How to design interlocking joints for fastening 3D printed parts
Learn how to design and 3D print interlocking joints (e.g. finger-, dovetail- and puzzle joints) to assemble your 3D printed parts.
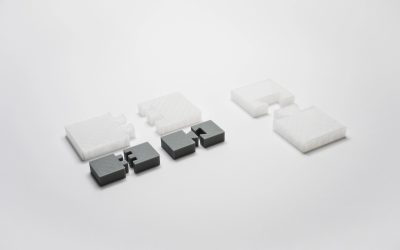
Introduction
Interlocking joints are a common method for connecting components that are regularly assembled and disassembled. The use of interlocking joints allows:
- The ability to quickly assemble/disassemble components.
- A reduction in the the number of components in an assembly.
- A simple method for connecting multiple parts together where printer limitations such as overhangs, bridges or support removal interfere with the quality of a print.
- The ability to print assemblies in multiple colors and materials.
This article will discuss the common applications of interlocking connections used in 3D printing, and recommend the 3D printing processes most suited to interlocking joint production.
3D printing technologies and interlocking joints
The table below provides a quick overview of the most common 3D printing technologies and whether they are appropriate for printing interlocking joints:
Process | Description |
---|---|
FDM | Low cost and effective way of manufacturing interlocking joints but lower accuracy than other printing methods. ABS better suited than PLA due to its improved ductility |
SLA | High accuracy but can be very brittle unless using a “tough resin” |
SLS | Good for interlocking parts as parts have high print accuracy and good strength |
Material Jetting | Good strength and elasticity combined with high resolution details makes material jetting ideal for interlocking applications |
Binder Jetting | Not suited for interlocking connections |
Designing for interlocking joints
There are 3 forces to consider when designing interlocking joints:
-
Friction - the critical force that holds the joint together. The tighter the joint is, the higher the friction and the more difficult it will be to pull apart
-
Tension - the force that acts to pull the joint apart
-
Shear - the force perpendicular to tension that pulls the joint sideways (a tearing force)
Interlocking joints accuracy
When interlocking joints are manufactured in injection molding, a tolerance of 0.1mm is applied. For 3D printing, tolerances vary between technologies as summarized in the table below.
Process | Interlocking parts tolerances |
---|---|
FDM | 0.5 mm |
SLA | 0.2 mm |
SLS | 0.2 mm |
Material Jetting | 0.1 mm |
Rules of thumb
- SLS and Material Jetting are best suited for interlocking joints due to their high print accuracy and material strength.
- FDM is good for low cost prototyping of interlocking connections when accuracy and durability are not critical.
- Including a small radius on the edges of parts will assist with assembly of joints.