Der vollständige technische Leitfaden
Spritzguss

Wollen Sie Ihre Teile spritzgießen lassen?
Design hochladen & Sofortangebot erhalten
Dieser Leitfaden liefert Ihnen alles Wissenswerte über das Spritzgießen. Erfahren Sie mehr über die Grundprinzipen dieses Verfahrens und erhalten Sie schnell umsetzbare Designtipps, die Zeit sparen und Ihre Kosten senken.
Part 1
Spritzgießen: Die Grundlagen
Was ist ein Spritzguss? Wie funktioniert er? Wofür wird er benutzt?
In diesem Abschnitt beantworten wir diese Fragen und zeigen Ihnen gängige Beispiele für Spritzgussteile, um Sie mit den grundlegenden Mechanismen und Anwendungen der Technologie vertraut zu machen.
Was bedeutet Spritzgießen?
Das Spritzgießen ist eine formgebende Fertigungstechnologie: Um ein Teil herzustellen, wird Kunststoff zuerst geschmolzen und dann in den Hohlraum eines Formwerkzeugs eingespritzt. Wenn sich das Material abkühlt, verfestigt es sich und nimmt die Geometrie (Form) des Formwerkzeugs an. Das Teil wird dann ausgeworfen und der Prozess beginnt von neuem.
Dies ist eine grundlegend andere Art der Herstellung als beim additiven Fertigungstechnologien (3D-Druck) oder subtraktiven Fertigungstechnologien (CNC-Bearbeitung). Das Fließen und Erstarren des Materials während des Spritzgießens hat einen erheblichen Einfluss auf die wichtigsten Designeinschränkungen für diese Technologie - mehr dazu unten.
Der Spritzguss-Prozess
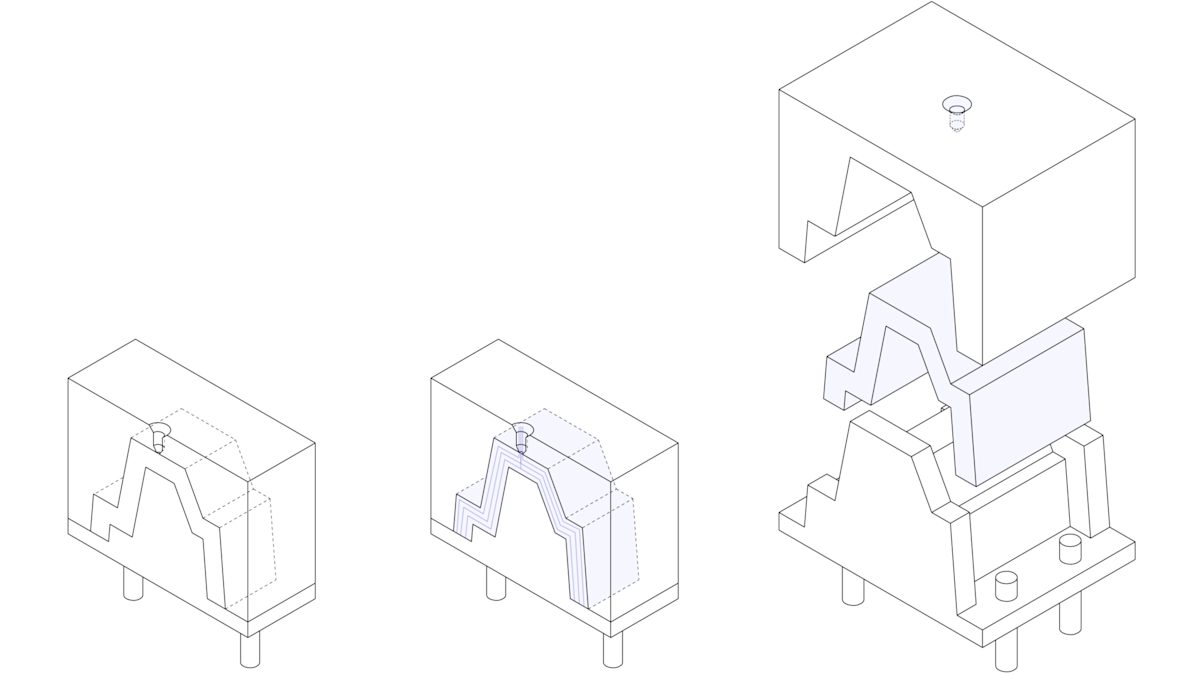
Der Kunststoff Spritzguss wird heute häufig sowohl für Verbraucherprodukte als auch für technische Anwendungen eingesetzt. Nahezu jeder Kunststoffgegenstand in Ihrer Umgebung wurde im Spritzgussverfahren hergestellt. Dies ist auf die Fähigkeit der Technologie zurückzuführen, identische Teile mit sehr hohen Stückzahlen (normalerweise 1.000 bis über 100.000 Stück) zu sehr niedrigen Kosten pro Teil (normalerweise 1-5 US-Dollar pro Stück) herzustellen.
Im Vergleich zu anderen Technologien sind die Anlaufkosten des Spritzgießens jedoch relativ hoch, hauptsächlich aufgrund des Bedarfs an kundenspezifischen Werkzeugen. Eine einzige Form kann je nach Komplexität, Material (Aluminium oder Stahl) und Genauigkeit (Prototyp, Kleinserien- oder Großserienform) zwischen 3.000 bis über 100.000 USD kosten.
Alle thermoplastischen Materialien können spritzgegossen werden. Einige Arten von Silikon und anderen duroplastischen Harzen sind ebenfalls für das Spritzgussverfahren geeignet. Die am häufigsten verwendeten Materialien beim Spritzgießen sind:
- Polypropylen (PP): ~38% der weltweiten Produktion
- ABS: ~27% der weltweiten Produktion
- Polyethylen (PE): ~15% der weltweiten Produktion
- Polystyrol (PS): ~8% der weltweiten Produktion
Selbst wenn wir alle anderen möglichen Herstellungstechnologien berücksichtigen, macht das Spritzgießen mit diesen vier Materialien allein mehr als 40% aller Kunststoffteile aus, die jedes Jahr weltweit hergestellt werden!
Eine kurze Geschichte des Spritzgießens
Kunststoffe ersetzen Elfenbein
1869 erfand John Wesley Hyatt Celluloid, den ersten praktisch einsetzbaren Kunststoff, der Elfenbein für die Herstellung von … Billardkugeln ersetzen sollte! Frühe Spritzgießmaschinen verwendeten einen Zylinder, um den Kunststoff zu erwärmen, und einen Kolben, um ihn in die Form zu spritzen.
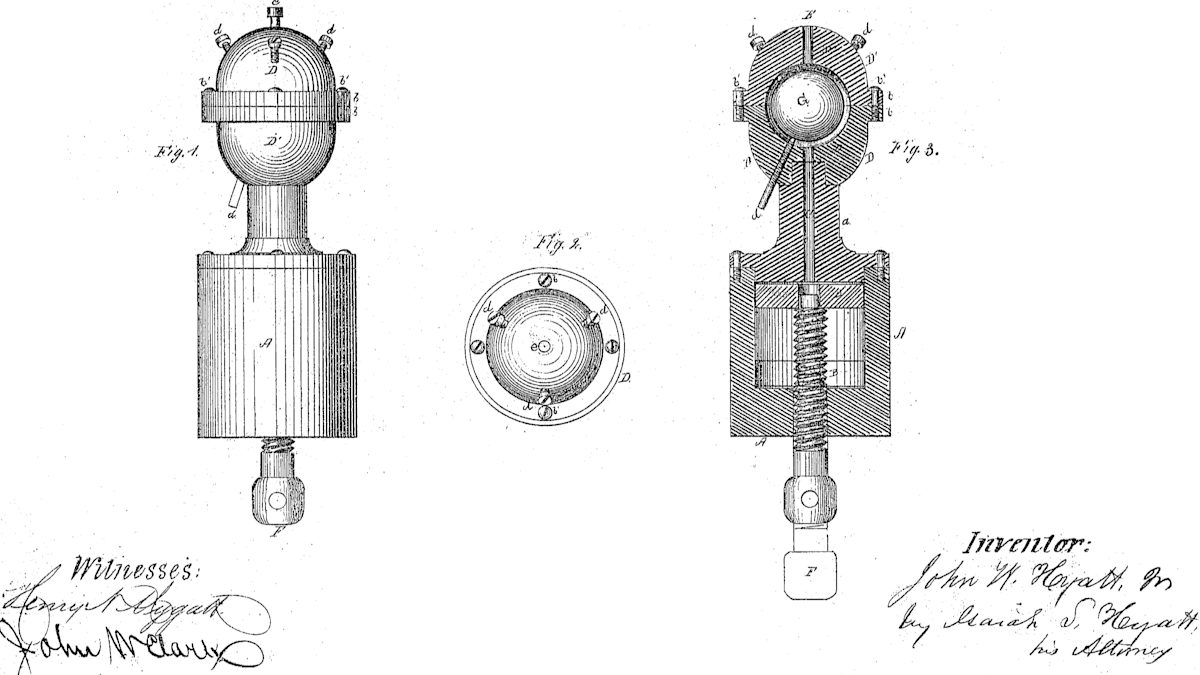
Die revolutionäre Erfindung
Mitte der 1950er Jahre revolutionierte die Erfindung der Kolbenschraube im Alleingang die Kunststoffindustrie. Die Kolbenschraube löste wichtige Probleme mit ungleichmäßiger Erwärmung des Kunststoffs, mit dem frühere Systeme konfrontiert waren, und eröffnete neue Horizonte für die Massenproduktion von Kunststoffteilen.

Spritzgießen heute
Heute ist Spritzgießen ein [Markt mit 300 Milliarden US-Dollar Umsatz] (https://www.grandviewresearch.com/industry-analysis/injection-molded-plastics-market „Injection Molding market“). Weltweit werden jährlich mehr als 5 Millionen Tonnen Kunststoffteile im Spritzgussverfahren hergestellt. In letzter Zeit steigt der Bedarf an biologisch abbaubaren Materialien aus Umweltgründen.

Spritzgießmaschine: Wie funktionieren sie?
Eine Spritzgießmaschine besteht aus drei Hauptteilen: der Spritzeinheit, der Form - dem Herzstück des gesamten Prozesses - und der Spann-/Auswerfeinheit.
In diesem Abschnitt untersuchen wir den Zweck jedes dieser Systeme und wie sich deren grundlegende Funktionsmechanik auf das Endergebnis des Spritzgussprozesses auswirkt.
Sehen Sie sich eine große Spritzgießmaschine in Aktion an, während Sie im folgenden Video alle 3 Sekunden 72 Flaschenverschlüsse herstellt.
Die Spritzeinheit

Die Spritzeinheit dient dazu, den Rohkunststoff aufzuschmelzen und in die Form zu befördern. Sie besteht aus dem Trichter, dem Zylinder und der Kolbenschnecke.
Der Rohkunststoff kommt in Form von Pellets an. Im Trichter können die Pellets mit Pigmenten oder anderen Zusätzen (z. B. Glasfasern) gemischt werden. Auf diese Weise können Farbe und physikalische Eigenschaften der Formteile auf die spezifischen Anforderungen der jeweiligen Anwendung zugeschnitten werden.
Als Nächstes wird das Material in den Zylinder geleitet, in dem sich die Kolbenschnecke befindet.
Die Schnecke erfüllt zwei Aufgaben: Sie befördert die Pellets in Richtung der Form und komprimiert sie gleichzeitig. Tatsächlich erzeugen die durch die Bewegung der Schnecke verursachten Scherkräfte 60% bis 90% der zum Schmelzen der Kunststoffpellets erforderlichen Wärme. Der Rest wird durch die Heizbänder bereitgestellt, die um den Zylinder gewickelt sind.
Sobald sich genügend geschmolzenes Plastik vor der Schraube befindet, fährt der Kolben nach vorne und presst das Material in den leeren Hohlraum der Form (wie eine Spritze). Der gesamte Vorgang läuft kontinuierlich ab, sodass das Befüllen der Form nur wenige Sekunden dauert.
Herstellung der Spritzgussform
Die Form ist wie das Negativ eines Fotos: Ihre Geometrie und Oberflächenstruktur wird direkt auf das Spritzgussteil übertragen.
«br>
Die Form macht normalerweise den größten Teil der Anlaufkosten beim Spritzgießen aus: Die Kosten für eine typische Form beginnen bei etwa 2.000-5.000 $ für eine einfache Geometrie und relativ kleine Produktionsserien (1.000 bis 10.000 Einheiten) und können bis zu 100.000 $ für Formen, die für die Großproduktion optimiert sind (100.000 Einheiten oder mehr), steigen.
«br>
Dies ist auf das hohe Maß an Fachwissen zurückzuführen, das für die Konstruktion und Herstellung einer qualitativ hochwertigen Form erforderlich ist, mit der Tausende (oder Hunderttausende) von Teilen präzise hergestellt werden können.
«br>
Die Formen werden in der Regel aus Aluminium oder Werkzeugstahl CNC-gefräst und dann auf den erforderlichen Standard bearbeitet. Neben dem Negativ des Teils haben sie auch andere Merkmale, wie das Angusssystem, das den Materialfluss in die Form erleichtert, und interne Wasserkühlkanäle, die die Kühlung des Teils unterstützen und beschleunigen.
«br>
Lernen Sie mehr über die CNC-Bearbeitung. Lesen Sie den vollständigen Leitfaden zur CNC-Bearbeitung
«br>
Jüngste Fortschritte bei den Materialien für den 3D-Druck haben die Herstellung von Formen ermöglicht, die sich für den [Low-Run-Spritzguss] (https://www.hubs.com/knowledge-base/3d-printing-low-run-injection-molds/) (100 Teile oder weniger) zu einem Bruchteil der Kosten eignen. Solche kleinen Mengen waren in der Vergangenheit aufgrund der sehr hohen Kosten des traditionellen Formenbaus wirtschaftlich unrentabel.
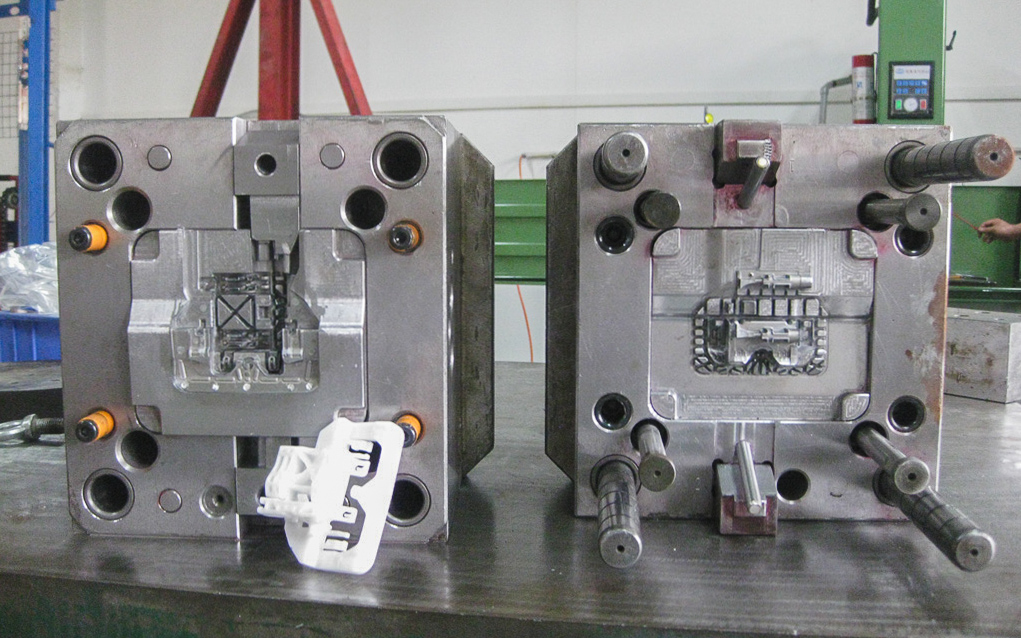
Die Anatomie der Form

