Bioinspired materials have the potential to revolutionize manufacturing. Designed to copy properties, structures or processes found in nature, bioinspired materials are often strong and lightweight at the same time, as well as efficient in the use of resources, and can find many applications in technological and industrial design.
Of course, this is nothing new – humans have long looked to nature for ideas on how to make things, from kitchen sponges and honeycomb structures all the way to aviation. But recent advances in science and manufacturing have opened up a wealth of new opportunities. Researchers and designers from a wide range of fields, including medicine, structural engineering, soft robotics, materials science, apparel and architecture, use biomimicry, biomimetics and bioinspiration to come up with innovations that can be used across many different industries.
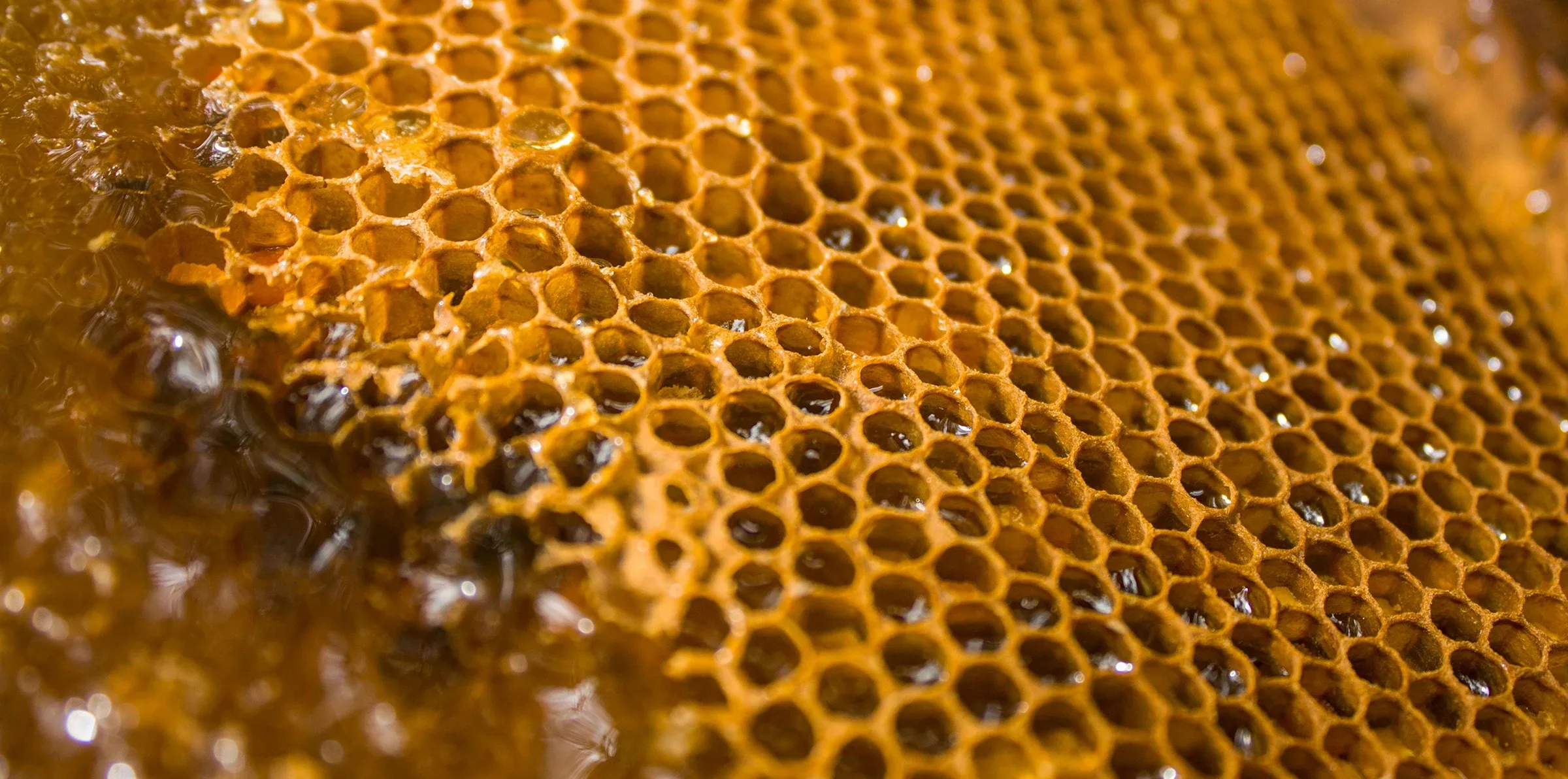
Copycat or innovator?
There are varying concepts: biomimicry simply imitates a natural function with a synthetic material. Take Velcro, which mimics the structure of burrs. Biomimetics is an interdisciplinary approach aiming to transfer insights from biology to technical application. And bioinspiration means taking natural processes as inspiration for the creation of new materials and functions.
