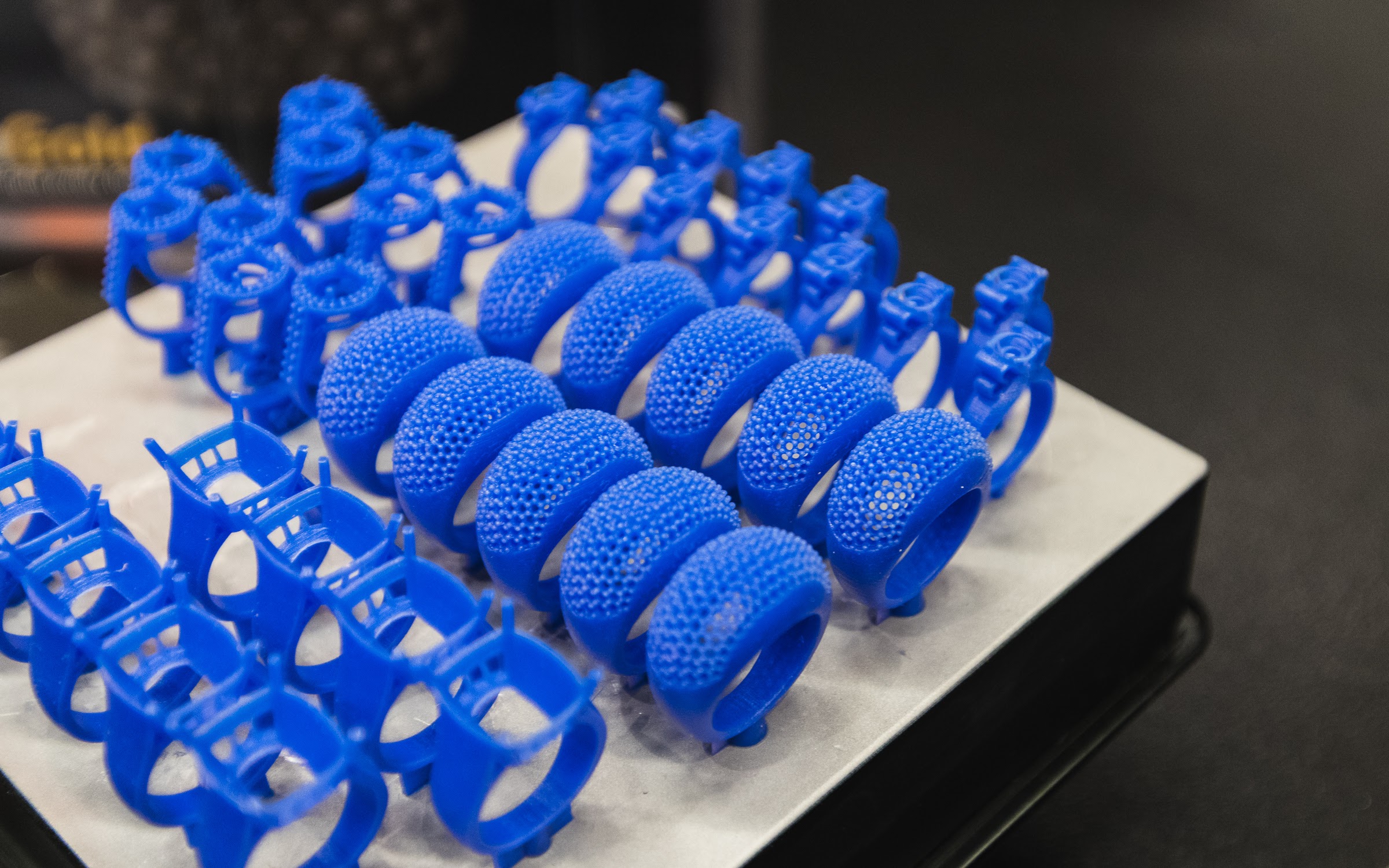
SLA/DLP expectations
SLA and DLP produce parts with smooth surfaces and high level of detail. Prints are often brittle making SLA and DLP best suited for non-functional parts or visual models. The requirement for support means that post-processing is always required. Industrial SLA/DLP machines are capable of printing finer supports with greater overhangs resulting in less post processing and better surface finishes.
Summary table
The table below gives a comparison of typical desktop SLA/DLP printers and typical industrial SLA/DLP machines.
Property | Desktop DLP | Desktop SLA | Industrial DLP | Industrial SLA |
---|---|---|---|---|
Standard accuracy | 30 - 140 microns | 240 microns | 10 - 100 microns | 30 - 140 microns |
Typical layer thickness | 5 - 150 microns | 25 - 200 microns | 25 - 150 microns | 50 -100 microns |
Minimum wall thickness | 0.1 mm | 0.5 mm | 0.1 mm | 0.1 - 0.3 mm |
Minimum feature size | 10 - 200 microns | 300 microns | 10 - 100 microns | 75 microns |
Surface finish | ★ ★ ☆ ☆ ☆ | ★ ★ ★ ☆ ☆ | ★ ★ ★ ★ ★ | ★ ★ ★ ★ ☆ |
Maximum build envelope | Small (e.g. 58 x 32 x 127 mm) | Medium (e.g. 145 x 145 x 175 mm) | Small - Large (e.g. 48 x 28 x 100 - 192 x 120 x 230 mm) | Extra large (e.g. 2100 x 700 x 800 mm) |
Common resins | Clear, castable, dental | Clear, castable, dental, flexible, tough | Clear, castable, dental, flexible, wax-like, ABS-like | Clear, castable, dental, flexible, wax-like, ABS-like |
Production capabilities (per machine) | Low | Low | Medium | High |
Machine cost | $2,500 - $5,000 | $2,000 - $15,000 | $15,000 - $85,000 | $100,000 - $500,000 |
Curious about the cost of SLA and the available materials options?
Rules of thumb
- For small, accurate, visual prototypes that require smooth surfaces desktop SLA and DLP printers offer a fast, low cost solution.
- For large parts that also require mechanical properties or a higher level of accuracy, industrial SLA and DLP machines are the best solution.
- When the design has a lot of overhanging features or very fine details are not needed, SLS 3D printing should be considered.