Die einfachste Form- die Ziehform (Straight-Pull-Form) - besteht aus zwei Hälften: dem Hohlraum und dem Kern. Für komplexere Teile mit Hinterschneidungen können auch Seitenkerne verwendet werden, die in einem Winkel in das Teil hinein- und aus ihm herausgleiten. Weitere Informationen zu Seitenkernen und Hinterschneidungen finden Sie in einem nächsten Abschnitt.
Der Kern und der Hohlraum haben unterschiedliche Funktionen. Der Kern ist die Formhälfte, die näher am Einspritzsystem liegt. Er bildet die „kosmetische“ Seite des Teils (A-Seite), die ein gutes optisches Erscheinungsbild erfordert. Der Hohlraum ist die hintere Formhälfte und bildet die „verborgene“ Funktionsseite (B-Seite), die alle Strukturelemente des Teils (Rippen, Vorsprünge usw.) umfasst.
Die Formen werden normalerweise aus Aluminium (für 1.000 bis 5.000 Einheiten) oder Werkzeugstahl (für über 100.000 Einheiten) CNC-bearbeitet. Für Kleinserien (<100 Einheiten) können die Formen sogar 3D-gedruckt werden, um die Vorlaufzeiten zu verkürzen.
Neben dem „Negativ“ des Teils weist eine Form andere Merkmale auf, die den Spritzvorgang unterstützen. Beispielsweise enthalten Formen häufig Kühlkanäle, die den Erstarrungsprozess beschleunigen, und Entlüftungsöffnungen, die dabei helfen, die Luft aus der leeren Form zu entfernen.
Interessante Tatsache: Etwa 50% der Dauer eines typischen Spritzgusszyklus‘ entfallen auf das Abkühlen und Erstarren der Teile. Das Minimieren der Dicke eines Designs ist der Schlüssel, um diesen Schritt zu beschleunigen und Kosten zu senken.
Die 2 Seiten der Form: A-Seite & B-Seite
Spritzgussteile haben zwei Seiten: die A-Seite, die dem Hohlraum zugewandt ist (vordere Hälfte der Form) und die B-Seite, die dem Kern zugewandt ist (hintere Hälfte der Form). Diese beiden Seiten dienen in der Regel unterschiedlichen Zwecken:
«br>
- Die A-Seite hat in der Regel ein besseres visuelles Erscheinungsbild und wird oft als kosmetische Seite bezeichnet. Die Flächen auf der A-Seite sind glatt oder haben eine Textur nach Ihren Designvorgaben.
«br>
- Die B-Seite enthält normalerweise die verborgenen (aber sehr wichtigen) Strukturelemente des Teils (die Vorsprünge, Rippen, Schnappverbindungen usw.). Aus diesem Grund wird sie als Funktionsseite bezeichnet. Die B-Seite hat oft eine rauhere Oberfläche und sichtbare Spuren der Auswerferstifte.
Das Angusssystem
Der geschmolzene Kunststoff gelangt durch das Angusssystem in die Form. Das Angusssystem besteht normalerweise aus drei Hauptabschnitten: dem Anguss (dem Hauptkanal), den Läufern (den Führungskanälen) und dem Anschnitt (den Eintrittspunkten).
Verschiedene Arten von Anschnitten eignen sich für verschiedene Anwendungen. Die Abbildung zeigt einen * Kantenanschnitt*, während die Quader unten mit einem Heißanschnitt hergestellt wurden.
Das Angusssystem wird nach dem Auswerfen vom Teil abgeschnitten. Dies ist der einzige Materialabfall im Spritzguss, von dem 15-30% recycelt und wiederverwendet werden können.

Verschiedene Formenschleusen sind für unterschiedliche Anwendungen geeignet. Es gibt 4 Arten von Formenschleusen, die beim Spritzgießen verwendet werden:
- Randschleusen spritzen Material an der Trennfuge der beiden Werkzeughälften ein und sind der am häufigsten verwendete Anschnitttyp. Das Angusssystem muss später manuell entfernt werden, wobei eine kleine Fehlstelle an der Einspritzstelle verbleibt.
- Tunnelschleusen injizieren Material unterhalb der Trennlinie. Das Angusssystem schnappt ab, wenn das Teil aus dem Werkzeug ausgestoßen wird, so dass eine manuelle Entnahme nicht mehr erforderlich ist. Dies macht diesen Anschnitttyp ideal für sehr große Volumen.
- Hinterschleusen injizieren das Material von der Rückseite des Hohlraums und verbergen so die kleine Unvollkommenheit, die vom Brechen der anderen Schleusen übrig geblieben ist. Diese Anschnitte werden für Teile verwendet, die ein hervorragendes optisches Erscheinungsbild erfordern.
- Hot Tips spritzen Kunststoff von der Oberseite des Teils ein. Auf diese Weise wird kein Material auf dem Angusssystem verschwendet, was sie ideal für die Großserienproduktion macht, aber an der Einspritzstelle wird eine Vertiefung sichtbar.
Der Anguss
An dem Punkt, an dem das Läufersystem mit dem Teil verbunden ist, ist normalerweise eine kleine Unvollkommenheit sichtbar, die als Anguss bezeichnet wird.
Wenn das Vorhandensein des Angusses aus ästhetischen Gründen nicht erwünscht ist, kann er auch in der funktionalen B-Seite des Teils „verborgen“ sein.
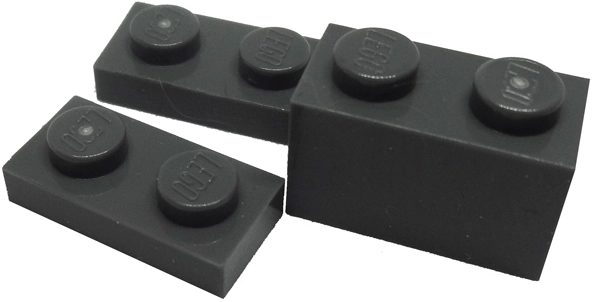
The clamping and ejection system
On the far side of an injection molding machine is the clamping system. The clamping system has a dual purpose: it keeps the 2 parts of the mold tightly shut during injection and it pushes the part out of the mold after it opens.
After the part is ejected, it falls onto a conveyor belt or a bucket for storage and the cycle starts over again.
Alignment of the different moving parts of the mold is never perfect though. This causes the creation of 2 common imperfections that are visible on almost every injection molded part:
-
Parting lines which are visible on the side of a part where the 2 halves of the mold meet. They are caused by tiny misalignments and the slightly rounded edges of the mold.
-
Ejector (or witness) marks which are visible on the hidden B-side of the part. They are created because the ejector pins are slightly protruding above or indented below the surface of the mold.
The image below shows the mold used to manufacture both sides of the casing for a remote controller. Quick quiz: try to locate the *core* (A-side), the *cavity* (B-side), the runner system, the ejector pins, the side-action core and the air vents on this mold.
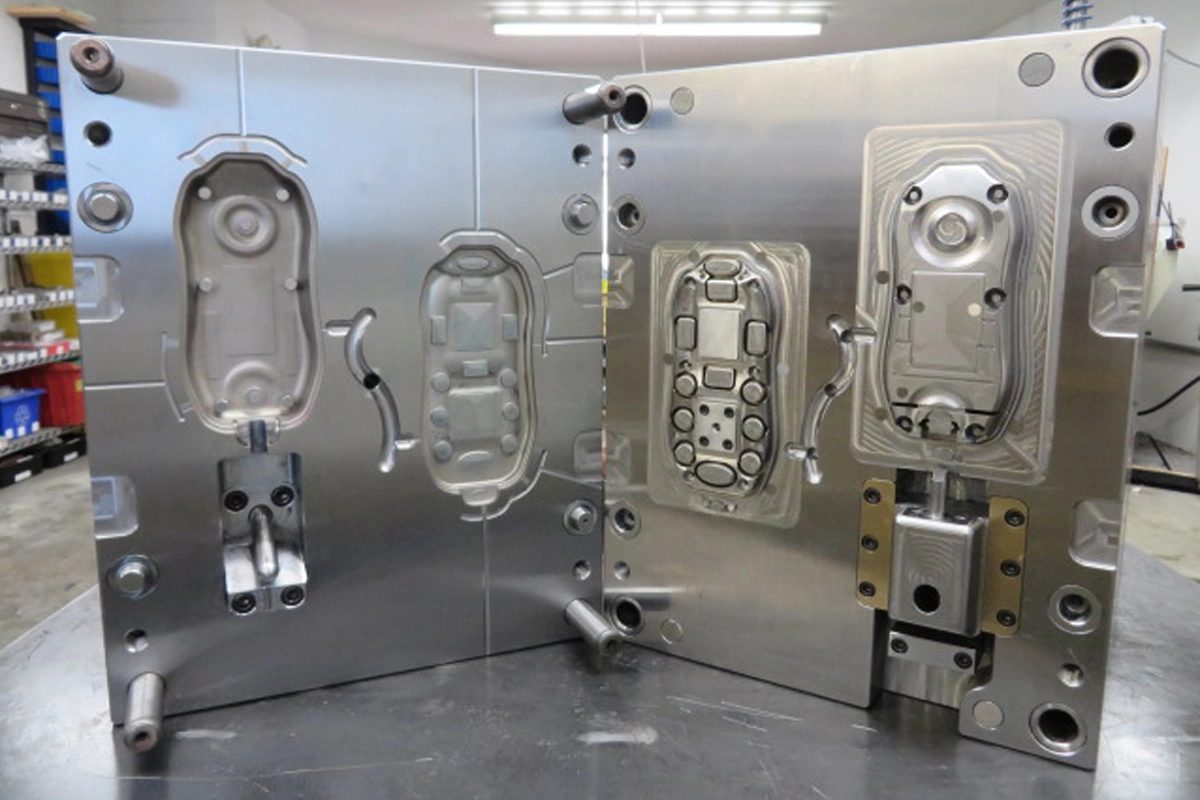
Vorteile und Einschränkungen des Spritzgießens
Das Spritzgießen ist eine etablierte Fertigungstechnologie mit einer langen Geschichte, die jedoch ständig weiterentwickelt und mit neuen technologischen Fortschritten verbessert wird.
Im Folgenden finden Sie eine kurze Übersicht über die wichtigsten Vor- und Nachteile des Spritzgießens, um zu verstehen, ob dies die richtige Lösung für Ihre Anwendung ist.
Vorteile des Spritzgießens
Spritzgießen ist die kostengünstigste Technologie zur Herstellung großer Mengen identischer Kunststoffteile. Sobald die Form erstellt und die Maschine eingerichtet ist, können zusätzliche Teile sehr schnell und zu sehr geringen Kosten hergestellt werden.
Das empfohlene Mindestproduktionsvolumen für das Spritzgießen beträgt 500 Stück. Ab diesem Zeitpunkt beginnen sich Skaleneffekte bemerkbar zu machen, und die relativ hohen Anfangskosten für Werkzeuge wirken sich weniger stark auf den Stückpreis aus.
Nahezu jedes thermoplastische Material (und einige Duroplaste und Silikone) können spritzgegossen werden. Dies gibt eine sehr breite Palette verfügbarer Materialien mit unterschiedlichen physikalischen Eigenschaften, mit denen gestaltet werden kann.
Spritzgussteile haben sehr gute physikalische Eigenschaften. Ihre Eigenschaften können durch Verwendung von Additiven (z. B. Glasfasern) oder durch Zumischen verschiedener Pellets (z. B. PC/ABS-Mischungen) angepasst werden, um das gewünschte Maß an Festigkeit, Steifheit oder Schlagzähigkeit zu erreichen.
Der typische Spritzgusszyklus dauert 15 bis 60 Sekunden, abhängig von der Größe des Teils und der Komplexität der Form. Im Vergleich dazu kann die CNC-Bearbeitung oder der 3D-Druck Minuten bis Stunden benötigen, um dieselbe Geometrie zu erzeugen. Eine einzelne Form kann auch mehrere Teile aufnehmen, wodurch die Produktionskapazitäten dieses Herstellungsprozesses weiter erhöht werden.
Dies bedeutet, dass hunderte (oder sogar tausende) identische Teile pro Stunde hergestellt werden können.
Der Spritzgussprozess ist sehr gut wiederholbar und die produzierten Teile sind im Wesentlichen identisch. Natürlich tritt im Laufe der Zeit ein gewisser Verschleiß an der Form auf, aber eine typische vorläufige Aluminiumform hat eine Lebensdauer von 5.000 bis 10.000 Zyklen, während Großserienformen aus Werkzeugstahl mehr als 100.000 Zyklen aushalten können.
Typischerweise werden beim Spritzgießen Teile mit Toleranzen von ± 0,500 mm hergestellt. Unter bestimmten Umständen sind auch engere Toleranzen bis zu ± 0,125 mm möglich. Diese Genauigkeit ist für die meisten Anwendungen ausreichend und mit der CNC-Bearbeitung und dem 3D-Druck vergleichbar.
Eine wesentliche Stärke des Spritzgießens besteht darin, dass fertige Produkte hergestellt werden können, die nur wenig oder gar keine zusätzliche Nachbearbeitung benötigen. Die Oberflächen der Form können sehr stark poliert werden, um spiegelähnliche Teile zu erzeugen. Oder sie können perlgestrahlt werden, um strukturierte Oberflächen zu erzeugen. Die SPI-Normen geben den Grad der Endbearbeitung vor, der erreicht werden kann.
[Empfehlungen zur Verarbeitung/Materialverträglichkeit einholen →] (https://www.hubs.com/knowledge-base/injection-molding-spi-surface-finishes “Injection molding SPI finish recomendations”)
Einschränkungen des Spritzgießens
Die wirtschaftliche Haupteinschränkung beim Spritzgießen sind die hohen Werkzeugkosten. Da für jede Geometrie eine eigene Form angefertigt werden muss, sind die Anlaufkosten sehr hoch. Diese beziehen sich hauptsächlich auf das Design und die Herstellung der Form und variieren typischerweise zwischen 5.000 und 100.000 USD. Aus diesem Grund ist das Spritzgießen nur für Produktionen über 500 Stück wirtschaftlich.
Nach der Herstellung einer Form ist deren Modifizierung sehr teuer: Konstruktionsänderungen erfordern in der Regel die Herstellung einer neuen Form von Grund auf. Aus diesem Grund ist es sehr wichtig, ein Teil für das Spritzgießen richtig zu konstruieren.
In Teil 2 listen wir die wichtigsten Designaspekte auf, die Sie beim Entwurf für das Spritzgießen berücksichtigen müssen. Mit Teil 5 erfahren Sie auch, wie Sie das Risiko verringern können, indem Sie physische Prototypen Ihrer Teile erstellen.
Die typische Bearbeitungszeit für das Spritzgießen variiert zwischen 6 und 10 Wochen - 4 bis 6 Wochen für die Herstellung der Form, plus 2 bis 4 Wochen für die Produktion und den Versand. Wenn Konstruktionsänderungen am Modell erforderlich sind, was durchaus üblich ist, erhöht sich die Bearbeitungszeit entsprechend.
Im Vergleich dazu können Teile, die in einem Desktop-3D-Drucker hergestellt wurden, über Nacht ausgeliefert werden, während industrielle 3D-Drucksysteme eine typische Vorlaufzeit von 3 bis 5 Tagen haben. CNC-gefräste Teile werden in der Regel innerhalb von 10 Tagen oder sogar innerhalb von 5 Tagen geliefert.
Beispiele für Spritzgussprodukte
Wenn Sie sich in diesem Moment umschauen, sehen Sie mindestens einige Produkte, die im Spritzgussverfahren hergestellt wurden. Wahrscheinlich sehen Sie sich gerade eines an: das Gehäuse des Geräts, mit dem Sie diesen Führer lesen.
Um sie zu erkennen, achten Sie auf diese drei Punkte: eine Trennlinie, Auswurfspuren auf der verborgenen Seite und eine relativ gleichmäßige Wandstärke im gesamten Teil.
Wir haben hier einige Beispiele gebräuchlicher Spritzgussprodukte zusammengestellt, um ein besseres Verständnis dafür zu erhalten, was mit diesem Herstellungsverfahren erreicht werden kann.
Legosteine
Legosteine sind eines der bekanntesten Beispiele für Spritzgussteile. Sie werden mit Formen wie der abgebildeten hergestellt, die 120 Millionen Legosteine (das sind 15 Millionen Zyklen) produzierte, bevor sie außer Betrieb genommen wurde.
Das für Legosteine verwendete Material ist ABS aufgrund seiner hohen Schlagfestigkeit und ausgezeichneten Formbarkeit. Jeder einzelne Stein wurde perfekt konstruiert, um Toleranzen von bis zu 10 Mikrometern (oder einem Zehntel menschlicher Haare) zu erreichen. Dies wird teilweise durch die Verwendung der besten Entwurfspraktiken erreicht, die wir im nächsten Abschnitt untersuchen werden (einheitliche Wandstärke, Entwurfswinkel, Rippen, geprägter Text usw.).

