Formify is a tech startup that uses pictures of customers’ hands, proprietary software and
MJF 3D printing to produce custom-fitting, ergonomic computer mice. Based in Toronto, the company has already outfitted professional gamers with personalized mice and will launch a Kickstarter in Q2 of 2022.
The challenge
Personalized design presented a unique manufacturing challenge for Formify. The company needed to produce finely detailed and lightweight custom components that would fit comfortably in the hands of any user, in a way that would later scale significantly.
How Protolabs Network helped
Protolabs Network's automated quote builder and wide range of 3D printing technologies allowed Formify to swiftly prototype and perfect its design, while its extensive MJF (Multi Jet Fusion) capacity supports the startup’s ability to scale and produce large quantities of personalized products.
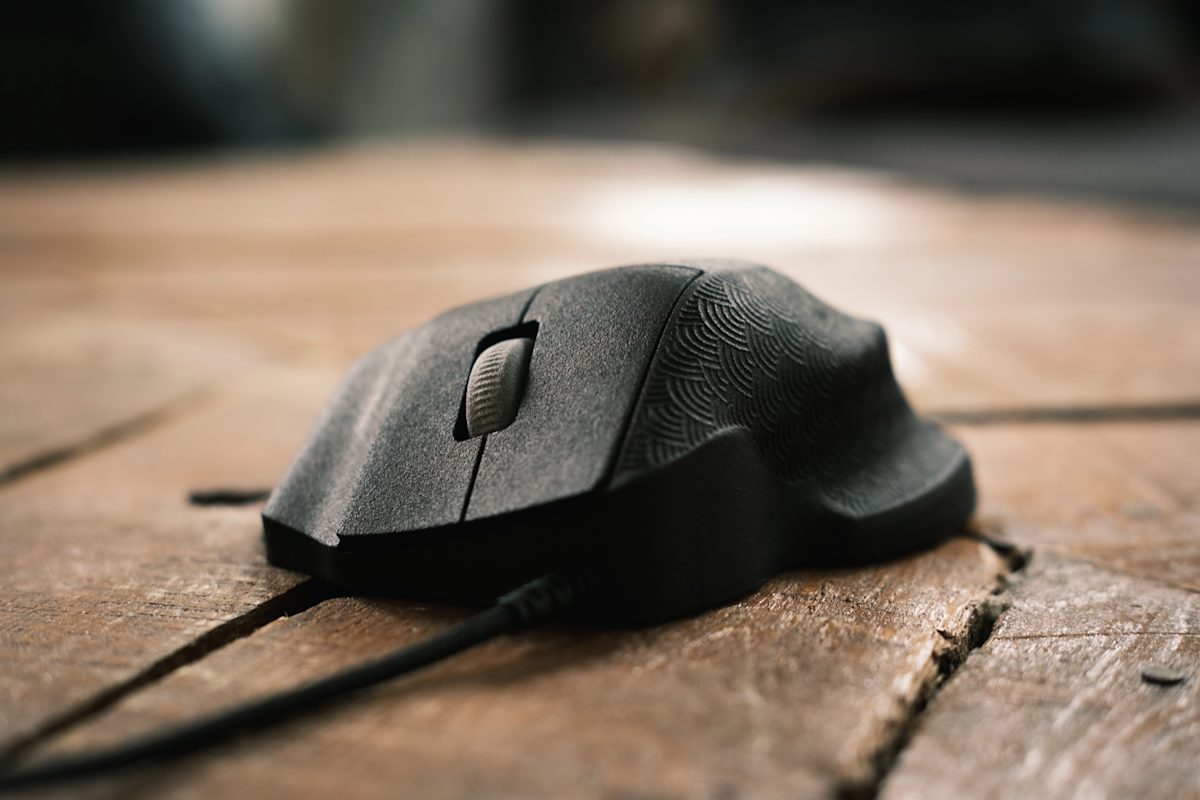
A new name in custom gaming gear
Formify started as a student project at Ryerson University and the University of Waterloo. Looking for an exciting tech problem to tackle, Will MacLaughlin, Alexander Chapman, Luke Morabito, Kenny MacLaughlin and Gianpaolo Pittis noticed that gaming peripherals like mice and VR headsets were all the same size, making them unwieldy for different types of users, especially in professional gaming.