Think about it: natural evolution equals hundreds of millions of years of R&D. We’d be fools not to take advantage of it. Indeed, it’s been predicted that by 2030, bioinspiration will generate $1.6 trillion of global GDP, while saving another $500 billion via resource and pollution mitigation.
Bioinspiration in medicine
Medicine and medical technology are obvious fields for applying bioinspired materials and processes. After all, the human body requires materials as close to its own as possible. Biomimetic ceramics, for example, mimic the structure of materials such as bone and teeth and can be used to create implants and bone replacements. And biomimetic hydrogels, which copy the structure of cartilage, can be applied in regenerative medicine.
Another fascinating substance is a surgical glue inspired by slugs. Or rather, by the process some slugs use to defend themselves against danger. Adding a certain protein to their mucus produces a sticky glue, protecting them from being detached from plant leaves and other surfaces by predators (or angry gardeners). Similarly, the new medical adhesive is made out of two types of polymers that become an ultra-strong glue when combined. Surgical glue, used for wound healing, needs to be especially powerful when used on moving body parts – think of beating hearts, for example – and the ‘slug glue’ is three times stronger than current surgical glue.
The animal world has inspired another sticky innovation, too: MIT researchers have developed an adhesive bandage that works similarly to the feet of geckos. Gecko-inspired adhesives are also being applied in other fields, including robotics.
Researchers and manufacturers are also looking to the natural world to learn about mechanical processes for medical technology. There are movable needles modelled on how parasitic wasps lay eggs inside caterpillars; suckers inspired by octopus tentacles that can pick up and release delicate tissue grafts for transplants; and catheters that can find their way through blood vessels using a navigation method similar to that of electric fish.
Spiders and other fashionable animals – bioinspired textiles
One of nature’s most intriguing materials is spider silk. Famously stronger than steel, yet lightweight and luxurious, it’s an appealing material for the apparel industry. While garments made from real spider silk will likely always remain in the realm of the extraordinary – beyond even haute couture – there have been various projects experimenting with synthetic spider silk and related processes. And recent breakthroughs are bringing us ever-closer to the goal of sustainably producing synthetic, or recombinant, spider silk at scale.
Recombinant silk is one of many new biofabricated materials: a field where the fashion and apparel industries are fully embracing bioinspiration. These materials are crafted by living microorganisms such as bacteria or mycelium, networks of fungal threads. Biofabricated materials are heavily researched as they offer a sustainable alternative to textiles based on petrochemicals. Examples include strong, lightweight and low-carbon nanocellulose, leather alternatives from mycelium, and dyes produced by bacteria.
Alternatives to microplastics
Various industries, including cosmetics and agriculture, rely on microplastics for various functions, and the search for alternatives has led researchers to silk fibroin, a natural polymer. It is highly adaptable as well as biodegradable and can be used in a range of applications, where it can mimic or even surpass the functionalities of microplastics.
PHA is a family of biopolyesters that shows a lot of promise as a plastic substitute. Produced by bacteria, PHA materials can be made from renewable resources and can biodegrade in many environments – including the ocean. As pellets, they can be used in injection molding and additive manufacturing, as well as a number of other plastic substitute applications.
Robotics: the ultimate bioinspiration
One could argue that the entire field of robotics is one of bioinspiration, and consequently, researchers continue to get new ideas from the natural world. Among the many new advances is a gripper inspired by a chameleon tongue and the way it encloses its prey.
Soft robotics is one of the fields where bioinspiration plays a big role. Using soft structures in robotics can assure greater safety in human interaction. And there is huge potential in creating morphologically adaptive materials – see also: 4D printing – and materials that can be endowed with sensing, dynamic response, and mobility faculties.
One example for direct bioinspiration are designs for robots engaged in deep-sea exploration, which need to be able to withstand extreme pressure. To remove the need for rigid protective casings, engineers have looked towards the pressure-adaptive forms of deep-sea species. Marine exploration is also assisted by jellyfish-inspired robots made from soft silicone and self-coiled polymer muscles.