Flaschenverschlüsse
Viele Kunststoffverpackungen werden im Spritzgussverfahren hergestellt. Tatsächlich ist das Verpackungswesen der größte Markt für den Spritzguss.
Beispielsweise werden Flaschenverschlüsse aus Polypropylen spritzgegossen. Polypropylen (PP) hat eine hervorragende chemische Beständigkeit und ist für den Kontakt mit Lebensmitteln geeignet.
Auf Flaschenverschlüssen können Sie auch alle gängigen Spritzgussfehler (Trennlinie, Auswurfspuren usw.) und die gängigen Konstruktionsmerkmale (Rippen, Freistreifen usw.) erkennen.
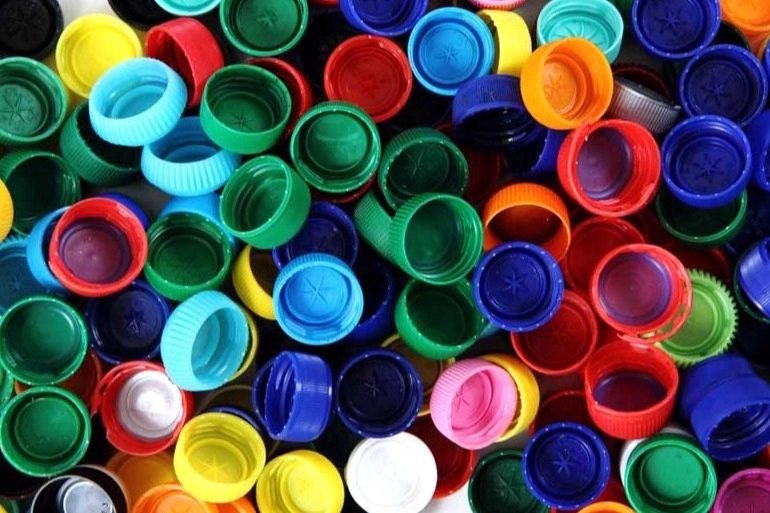
Modellflugzeuge
Modellflugzeuge sind ein weiteres bekanntes Beispiel für Spritzgussteile. Das hier verwendete Material ist hauptsächlich Polystyrol (PS), da es kostengünstig und leicht zu formen ist.
Interessant an Modellflugzeug-Bausätzen ist, dass das Angusssystem noch angebracht ist. So können Sie den Weg sehen, den der geschmolzene Kunststoff zurückgelegt hat, um die leere Form zu füllen.
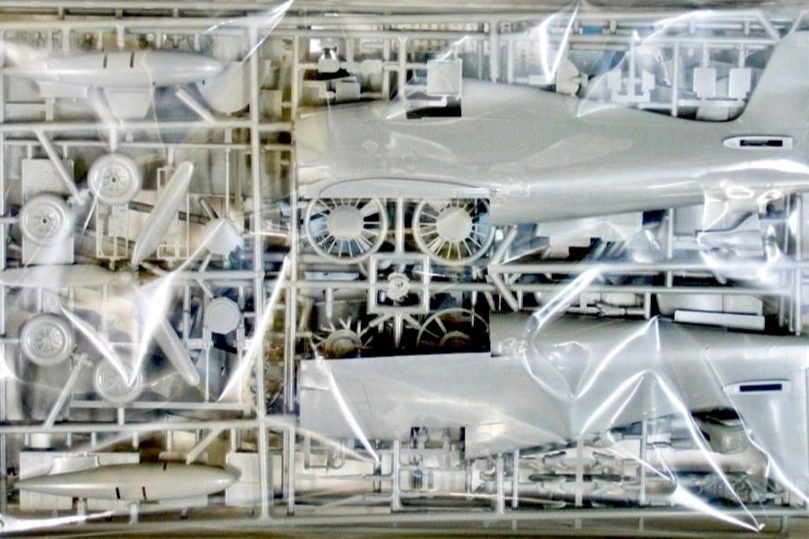
Autoteile
Nahezu jedes Kunststoffbauteil im Innenraum eines Autos wurde spritzgegossen. Die drei in der Automobilindustrie am häufigsten verwendeten Spritzgussmaterialien sind Polypropylen (PP) für unkritische Teile, PVC für seine gute Witterungsbeständigkeit und ABS für seine hohe Schlagzähigkeit.
Mehr als die Hälfte der Kunststoffteile eines Autos besteht aus einem dieser Materialien, einschließlich der Stoßstangen, der inneren Karosserieteile und der Armaturenbretter.

Unterhaltungselektronik
Die Gehäuse fast aller in Serie hergestellten Unterhaltungselektronikgeräte werden spritzgegossen. Hier werden ABS und Polystyrol (HDPE) wegen ihrer hervorragenden Schlagzähigkeit und guten elektrischen Isolation bevorzugt.

Medizinische Geräte
Viele sterilisierbare und biokompatible Materialien sind für das Spritzgießen verfügbar.
Medizinisches Silikon ist eines der beliebtesten Materialien in der Medizinbranche. Da Silikon ein Duroplast ist, sind spezielle Maschinen und Prozesskontrollen erforderlich, was die Kosten erhöht.
Für Anwendungen mit weniger strengen Anforderungen sind andere Materialien wie ABS, Polypropylen (PP) und Polyethylen (PE) üblicher.
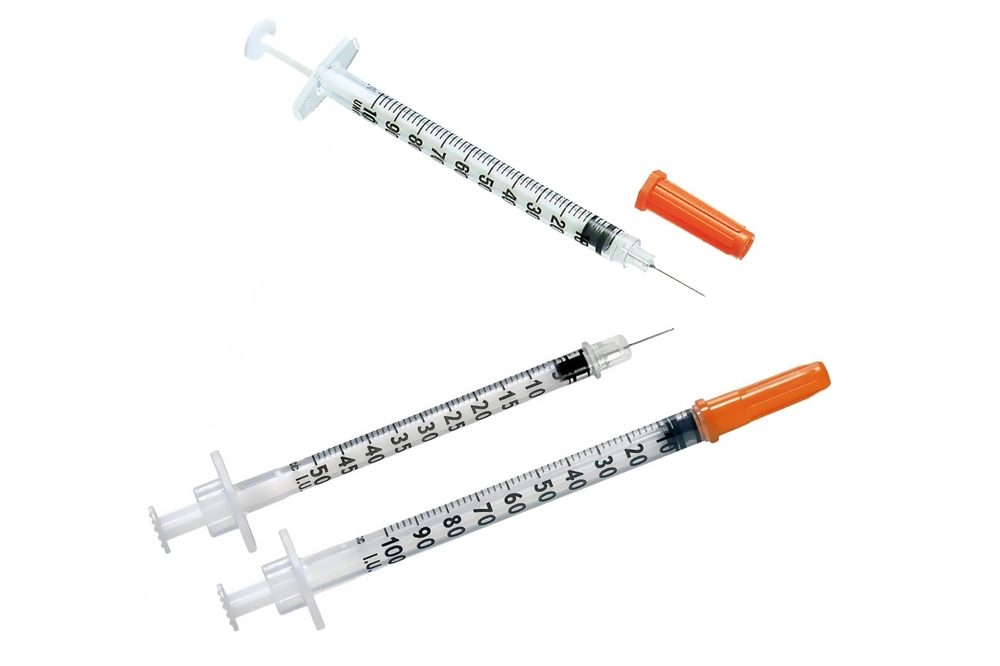
Part 2
Design für den Spritzguss
In diesem Abschnitt erfahren Sie, wie Sie Ihre Konstruktionen für das Spritzgießen optimieren können.
Verwenden Sie die folgenden Leitlinien, um Zeit zu sparen und Ausfälle zu reduzieren, und lernen Sie, wie Sie Merkmale erstellen, die die Funktionalität Ihrer Designs maximieren.
Häufige Spritzgussdefekte
Die meisten Defekte beim Spritzgießen hängen entweder mit dem Fließen des geschmolzenen Materials oder seiner ungleichmäßigen Abkühlgeschwindigkeit während des Erstarrens zusammen.
Hier ist eine Liste von Fehlern, die ein Ingenieur beim Entwerfen eines Teils für das Spritzgießen berücksichtigen sollte. Im nächsten Abschnitt erfahren Sie, wie Sie diese vermeiden können, indem Sie die bewährten Entwurfspraktiken befolgen.
Verziehen
Wenn bestimmte Abschnitte schneller abkühlen (und dadurch schrumpfen) als andere, kann sich das Teil aufgrund innerer Spannungen dauerhaft verziehen.
Teile mit nicht konstanter Wandstärke neigen am stärksten zum Verziehen.

Sinkstellen
Wenn sich das Innere eines Teils vor seiner Oberfläche verfestigt, kann eine kleine Vertiefung in einer ansonsten ebenen Oberfläche auftreten, die als Sinkstelle bezeichnet wird.
Teile mit dicken Wänden oder schlecht geformten Rippen neigen am ehesten zu Sinkstellen.

Ziehspuren
Wenn der Kunststoff schrumpft, übt er Druck auf die Form aus. Während des Auswurfs gleiten und kratzen die Wände des Teils gegen die Form, was zu Abriebspuren führen kann.
Teile mit senkrechten Wänden (und ohne Verzugswinkel) sind am anfälligsten für Spuren.

Grenzlinien
Wenn sich zwei Materialflüsse treffen, können sich kleine haarartige Verfärbungen entwickeln. Diese Grenzlinien wirken sich einerseits auf die Ästhetik der Teile aus, verringern jedoch im Allgemeinen auch die Festigkeit des Teils.
Teile mit abrupten Geometrieänderungen oder Löchern neigen eher zu Grenzlinien.

Kurzteile
In der Form eingeschlossene Luft kann den Materialfluss während des Einspritzens behindern, was zu einem unvollständigen Teil führt. Gutes Design kann die Fließfähigkeit des geschmolzenen Kunststoffs verbessern.
Teile mit sehr dünnen Wänden oder schlecht geformten Rippen neigen eher zu verkürzten Teilen.

