-
Cosmetic finishes will follow our Cosmetic Acceptability Criteria
-
Parts will have guaranteed consistency across the batch
-
Batch will be inspected as per AQL level II
-
There will be around a +10% price increase
Surface finishing service
The easiest way to source your custom parts, with 15+ surface finishing options. Get your parts bead blasted, anodized, or powder coated.
Name |
Service |
Applicable to |
Machining marks |
Cosmetic availability |
Tolerances |
|
---|---|---|---|---|---|---|
|
CNC machining, Sheet metal fabricat ion |
Metals, Plastics |
Visible, light surface scratches |
No |
Tolerances are not affected |
|
|
CNC machining |
Metals, Plastics |
Visible, light surface scratches |
No |
Tolerances are not affected |
|
|
CNC machining |
Metals |
Slightly visible |
No |
Tolerances are not affected |
|
|
CNC machining |
Metals |
Removed on primary surfaces |
Always cosmetic |
Met after polishing |
|
|
CNC machining, Sheet metal fabrication |
Metals |
Removed for non-cosmetic, removed on primary surfaces for cosmetic |
On request |
Not affected except for specific features* |
|
|
CNC machining, Sheet metal fabrication |
Metals |
Reduced for non-cosmetic, removed on primary surfaces for cosmetic |
On request |
Met after brushing |
|
|
CNC machining, Sheet metal fabrication |
Aluminum |
Reduced for non-cosmetic, removed on primary surfaces for cosmetic |
On request |
Met after anodizing |
|
|
CNC machining, Sheet metal fabrication |
Aluminum |
Visible under anodizing |
No |
Met after anodizing |
|
|
CNC machining, Sheet metal fabrication |
Copper, Stainless steel, Alloy steel, Tool steel, Mild steel |
Visible |
No |
Met after coating |
|
|
CNC machining, Sheet metal fabrication |
Aluminum |
Visible |
No |
Met after coating |
|
|
CNC machining |
Mild steel, Aluminum, Stainless steel |
Reduced but visible |
No |
Met after electroless nickel plating |
|
|
CNC machining, Sheet metal fabrication |
Metals |
Removed |
No |
Met before powder coating |
|
|
CNC machining |
Stainless steel |
Removed on Primary surfaces |
Always cosmetic |
Met after electropolishing |
|
|
3D printing |
Plastics |
Surface gets a smooth glossier appearance |
No |
Met before vapor smoothing |
Cosmetic finishes
Surface finishes can serve either a functional or aesthetic purpose. Surface finishes that serve both purposes are deemed cosmetic finishes, and are used for cosmetic parts. Producing cosmetic parts requires additional measures to minimize defects such as hang marks and scratches from tools.

Primary machining marks will still be visible
- As machined
- Smooth machining
- Fine machining
- Chromate Conversion Coating
- Electroless Nickel Plating
- Anodized type III (Hardcoat)
- Powder coating
- Black oxide

Finishes can be either cosmetic or non-cosmetic as per request
- Brushed + Anodizing type II
- Bead Blasted + Anodizing type II
- Bead Blasted
- Brushed