Gaming, whether casual or professional (esports), is an enormous market intrinsically tied to consumer electronics manufacturing. However, personalized design is still not an essential part of manufacturing for gaming. This presented an opportunity to the Formify team to bring unique, custom products to an industry sorely in need of such hardware innovation.
“By comparison, in every other athletic industry, you have different sizes of pads and shoes,” says Will. “It’s ridiculous that they’re using a one-size-fits-all mouse for esports. If you tried to play a game on a million dollar stage, which a lot of people are doing now, it just doesn’t make sense for everyone to use the same mouse.”
Formify’s idea to address this challenge was to develop a software platform that would transform a photo of a hand into a form-fitting mouse design. The next step would be to use 3D printing to produce the mouse itself, as other manufacturing processes generally used for electrics, such as injection molding, are better suited for higher volumes of identical parts from both cost and design standpoints.
“We set out to build a software that could build custom-shaped items with very minimal user input with no increased cost, due to the nature of 3D printing,” says Will.
Printing custom products
Once Formify had created the full tech stack required to turn a photo of a hand into a perfectly fitting form, the company set out to choose the optimal manufacturing technology. The physical product needed to be biocompatible, comfortable and incredibly lightweight for peak gaming performance.
After testing nearly every type of 3D printing technology available, Formify settled on Multi Jet Fusion (MJF). “Thousands of points on the mesh [product surface] had to be unique,” says Will. “MJF was the only technology that could achieve the fully-customizable shapes we were looking for.”
Will and the team discovered Protolabs Network during this prototyping and manufacturing research process. Formify quickly realized that the automated, instant quote builder and 3D printing capabilities matched what Formify was aiming to achieve, especially in contrast to the longer lead times and unfavorable pricing from more traditional manufacturers.
“It’s hard to get a fast quote and to get reasonable prices for one-off parts. The network is the obvious solution to getting a ton of custom one-off parts in a short turnover time,” says Will. Working with our platform helped the Formify team develop the product faster and find the optimal 3D printing technology along the way, and what really set us apart from traditional manufacturers was the platform’s robust automation.
“We make a custom product where each part is unique, so it’s really important for the process to be automated,” says Will. “If we’re uploading 200 different parts and we need to order them all at once, it’s a bit of a management hassle to organize that with a manufacturer if the process isn’t automated.”

Formify used the network throughout its prototyping process, as well as to produce 15 MJF-printed beta products sent to professional gamers and known names on Youtube and Twitch. The company is gearing up for a Kickstarter launch in Q2 of 2022, with the hope of scaling up to offer personalized mice to casual and professional gamers, offices looking for ergonomic peripherals (with brands etched in if desired, thanks to MJF’s surface finish options) and many other types of clients.
To match this desired demand, Formify plans to continue partnering with us to produce larger volumes of completely unique components for each personalized mouse. Our platform's robust automation, coupled with MJF’s unique capacity for mass customization, will support Will and the team as they scale. According to Will, “we have an unlimited manufacturing scope with the network.”
Multi Jet Fusion (MJF) - the next big innovation in gaming
3D printing with MJF has been an essential part of Formify’s story. The manufacturing technology produces superior surface finishes than other 3D printing processes as well as injection molding and allows for larger batches of one-off parts, which is key to making personalization far more accessible.
MJF also allows for far more complex geometries, which has helped Formify develop one of the most lightweight mice on the market. This is key to the product’s success in professional gaming, where split seconds matter more than you’d expect.
According to Will, “there have been a lot of gaming studies that say that the lighter your mouse is, the better your mouse is. A lightweight mouse increases target acquisition time and improves performance. People really want that extra edge in performance as gaming becomes more competitive.”

Designing a personalized future
Presently, Formify is preparing for its upcoming Kickstarter campaign, getting the custom mouse into the hands of more Youtubers and Twitch streamers in the meantime. The hope is to rapidly scale production with the network and start sending personalized peripherals to users within the gaming community and across many other industries.
For Will and the Formify team, however, perfecting custom mouse production is only the first step. Formify aspires to create other types of personalized products, such as virtual reality headsets, and venture further into office ergonomics and medical athletics.
“So many industries can benefit from personalized design,” says Will. “Personalized design should be accessible for everyone.”
Ready to produce your parts with Hubs?