Umgang mit Hinterschneidungen
Ein wichtiger Aspekt beim Entwerfen von Teilen für das Spritzgießen sind Hinterschneidungen.
Hinterschneidungen beim Spritzgießen sind Teilemerkmale, die mit einer einfachen zweiteiligen Form nicht hergestellt werden können, da beim Öffnen der Form oder beim Auswerfen Material im Weg wäre.
Die Zähne eines Gewindes oder der Haken einer Schnappverbindung sind Beispiele für Hinterschneidungen. Im Folgenden finden Sie einige einfache Lösungen für den Umgang mit Hinterschneidungen:
Absperrungen verwenden
Eine andere Möglichkeit, mit Hinterschneidungen umzugehen, besteht darin, Material unter oder über dem Problembereich zu entfernen. Auf diese Weise wird die Hinterschneidung beseitigt, da das gesamte Teil direkt von der Form getragen werden kann.
Absperrungen sind ein nützlicher Trick, um mit Hinterschneidungen an Innenbereichen des Teils (für Schnappverbindungen) oder an den Seiten des Teils (für Löcher oder Griffe) umzugehen.

Im Folgenden sind einige Beispiele dafür aufgeführt, wie Spritzgussteile so umgestaltet werden können, dass Hinterschneidungen vermieden werden: Im Wesentlichen wird im Bereich unter der Hinterschneidung Material entfernt, wodurch das Problem vollständig beseitigt wird.
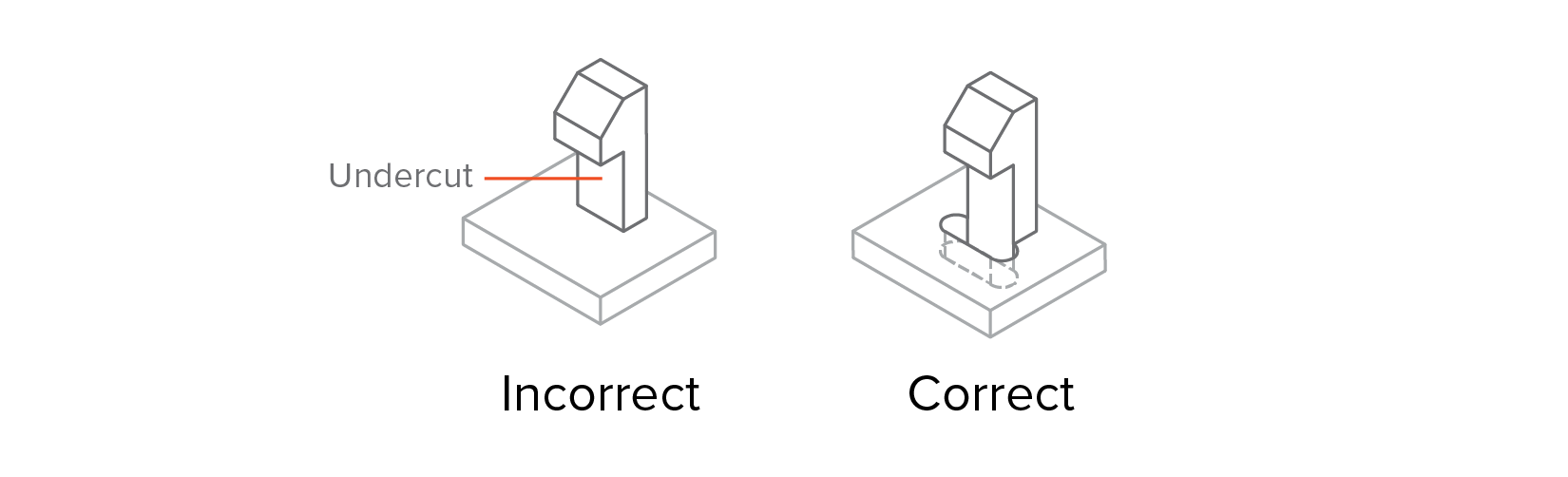
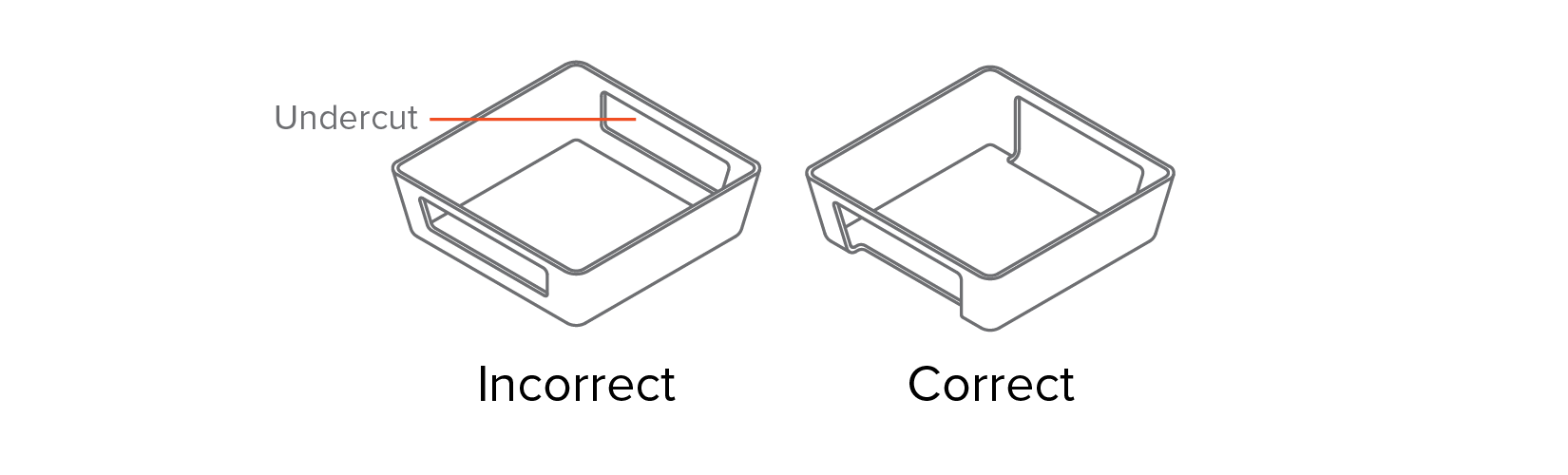
Trennlinie verschieben
Die einfachste Möglichkeit, mit einer Hinterschneidung umzugehen, besteht darin, die Trennlinie der Form so zu verschieben, dass sie diese schneidet.
Diese Lösung eignet sich für viele Designs mit Hinterschneidungen auf einer Außenfläche. Vergessen Sie nicht, die Verzugswinkel entsprechend anzupassen.

Hinterschneidungen entfernen
Wenn das Teil flexibel genug ist, kann es beim Auswerfen über die Form verformt werden. Das Abstreifen von Hinterschneidungen wird für interne Merkmale wie das Gewinde von Flaschenverschlüssen verwendet.
Verwenden Sie diese Leitlinien, um Hinterschneidungen für das Abstreifen zu entwerfen:
● Wählen Sie ein flexibles Material - wie PP, PE oder Nylon (PA)
● Die Höhe der Hinterschneidung sollte 5% des Lochdurchmessers betragen
● Verwenden Sie einen Steigungswinkel von 30° bis 45°

Es wird empfohlen, das Abstreifen von Hinterschneidungen bei Teilen aus faserverstärktem Kunststoff zu vermeiden. Typischerweise können flexible Kunststoffe wie PP, HDPE oder Nylon (PA) Hinterschneidungen von bis zu 5% ihres Durchmessers tolerieren.
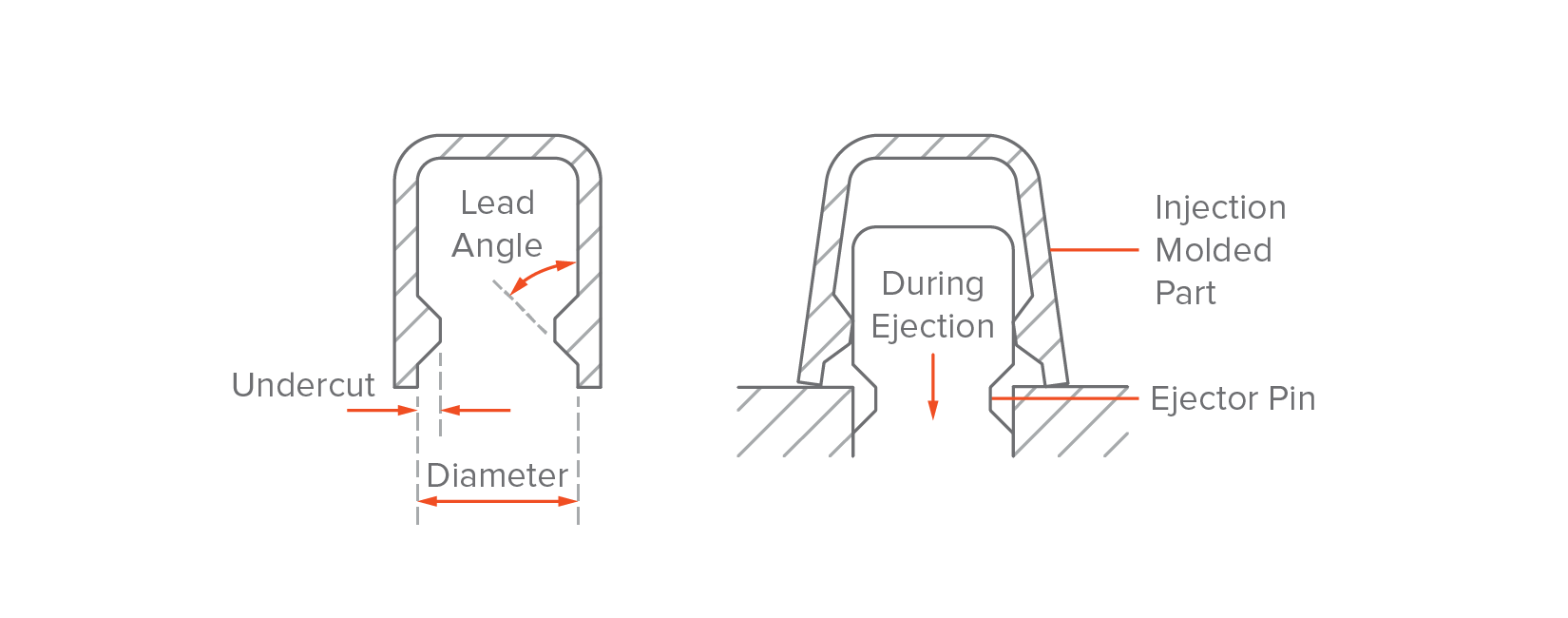
Seitenkerne
Wenn keine der oben genannten Lösungen durchführbar ist, können Kerne verwendet werden, die von der Seite aus dem Teil herausgleiten, bevor es ausgeworfen wird.
Seitenkerne sollten sparsam eingesetzt werden, da sie die Komplexität erhöhen und die Gesamtkosten einer Form um 15% bis 30% erhöhen.
Befolgen Sie diese Richtlinien beim Entwerfen eines Seitenkerns:
● Der Kern muss sich parallel zur Trennlinie bewegen
● Entwurfswinkel müssen wie gewohnt hinzugefügt werden
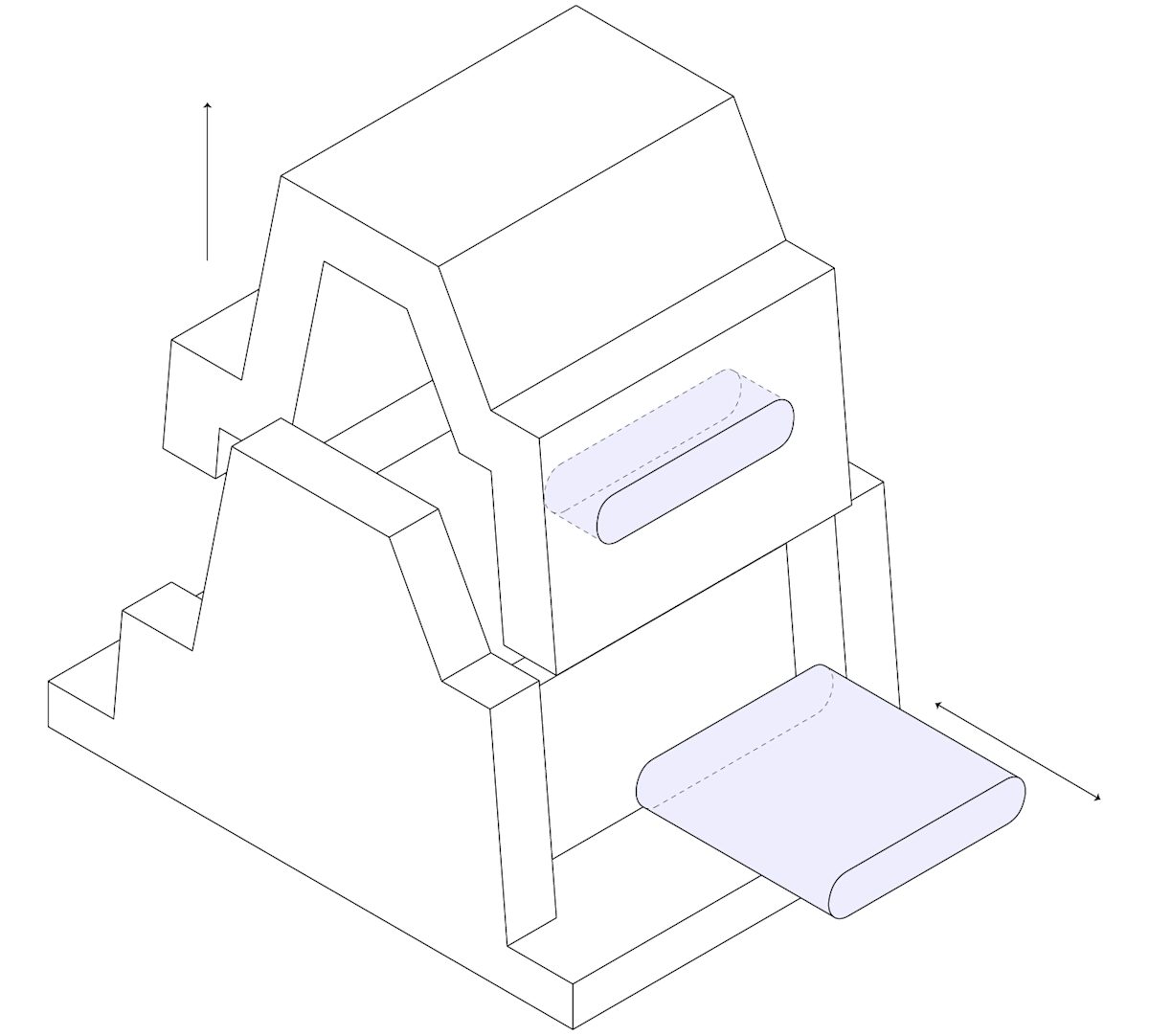
Gängige Designeigenschaften
Nachstehend finden Sie praktische Leitlinien für die Gestaltung der häufigsten Merkmale von Spritzgussteilen. Verwenden Sie sie, um die Funktionalität Ihrer Entwürfe zu verbessern und gleichzeitig die grundlegenden Entwurfsregeln einzuhalten.
Befestigungselemente mit Gewinde (Vorsprünge und Einsätze)
Es gibt 3 Möglichkeiten, einem Spritzgussteil Verbindungselemente hinzuzufügen: durch die Gestaltung eines Gewindes direkt auf dem Teil, durch das Hinzufügen eines Vorsprungs, an dem die Schraube befestigt werden kann, oder durch das Einfügen eines Gewindeeinsatzes.
Die Modellierung eines Gewindes direkt auf dem Teil ist möglich, aber nicht empfehlenswert, da die Zähne des Gewindes im Wesentlichen Hinterschnitte sind, was die Komplexität und die Kosten der Form drastisch erhöht (auf Hinterschnitte wird in einem späteren Abschnitt näher eingegangen). Ein Beispiel für ein Spritzgussteil mit einem Gewinde sind Flaschenverschlüsse.
Bossen
Bossen (Vorsprünge) werden als Befestigungspunkte verwendet (in Verbindung mit selbstschneidenden Schrauben oder Gewindeeinsätzen).
Stellen Sie sich Bossen als kreisförmige Rippen vor - es gelten dieselben allgemeinen Gestaltungsrichtlinien. Dabei sind folgende Faktoren zu berücksichtigen:
● Vermeiden Sie es, Bossen zu entwerfen, die in Hauptwände übergehen
● Stützen Sie die Bossen mit Rippen ab oder verbinden Sie sie mit einer Hauptwand
Für Bossen mit Einsätzen:
● Verwenden Sie einen Außendurchmesser, der 2 × der Nenngröße des Einsatzes entspricht.