These finishes will always serve a cosmetic function
- Brushed + Electropolished
- Polishing
Defining an A and a B side
Surface finishing often leaves aesthetic defects on your parts, such as hang marks for anodizing. Defining an A- and a B-side in your design will ensure that the most important areas of your part remain free of defects.
In this image you can see how you can define an A-side and a B-side in your technical drawing:
A side: Indicates the most aesthetically important surface, typically the visible side of your product.
B side: Indicates the side that is not aesthetically important, typically the side hidden from visibility after assembly.
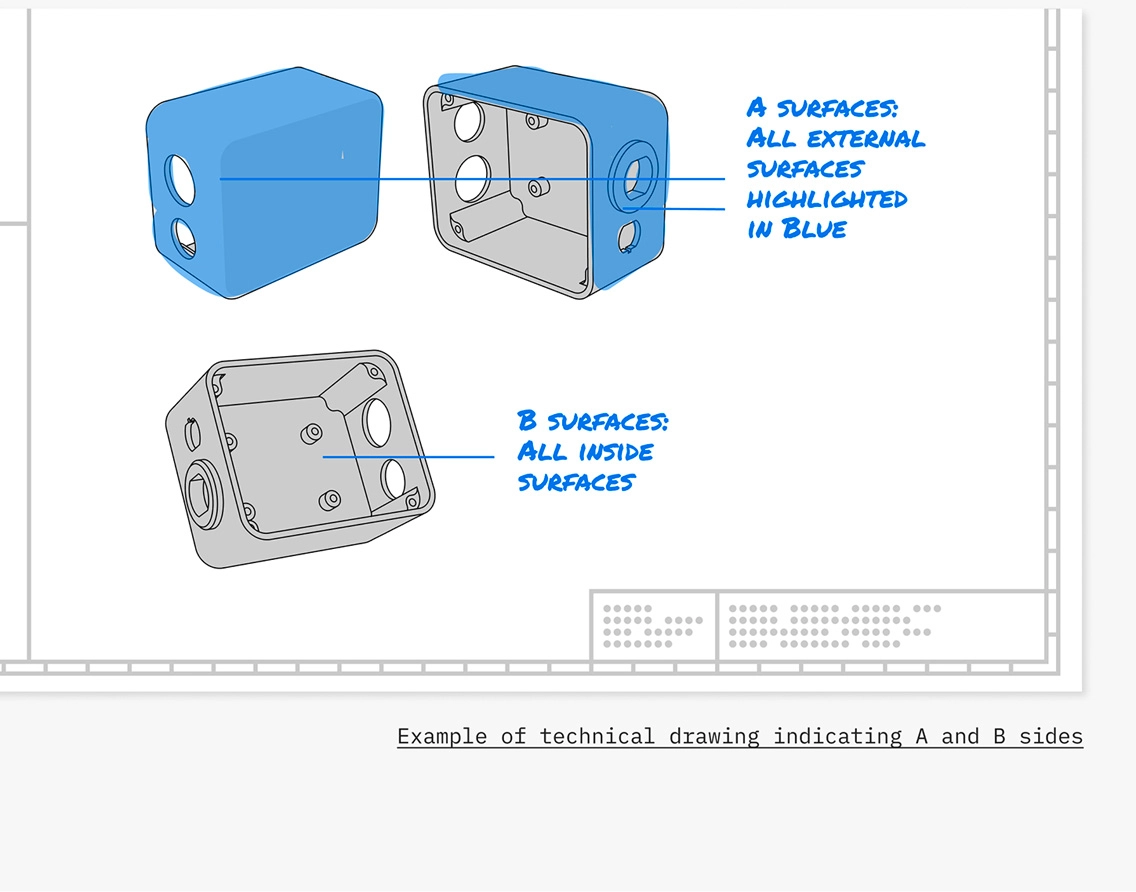
For the primary surface (A-side) of your part, we guarantee defect-free production. In contrast, secondary surfaces (B-side) may be machined with hanging marks and other minor defects. B-side surfaces, like the rest of your part, will be free of scratches, stains and blemishes.
Will my part have | Primary surface (A-side) |
Secondary surface (B-side) |
---|---|---|
Scratches, stains, blemishes | No | No |
Hanging marks | No | Minor hanging marks |
Other minor defects | No | Up to 2 minor defects |
Cosmetic Acceptability Criteria
All cosmetic parts produced by Protolabs Network follow our Cosmetic Acceptability Criteria:

Each part must be visually consistent across the same batch, meaning:
- Same grit must be used across parts for sanding or brushing
- Brush marks must be in the same direction**
- Color must be consistent to the same pantone when parts are placed next to each other
- Gloss units must be consistent across the batch
*** Manual brushing marks will be as unidirectional as possible. Please note that for rounded geometries, brushing marks may not be entirely unidirectional.*

The surface quality of every part must meet the following conditions:
- Distance: 50cm ±10cm (19,7 in ± 3,9 in) with a 10/10 vision (or corrected)
- Incidence angle: Approximately 45º in all directions
- Lighting conditions: 500-1000 Lux, color 3300-5300 Kelvin (neutral white)
What do you need to know about cosmetic finishes?
Put your parts into production today
Get instant quote