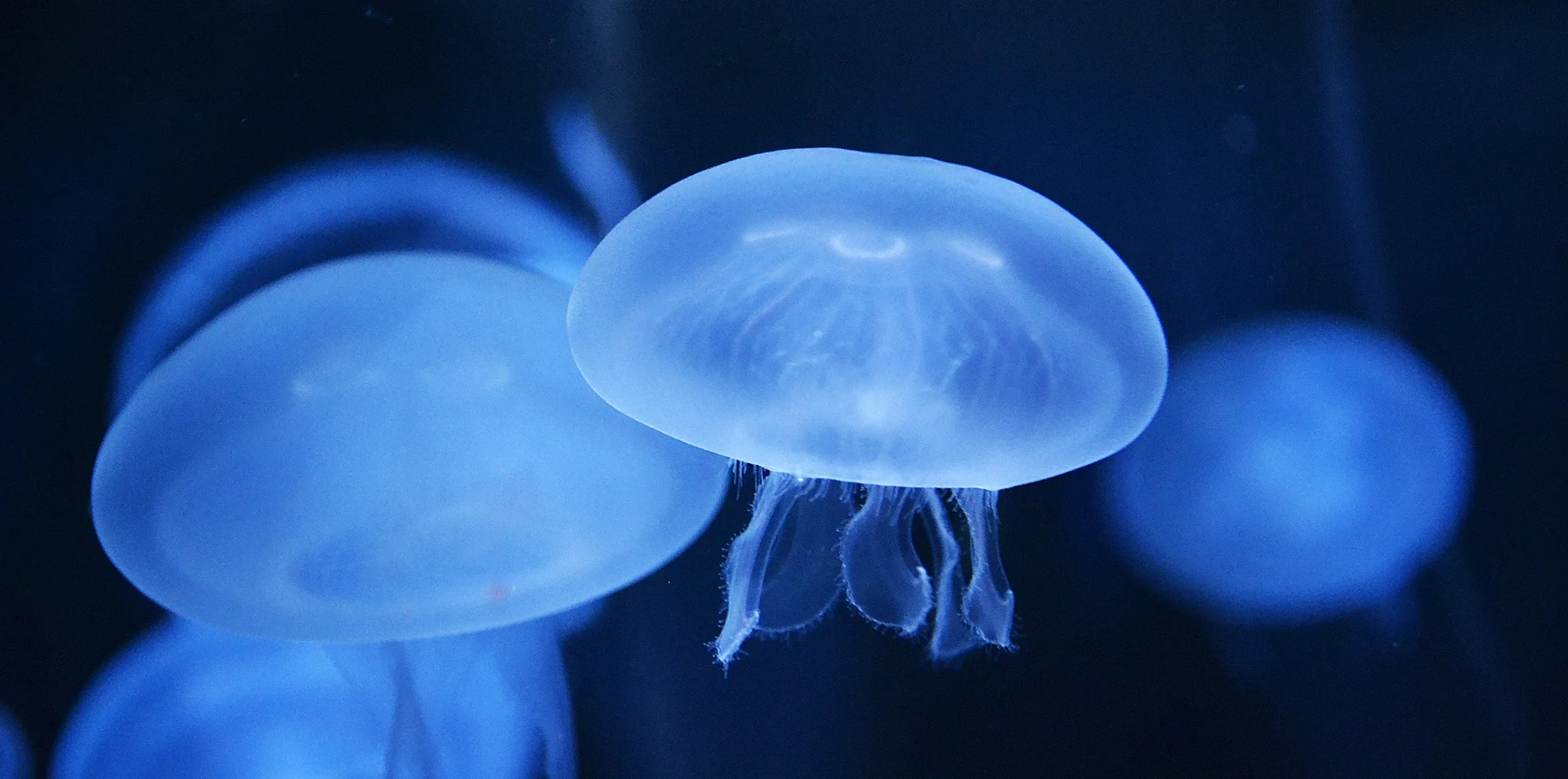
Bioinspired architecture: more than just green façades
In architecture, it’s flora rather than fauna that offers the most interesting opportunities for innovation. After all, plants are immobile – just like buildings – and have had to evolve to defend themselves against a variety of climatic conditions. Designers and engineers can choose from different ecosystems to find inspiration for solving a variety of challenges: from desert plants for UV protection to rainforest fauna, which offers plenty of mechanisms for issues such as water runoff and passive façade-shading. The ultimate aim: responsive biomaterials that can regulate humidity, temperature, CO2 and light, that can filter a variety of pollutants, and that have self-cleaning and self-repairing properties.
Maximum efficiency, minimum waste
The beauty of how natural materials and structures are constructed lies in their efficiency. Through highly evolved and elegant design, the best possible performance is achieved with a minimum of materials. In addition to biodegradability, this minimization of resources is why there is such a strong sustainability argument for many bioinspired materials and construction processes. And in order to achieve this efficiency, nature uses additive manufacturing methods.
Conversely, 3D printing techniques are capable of manufacturing nature-inspired structures that are too complex for traditional manufacturing methods. And so, in bioinspired manufacturing, hundreds of millions of years of evolution meet the newest technological innovations.
So, will spider silk and jellyfish silicone surpass traditional manufacturing materials? Perhaps the better question is, what can we learn from them to develop innovative new materials with superior properties? We’re excited to let the natural world guide us towards more adaptive, sustainably produced products with improved functionality, now and in the future.