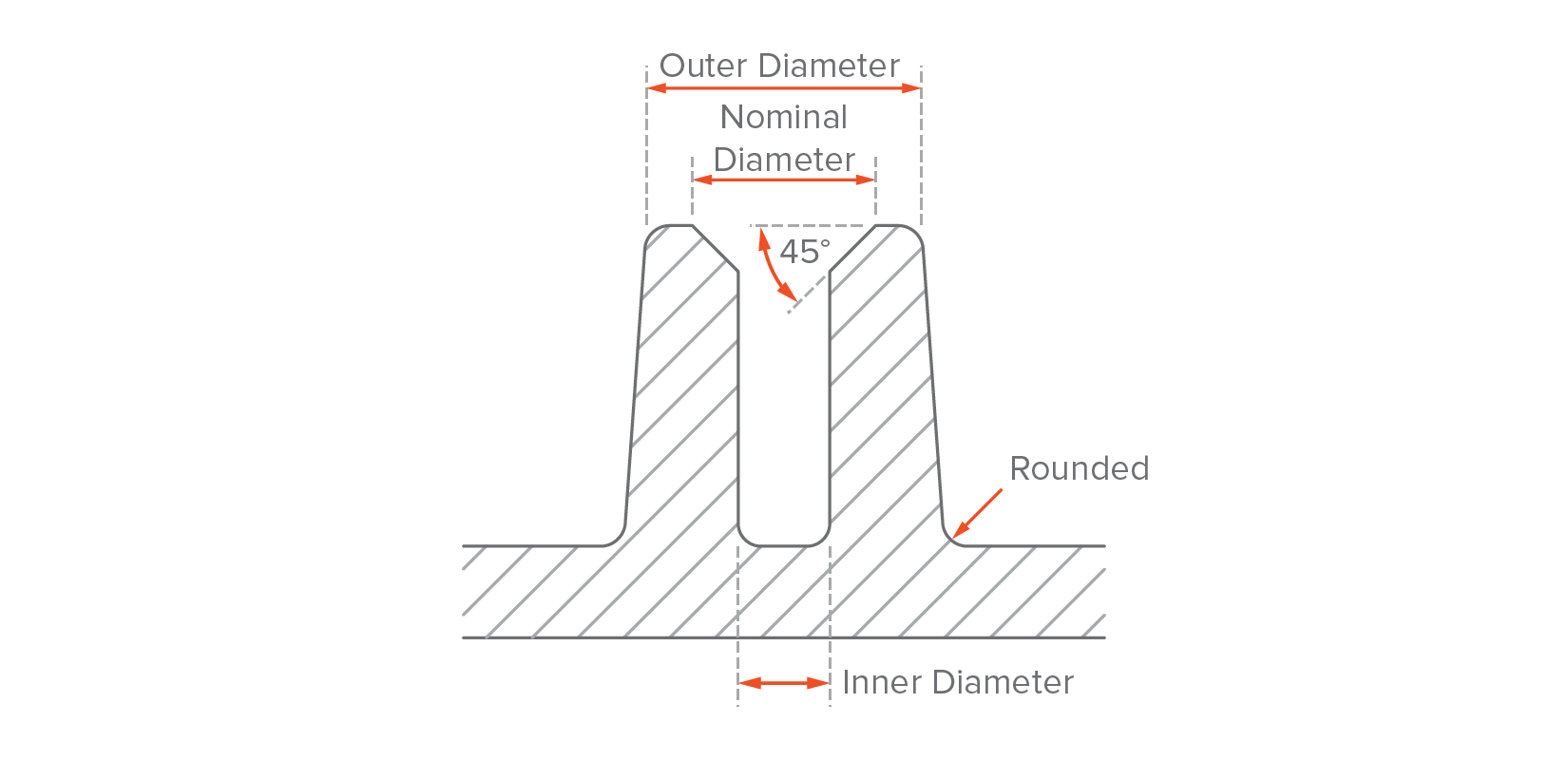
Wenn Vorsprünge als __Befestigungspunkte__ verwendet werden, sollte der Außendurchmesser des Vorsprungs doppelt so groß sein wie der Nenndurchmesser der Schraube oder des Einsatzes und sein Innendurchmesser gleich dem Durchmesser des Schraubenkerns. Das Loch des Vorsprungs sollte sich bis zur Ebene der Basiswand erstrecken, auch wenn nicht die volle Tiefe für die Montage benötigt wird, um eine __gleichmäßige Wandstärke__ im gesamten Feature zu erhalten. Fügen Sie eine Fase zum einfachen Einführen der Schraube oder des Einsatzes hinzu.
__Für beste Ergebnisse:__
Gewinde
Gewinde können direkt zur Formteilkonstruktion hinzugefügt werden, es werden dabei jedoch Hinterschneidungen eingeführt. Alternativ können Gewindeeinsätze verwendet werden.
Befolgen Sie folgende Leitlinien, wenn Sie Teile mit Gewinden konstruieren:
● Fügen Sie an den Kanten des Gewindes ein Relief von 0,8 mm hinzu
● Verwenden Sie ein Gewinde mit einer Steigung von mehr als 0,8 mm (32 Gewindegänge pro Zoll).
● Verwenden Sie vorzugsweise ein Gewinde mit Trapezform oder Sägezahnform.
So gehen Sie mit den erstellten Hinterschneidungen um:
● Ziehen Sie bei Innengewinden in Betracht, Hinterschneidungen zu entfernen
● Platzieren Sie Außengewinde entlang der Trennlinie

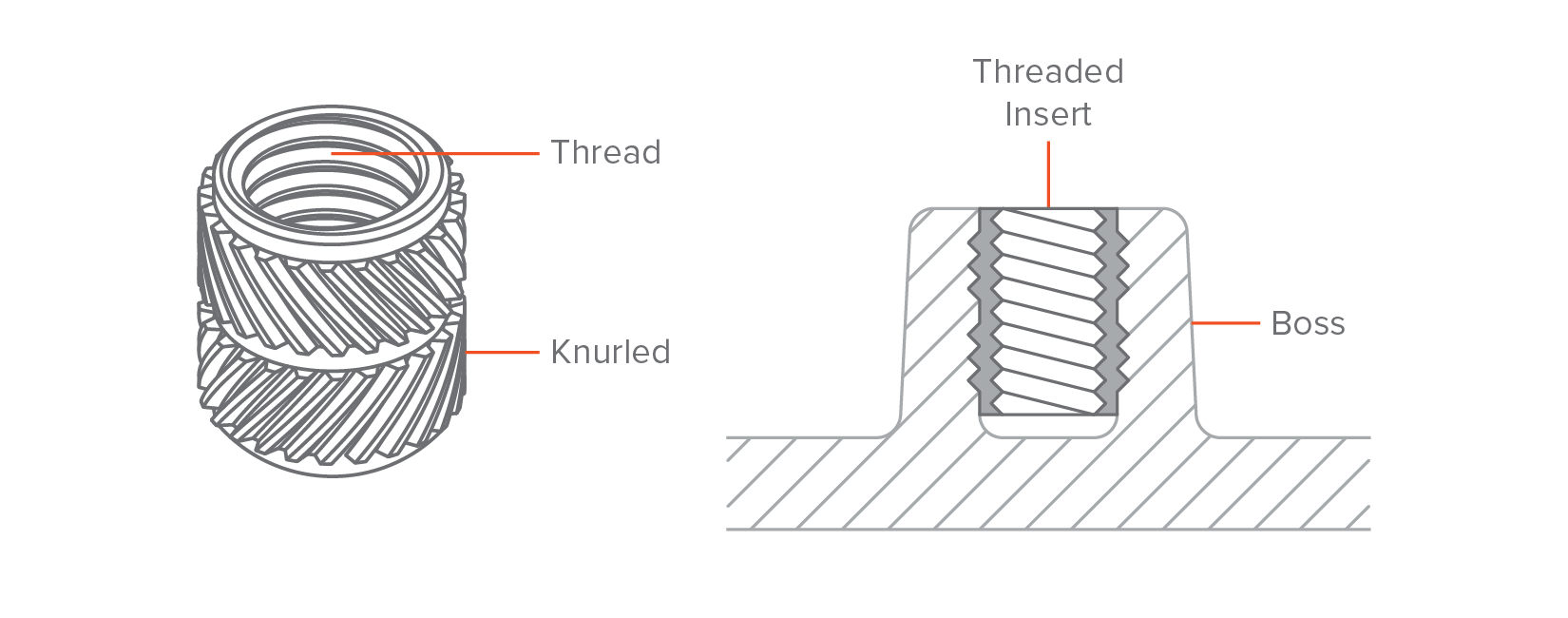
__Für beste Ergebnisse:__
Beste Art und Weise, mit den entstandenen Hinterschnitten umzugehen:
Rippen
Wenn selbst die maximale empfohlene Wandstärke nicht ausreicht, um die funktionalen Anforderungen eines Teils zu erfüllen, können Rippen verwendet werden, um dessen Steifigkeit zu erhöhen.
Bei der Gestaltung von Rippen gilt:
● Verwenden Sie eine Dicke von 0,5 × der Hauptwandstärke
● Definieren Sie eine Höhe, die kleiner als 3 × die Rippendicke ist
● Verwenden Sie eine Grundrundung mit einem Radius größer als ¼ × Rippendicke
● Fügen Sie einen Verzugswinkel von mindestens 0,25° - 0,5° hinzu
● Fügen Sie eine min. Abstand zwischen Rippen und Wänden von 4 × der Rippendicke ein

Schnappverbindungen
Schnappverbindungen sind eine kostengünstige und schnelle Möglichkeit, zwei Teile ohne Befestigungselemente oder Werkzeuge zu verbinden.
Bei der Gestaltung von Schnappverschlüssen für das Spritzgießen gilt:
● Fügen Sie den Seitenwänden des Schnappverschlusses einen Luftzug hinzu
● Verwenden Sie eine Dicke von 0,5 × Hauptwandstärke
● Passen Sie die Breite und Länge an, um die Durchbiegung und Kraft zu steuern
● Überlegen Sie, wie Sie mit der erstellten Hinterschneidung umgehen sollen
Detaillierte Richtlinien finden Sie in diesem Artikel vom MIT.

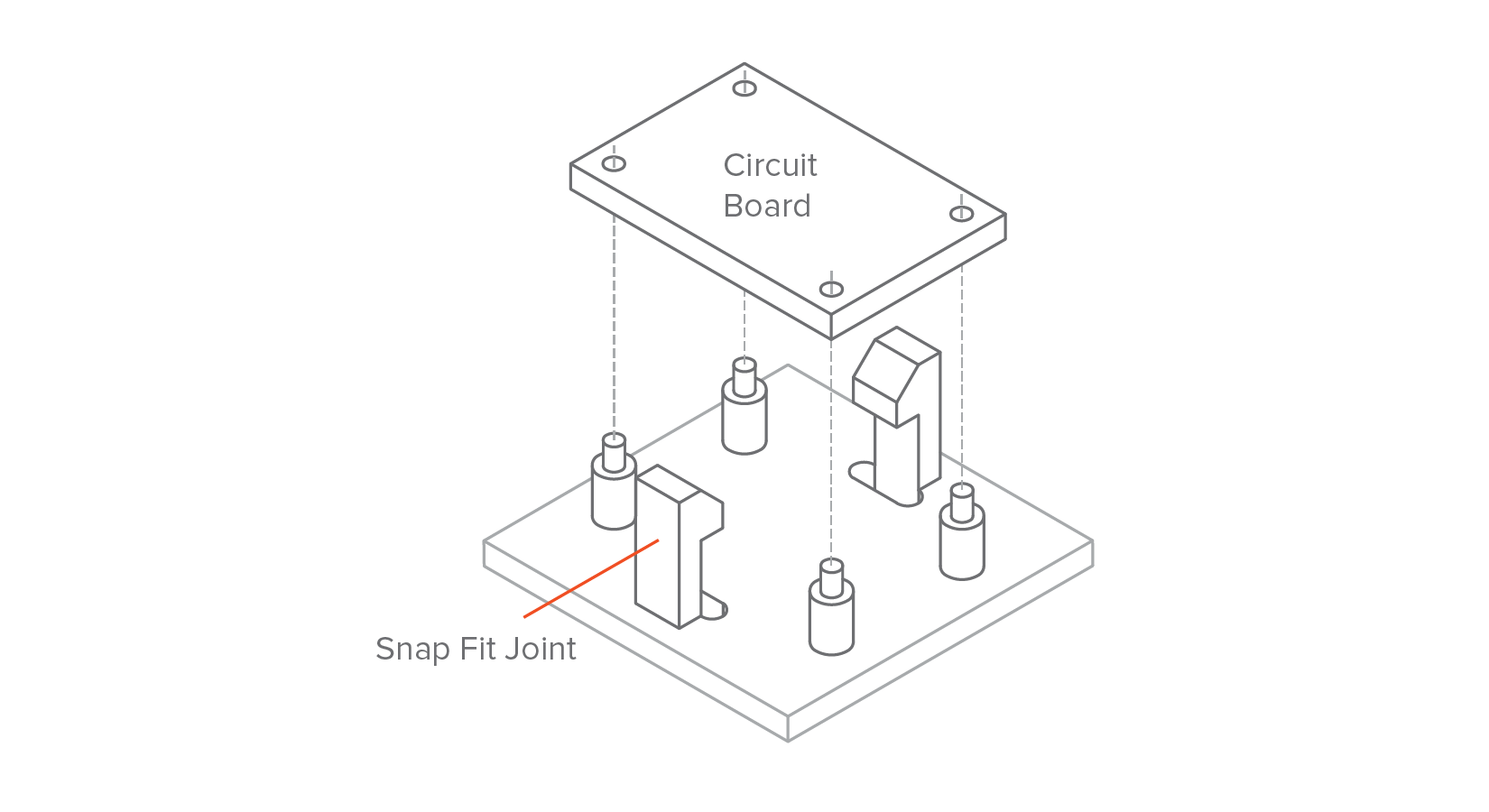
Im obigen Beispiel wird die gebräuchlichste Schnappverbindung (bekannt als __Kragarm-Schnappverbindung__) gezeigt. Wie bei den Rippen fügen Sie Ihren Schnappverbindungen einen Zugwinkel hinzu und verwenden eine Mindestdicke von 0,5x der Wandstärke.
Spezifische Richtlinien für die Konstruktion von Schnappverbindungen ist ein großes Thema, das den Rahmen dieses Artikels sprengt. Ausführlichere Informationen finden Sie in diesem Artikel von MIT.
Für beste Ergebnisse:
Folienscharniere
Folienscharniere sind dünne Kunststoffabschnitte, die zwei Segmente eines Teils verbinden und gebogen und geklappt werden können.
Im Folgenden finden Sie einige Tipps zum Entwerfen eines Folienscharniers:
● Wählen Sie ein flexibles Material (zum Beispiel PP, PE oder Nylon)
● Entwerfen Sie die Scharniere mit einer Dicke zwischen 0,20 und 0,35 mm
● Verwenden Sie Schultern mit einer Dicke, die der Dicke der Hauptwand entspricht
● Fügen Sie so große Füllungen wie möglich hinzu

A well-designed hinge is shown below. The recommended minimum thickness of the hinge ranges between 0.20 and 0.35 mm, with higher thicknesses resulting in more durable, but stiffer, parts.
{{img}}
*Example of a living hinge (left) and recommended design dimensions for PP or PE (right)*
Before going to full-scale production, prototype your living hinges using
CNC machining or
3D printing to determine the geometry and stiffness that best fits your application. Add generous fillets and design shoulders with a uniform wall thickness as the main body of the part to improve the material flow in the mold and minimize the stresses. Divide hinges longer than 150 mm in two (or more) to improve lifetime.
For detailed guidelines, please refer to this MIT guide.
For best results:
-
Design hinges with a thickness between 0.20 and 0.35 mm
-
Select a flexible material (PP, PE or PA) for parts with living hinges
-
Use shoulders with a thickness equal the thickness of the main wall
-
Add fillets as large as possible
Quetschrippen
Quetschrippen verformen sich und erzeugen Reibung zwischen dem Teil und dem eingesetzten Bauteil, wodurch es an seinem Platz gesichert wird.
Sie sind eine schnelle und kostengünstige Methode, um Lager oder andere Einsätze in Ihre Konstruktionen einzubauen. Verwenden Sie für High-End-Anwendungen stattdessen eine Presspassung.
Beim Entwerfen von Quetschrippen gilt:
● Verwenden Sie drei kreisförmige Rippen mit einem Radius von 2 mm
● Fügen Sie eine minimale Überlappung von 0,25 mm zwischen Rippe und Einsatz hinzu
● Fügen Sie dem Loch einen Luftzug hinzu, verziehen Sie jedoch nicht die Rippen

Ein Beispiel für ein Teil mit Quetschrippen ist unten dargestellt. Die Verwendung von drei Quetschrippen wird empfohlen, um eine gute Ausrichtung zu gewährleisten. Die empfohlene Höhe/Radius für jede Rippe beträgt 2 mm. Fügen Sie ein Mindestübermaß von 0,25 mm zwischen der Quetschrippe und dem eingebauten Teil hinzu. Wegen des geringen Oberflächenkontakts mit der Form können Quetschrippen ohne einen Entformungswinkel entworfen werden.
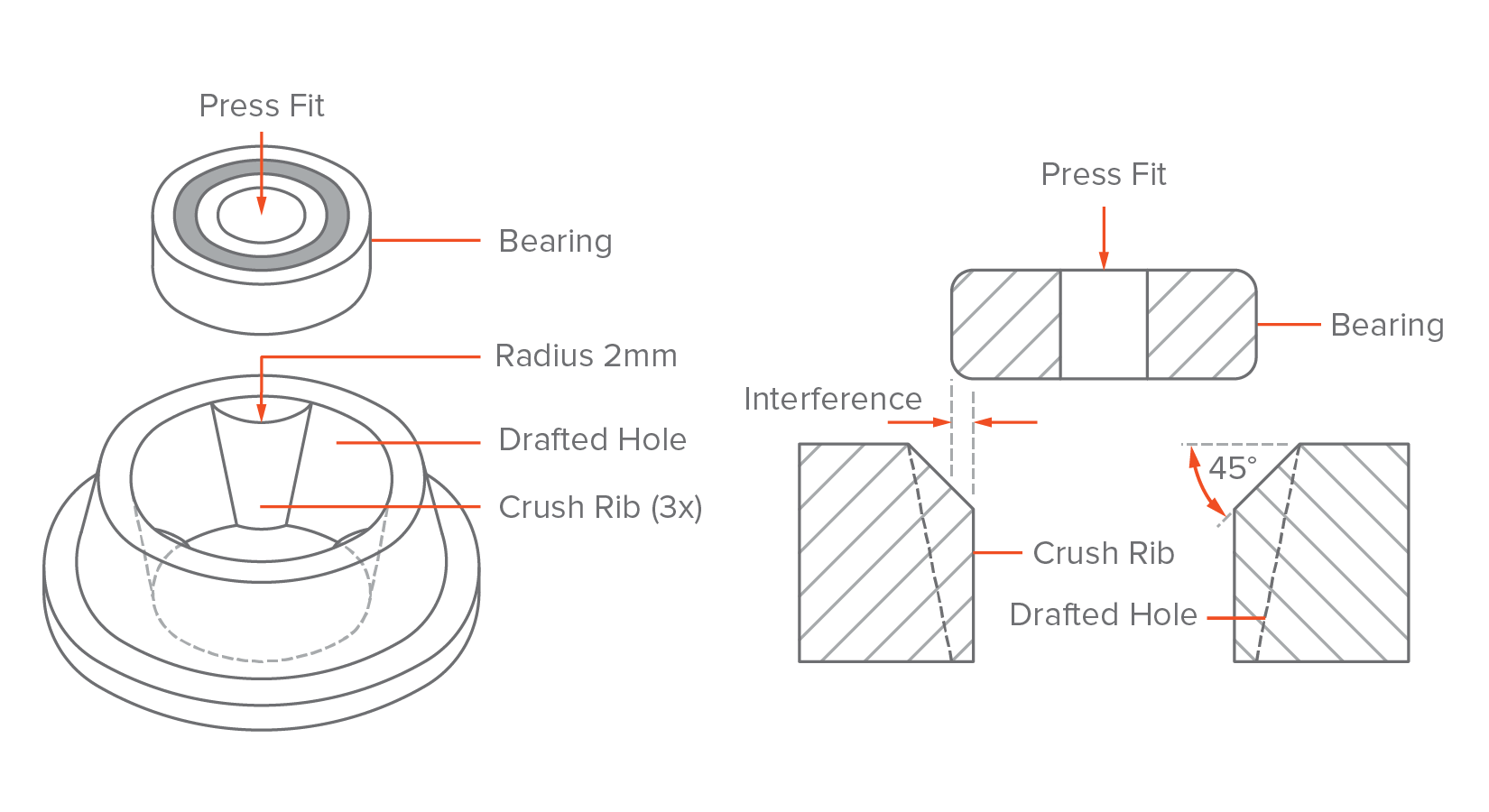
__Für beste Ergebnisse:__
Schrift und Symbole
Text, Logos und andere Symbole können auf der Oberfläche von Spritzgussteilen eingraviert oder geprägt werden.
Hier einige Tipps zum Hinzufügen von Text:
● Prägen ist besser Gravieren
● Richten Sie den Text senkrecht zur Trennlinie aus
● Verwenden Sie eine Höhe (oder Tiefe) von mehr als 0,5 mm
● Verwenden Sie eine Schrift mit einheitlicher Schriftstärke
● Die Schriftgröße sollte mindestens 20 Punkte betragen

Für beste Ergebnisse:
Toleranzen
Das Spritzgießen erzeugt typischerweise Teile mit Toleranzen von ± 0,500 mm.
Engere Toleranzen sind unter bestimmten Umständen möglich (bis zu ± 0,125 mm - und sogar ± 0,025 mm), erhöhen jedoch die Kosten drastisch.
Bei kleinen Serien (< 10.000 Teile) sollten Sie eine zweite Operation (z. B. Bohren) in Betracht ziehen, um die Genauigkeit zu verbessern. Dies stellt die korrekte Interaktion des Teils mit anderen Bauteilen oder Einsätzen sicher (z. B. bei Verwendung von Presspassungen).

Designregeln für das Spritzgießen
Lassen Sie uns sehen, wie diese Prozessbeschränkungen in umsetzbare Gestaltungsrichtlinien umgesetzt werden können.
In den folgenden Abschnitten fassen wir die wichtigsten Designregeln für die Konstruktion von Spritzgussteilen sowie Tipps zur korrekten Konstruktion der häufigsten Merkmale von Spritzgussteilen zusammen.
Lesen Sie die vollständigen Gestaltungsleitlinien für Spritzguss →
Verwenden Sie eine konstante Wandstärke
Empfohlene Dicke: 1 mm und 3 mm
Konstruieren Sie Teile immer mit der kleinstmöglichen (und konstanten) Wandstärke, um Verwerfungen und Einsenkungen zu vermeiden.
Wenn dickere Querschnitte erforderlich sind, höhlen Sie diese aus und versteifen Sie diese stattdessen mit Rippen (#common-design-features). Beachten Sie, dass jede Erhöhung der Wandstärke um 10% zu einer Erhöhung der Steifigkeit um ca. 30% führt.
Siehe Empfehlungen für materialspezifische Wandstärken →

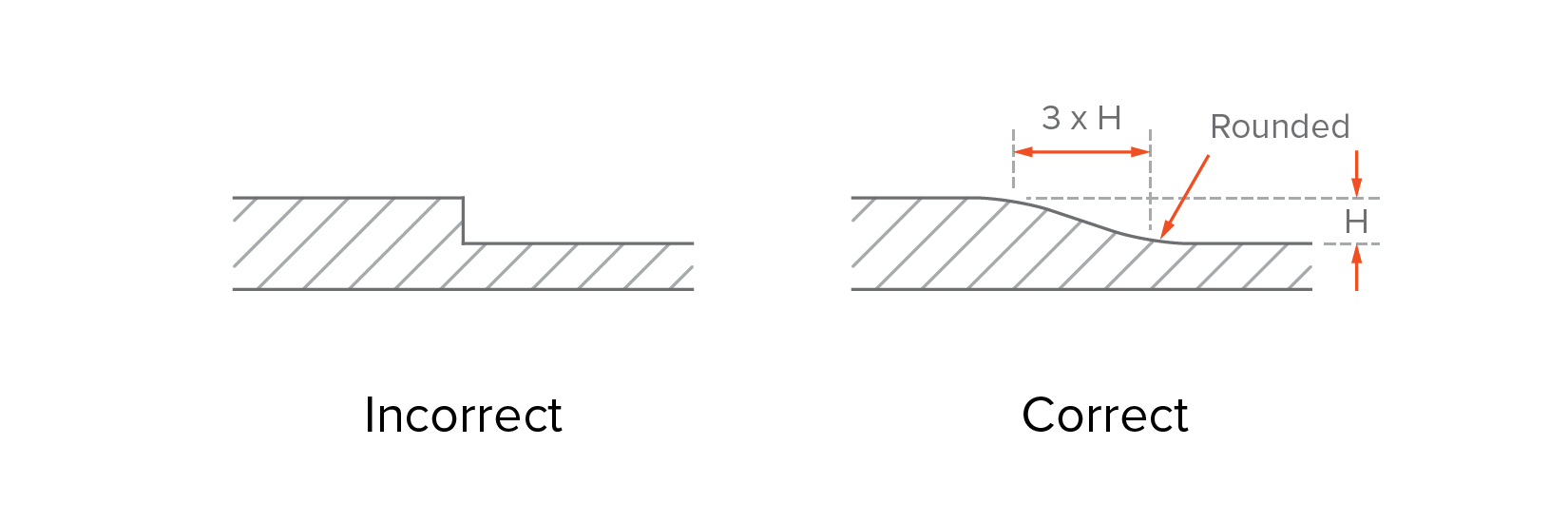
Eine Wanddicke zwischen 1,2 mm und 3 mm ist ein sicherer Wert für die meisten Materialien. Die nächste Tabelle fasst spezifische __empfohlene Wanddicken__ für einige der gebräuchlichsten Spritzgussmaterialien zusammen:
Material | Empfohlene Wandstärke [mm] | Empfohlene Wandstärke [inches] |
---|---|---|
Polypropylene (PP) | 0.8 - 3.8 mm | 0.03'' - 0.15'' |
ABS | 1.2 - 3.5 mm | 0.045'' - 0.14'' |
Polyethylene (PE) | 0.8 - 3.0 mm | 0.03'' - 0.12'' |
Polystyrene (PS) | 1.0 - 4.0 mm | 0.04'' - 0.155'' |
Polyurethane (PUR) | 2.0 - 20.0 mm | 0.08'' - 0.785'' |
Nylon (PA 6) | 0.8 - 3.0 mm | 0.03'' - 0.12'' |
Polycarbonate (PC) | 1.0 - 4.0 mm | 0.04'' - 0.16'' |
PC/ABS | 1.2 - 3.5 mm | 0.045'' - 0.14'' |
POM (Delrin) | 0.8 - 3.0 mm | 0.03'' - 0.12'' |
PEEK | 1.0 - 3.0 mm | 0.04'' - 0.12'' |
Silikon | 1.0 - 10.0 mm | 0.04'' - 0.40'' |
Für beste Ergebnisse:_
Dickere Abschnitte aushöhlen
Dicke Abschnitte können zu verschiedenen Defekten führen, einschließlich Verziehen und Absinken. Es ist wichtig, die maximale Dicke eines beliebigen Abschnitts Ihres Entwurfs auf die empfohlenen Werte zu beschränken, indem Sie ihn hohl machen.
Um die Festigkeit von Hohlprofilen zu verbessern, verwenden Sie Rippen, um Strukturen mit gleicher Festigkeit und Steifigkeit, aber reduzierter Wanddicke zu entwerfen. Ein gut konstruiertes Teil mit Hohlprofilen ist unten dargestellt:
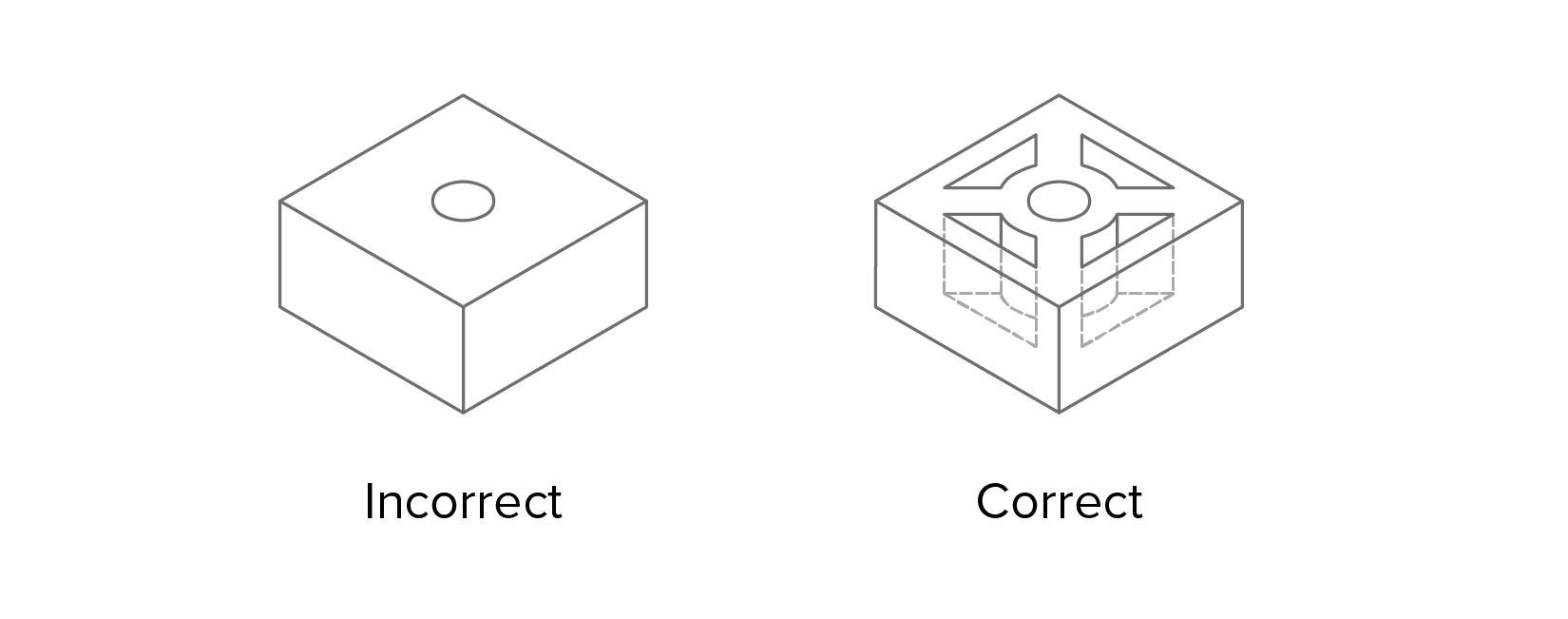
<
Rippen können auch verwendet werden, um die Steifigkeit __horizontaler Abschnitte__ zu verbessern, ohne ihre Dicke zu erhöhen. Beachten Sie jedoch, dass die Wanddickenbeschränkungen weiterhin gelten. Das Überschreiten der empfohlenen Rippendicke (siehe unten) kann zu Einfallstellen führen.
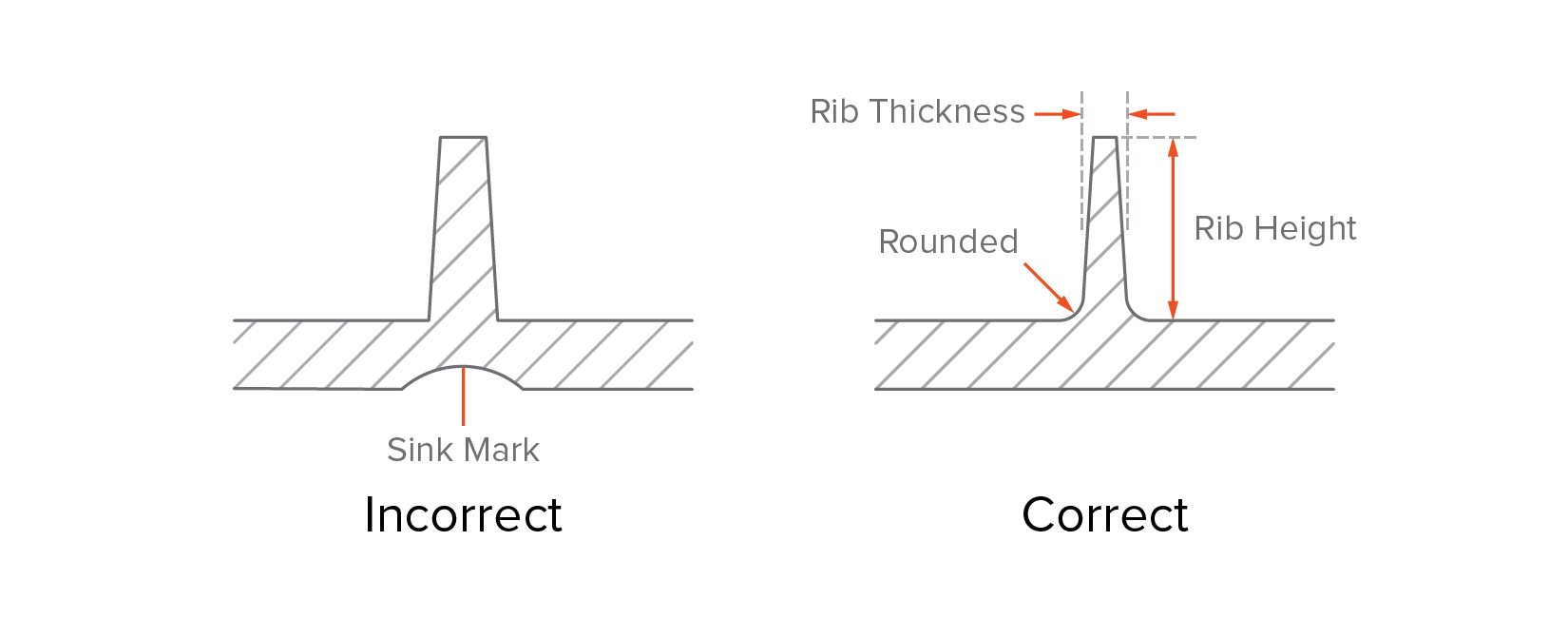
<
Für beste Ergebnisse:
Glatte Übergänge hinzufügen
Empfohlen: 3 × Wandstärkendifferenz
Manchmal lassen sich Querschnitte mit unterschiedlichen Wandstärken nicht vermeiden. Verwenden Sie in diesen Fällen eine Fase oder Verrundung, um den Übergang so glatt wie möglich zu gestalten.
Ebenso muss die Basis vertikaler Merkmale (wie Rippen, Vorsprünge, Schnappverschlüsse) immer abgerundet sein.

Alle Kanten abrunden
Innenkanten:> 0,5 × Wandstärke
Außenkanten: Innenkante + Wandstärke
Die Regel der konstanten Wandstärke muss auch auf die Ecken des Teils angewendet werden. Fügen Sie an allen Innen- und Außenkanten eine Verrundung mit einem möglichst großen Radius hinzu.

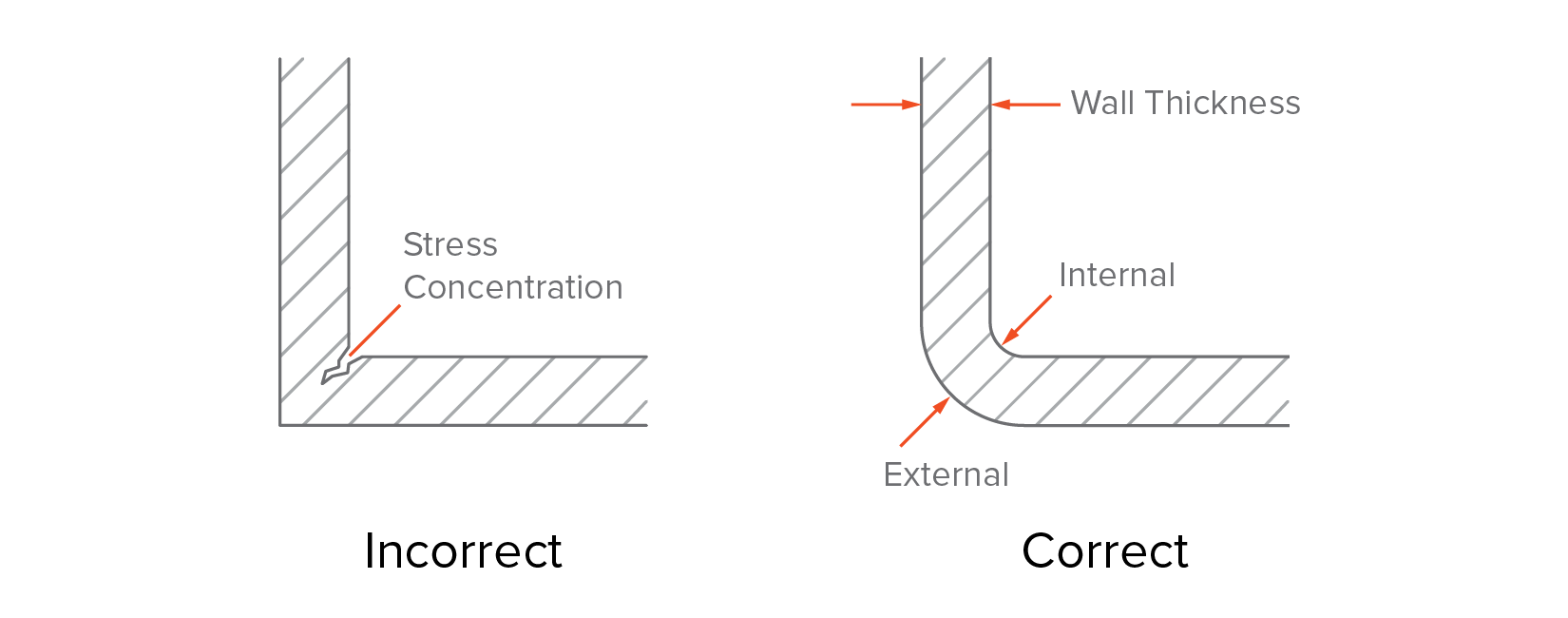
<center>*Fügen Sie breite Radien an allen Kanten hinzu, um eine gleichmäßige Wandstärke zu erhalten und Fehler zu vermeiden*</center>
Für beste Ergebnisse:
Entformungswinkel hinzufügen
Empfohlenes Minimum:> 2°
Fügen Sie allen vertikalen Wänden einen Entformungswinkel hinzu, um das Auswerfen des Teils zu erleichtern und Zugspuren zu vermeiden. Wenn sie einem funktionalen Zweck dienen, können die Außenwände unbearbeitet bleiben (siehe Legosteine).
Erhöhen Sie den Entformungswinkel in den folgenden Fällen über den empfohlenen Wert:
● Erhöhen Sie ihn bei Teilen, die größer als 50 mm sind, alle 25 mm um 1°
● Erhöhen Sie den Entformungswinkel für strukturierte Teile um 1° -2°

Eine gute Faustregel ist es, den Entformungswinkel um einen Grad pro 25 mm zu erhöhen. Fügen Sie zum Beispiel einen Entformungswinkel von 3o Grad zu einem 75 mm hohen Feature hinzu. Ein größerer Entformungswinkel sollte verwendet werden, wenn das Teil eine texturierte Oberfläche hat. Als Faustregel gilt: Fügen Sie zu den Ergebnissen der obigen Berechnungen 1 o bis 2 o Grad hinzu.
«br>
Denken Sie daran, dass auch für Rippen Zugwinkel erforderlich sind. Beachten Sie jedoch, dass durch das Hinzufügen eines Winkels die Dicke der Rippenoberseite reduziert wird. Stellen Sie also sicher, dass Ihr Entwurf die empfohlene Mindestwandstärke einhält.
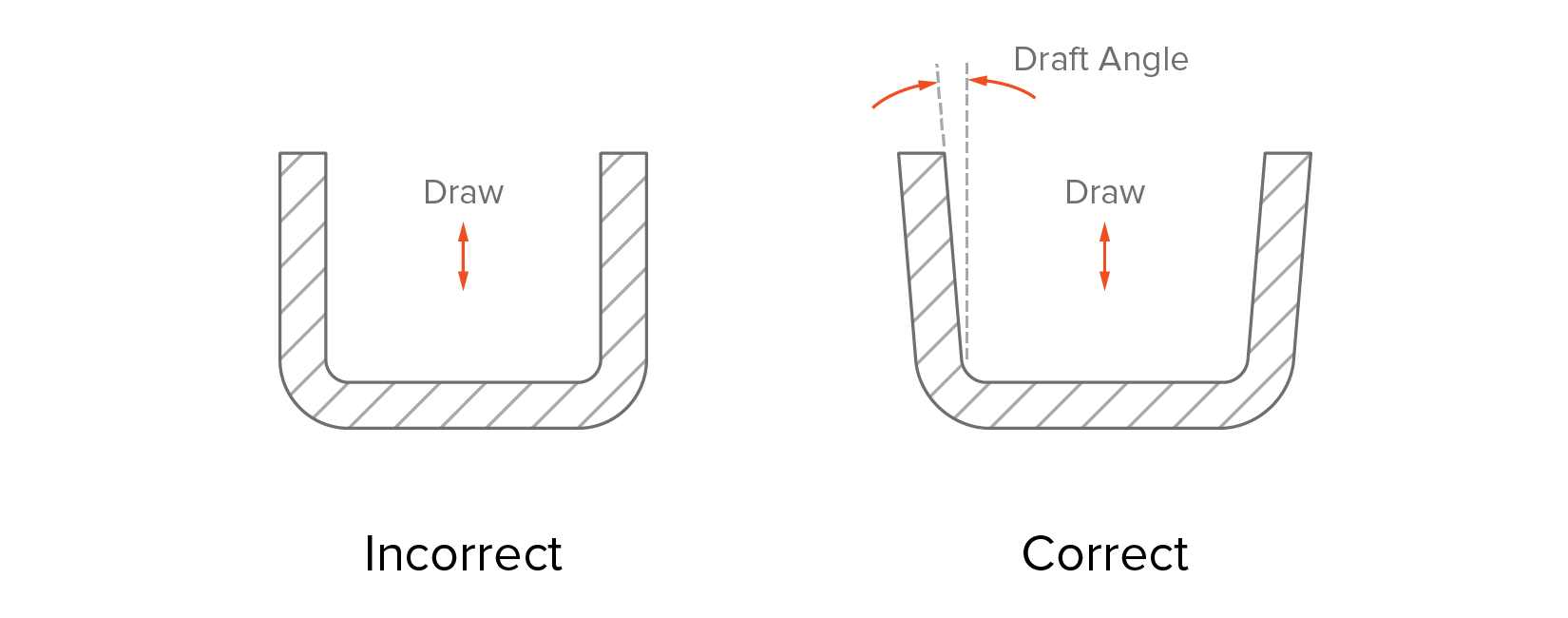
__Für beste Ergebnisse:__
Part 3
Kunststoff Spritzguss: Materialien
Spritzguss ist mit einer Vielzahl von Kunststoffen möglich. In diesem Abschnitt erfahren Sie mehr über die wichtigsten Eigenschaften der beliebtesten Materialien. Wir gehen auch auf die Standardoberflächen ein, die für Spritzgussteile verwendet werden können.
Spritzgussmaterialien
Alle Thermoplaste können spritzgegossen werden. Einige Duroplaste und Flüssigsilikone sind ebenfalls für das Spritzgussverfahren geeignet.
Sie können auch mit Fasern, Kautschukpartikeln, Mineralien oder Flammschutzmitteln vermischt werden, um ihre physikalischen Eigenschaften zu ändern. Zum Beispiel kann Glasfaser mit den Pellets in Verhältnissen von 10%, 15% oder 30% gemischt werden, was zu Teilen mit höherer Steifheit führt.
Ein Additiv, das üblicherweise verwendet wird, um die Steifigkeit der Spritzgussteile zu verbessern, ist Glasfaser. Die Glasfasern können in einem Verhältnis von 10%, 15% oder 30% mit dem Granulat gemischt werden, wodurch sich unterschiedliche mechanische Eigenschaften ergeben.
«br>
Farbstoff kann der Mischung hinzugefügt werden (in einem Verhältnis von etwa 3%), um eine große Vielfalt an farbigen Teilen zu erzeugen. Zu den Standardfarben gehören Rot, Grün, Gelb, Blau, Schwarz und Weiß, und sie können gemischt werden, um verschiedene Schattierungen zu erzeugen.
Oberflächen- und SPI-Standards
Spritzgussteile werden in der Regel nicht nachbearbeitet, sondern die Form selbst kann unterschiedlich endbearbeitet werden.
Auf diese Weise können ästhetische Anforderungen (z. B. eine spiegelglatte oder matte Oberfläche) oder technische Anforderungen (z. B. spezifische Oberflächenrauheit oder Toleranzen) erfüllt werden.
Die Society of Plastics Industry (SPI) hat verschiedene Standardveredelungsverfahren eingeführt, die zu unterschiedlichen Oberflächenveredelungen von Teilen führen.
Oberfläche | Beschreibung | Anwendung |
---|---|---|
Glänzende Oberfläche SPI-Standard: A-1, A-2, A-3 |
Die Form wird geglättet und anschließend mit einem Diamantschliff poliert, wodurch Teile mit einer spiegelnden Oberfläche erhalten werden. | Geeignet für Teile, die für kosmetische oder funktionelle Zwecke die glatteste Oberfläche benötigen (Ra <0,10 μm) |
Halbglänzende Oberfläche SPI-Standard: B-1, B-2, B-3 |
Die Form wird mit feinkörnigem Schleifpapier geglättet, wodurch Teile mit einer feinen Oberflächenbeschaffenheit erhalten werden. | Geeignet für Teile, die ein gutes optisches Erscheinungsbild, aber keinen Hochglanz erfordern. |
Matte Oberfläche SPI-Standard: C-1, C-2, C-3 |
Die Form wird mit feinem Steinpulver geglättet, wobei alle Bearbeitungsspuren entfernt werden. | Geeignet für Teile mit geringen ästhetischen Anforderungen, aber wenn Bearbeitungsspuren nicht akzeptabel sind. |
Texturierte Oberfläche SPI-Standard: D-1, D-2, D-3 |
Die Form wird zuerst mit feinem Steinpulver geglättet und dann sandgestrahlt, wodurch eine strukturierte Oberfläche entsteht. | Geeignet für Teile, die eine seidenmatte oder matt strukturierte Oberfläche benötigen. |
Oberfläche ab Maschine | Die Form wird nach Ermessen des Maschinenführers fertiggestellt. Werkzeugspuren können sichtbar sein. | Geeignet für nicht kosmetische, industrielle Teile oder versteckte Komponenten. |
Part 4
Kostensenkungstipps
Erfahren Sie mehr über die wichtigsten Kostentreiber beim Spritzgießen und drei umsetzbare Designtipps, mit denen Sie die Kosten senken und Ihr Projekt im Rahmen Ihres Budgets halten können.
Kostentreiber im Spritzguss
Die Hauptkostentreiber im Spritzguss sind:
- Werkzeugkosten bestimmt durch die Gesamtkosten für Entwurf und Bearbeiten des Formwerkzeugs
- Materialkosten bestimmt durch das Volumen des verwendeten Materials und dessen Preis pro Kilogramm
- Produktionskosten richten sich nach der Gesamtbetriebszeit der Spritzgießmaschine
Die Werkzeugkosten sind konstant (von 3.000 bis 5.000 USD) und unabhängig von der Gesamtzahl der hergestellten Teile, während die Material- und Produktionskosten vom Produktionsvolumen abhängen.
Bei kleineren Produktionsserien (1.000 bis 10.000 Stück) haben die Werkzeugkosten den größten Einfluss auf die Gesamtkosten (ca. 50-70%). Es lohnt sich also, Ihr Design entsprechend zu ändern, um den Herstellungsprozess der Form zu vereinfachen (und damit die Kosten zu senken).
Bei größeren Stückzahlen bis zur Großserienproduktion (10.000 bis über 100.000 Stück) wird der Beitrag der Werkzeugkosten zu den Gesamtkosten durch die Material- und Produktionskosten übertroffen. Ihr Hauptanliegen bei der Entwicklung sollte es daher sein, sowohl das Volumen als auch die Zeit des Spritzgusszyklus‘ zu minimieren.
Hier haben wir einige Tipps zusammengestellt, mit denen Sie die Kosten Ihres Spritzgussprojekts minimieren können.
Tipp 1: Halten Sie sich an die gerade Ziehform

Seitenkerne und andere Mechanismen in der Form können die Werkzeugkosten schnell um 15% bis 30% erhöhen. Dies entspricht einem zusätzlichen Mindestaufwand für die Werkzeuge von ca. 1.000 bis 1.500 US-Dollar.
In einem früheren Abschnitt haben wir Möglichkeiten untersucht, mit Hinterschneidungen umzugehen. Um Ihr Produktionsbudget einzuhalten, sollten Sie keine Seitenkerne und andere Mechanismen verwenden, es sei denn, dies ist unbedingt erforderlich.
Tipp #2: Gestalten Sie das Spritzgussteil neu, um Hinterschneidungen zu vermeiden
Hinterschnitte erhöhen immer die Kosten und Komplexität sowie die Wartung der Form. Eine geschickte Umgestaltung kann Hinterschnitte oft beseitigen.
Tipp #3: Verkleinern Sie das Spritzgussteil
Kleinere Teile können schneller gegossen werden, was zu einem höheren Produktionsausstoß führt und die Kosten pro Teil senkt. Kleinere Teile führen auch zu geringeren Materialkosten und reduzieren den Preis der Form.
Tipp #4: Passen Sie mehrere Teile in eine Form ein

In einem vorherigen Abschnitt haben wir gesehen, dass das Einpassen mehrerer Teile in dieselbe Form eine gängige Praxis ist. Normalerweise passen sechs bis acht kleine identische Teile in ein und dieselbe Form, was die Gesamtproduktionszeit um etwa 80% verkürzt.
Teile mit unterschiedlichen Geometrien können auch in die gleiche Form passen (siehe Beispiel Modellflugzeug). Dies ist eine großartige Lösung zur Reduzierung der Gesamtkosten einer Baugruppe. Wie die Teile nicht sein sollten
Hier eine fortgeschrittene Technik:
In einigen Fällen ist der Hauptteil von zwei Teilen einer Baugruppe derselbe. Mit kreativem Design können Sie Verriegelungspunkte oder Scharniere an symmetrischen Stellen erstellen, die das Teil im Wesentlichen spiegeln. Auf diese Weise können beide Hälften mit derselben Form hergestellt werden, wodurch sich die Werkzeugkosten halbieren.
Tipp #5: Vermeiden Sie kleine Details
Die Herstellung einer Form mit kleinen Details erfordert längere Bearbeitungs- und Nachbearbeitungszeiten. Der Text ist ein Beispiel dafür und kann sogar spezielle Bearbeitungstechniken wie die Funkenerosion (EDM) erfordern, was zu höheren Kosten führt.
Tipp #6: Verwenden Sie minderwertige Oberflächen
Oberflächenbehandlungen werden in der Regel von Hand auf die Form aufgetragen, was ein teurer Prozess sein kann, insbesondere bei hochwertigen Oberflächenbehandlungen. Wenn Ihr Teil nicht für den kosmetischen Gebrauch bestimmt ist, sollten Sie keine kostspielige hochwertige Oberflächenbehandlung vornehmen.
Tipp #7: Minimieren Sie das Teilevolumen, indem Sie die Wandstärke verringern

Die Reduzierung der Wandstärke Ihres Teils ist der beste Weg, um das Teilevolumen zu minimieren. Auf diese Weise wird nicht nur weniger Material verbraucht, sondern auch der Spritzgusszyklus wird erheblich beschleunigt.
Zum Beispiel kann die Reduzierung der Wandstärke von 3 mm auf 2 mm die Zykluszeit um 50% bis 75% reduzieren.
Durch dünnere Wände kann die Form schneller gefüllt werden. Noch wichtiger ist, dass Teile, die dünner sind, viel schneller abkühlen und erstarren. Denken Sie daran, dass etwa die Hälfte des Spritzgusszyklus für die Verfestigung des Teils aufgewendet wird, während die Maschine im Leerlauf bleibt.
Es muss darauf geachtet werden, die Steifigkeit des Teils nicht zu stark zu verringern und seine mechanische Leistung nicht zu beeinträchtigen. Rippen können an wichtigen Stellen verwendet werden, um die Steifigkeit zu erhöhen.
Tipp #8: Sekundärbearbeitungen in Betracht ziehen
Bei kleineren Produktionsvolumen (weniger als 1000 Teile) kann es kostengünstiger sein, einen sekundären Arbeitsgang zur Fertigstellung Ihrer Spritzgussteile einzusetzen. Beispielsweise könnten Sie nach dem Gießen ein Loch bohren, anstatt eine teure Form mit seitlich wirkenden Kernen zu verwenden.
Part 5
Mit dem Spritzguss starten
Wie geht es weiter, wenn Ihr Design fertig und für das Spritzgießen optimiert ist? In diesem Abschnitt führen wir Sie durch die Schritte, die erforderlich sind, um mit der Herstellung im Spritzgussverfahren zu beginnen.
Schritt 1: Klein anfangen und schnell Prototypen erstellen
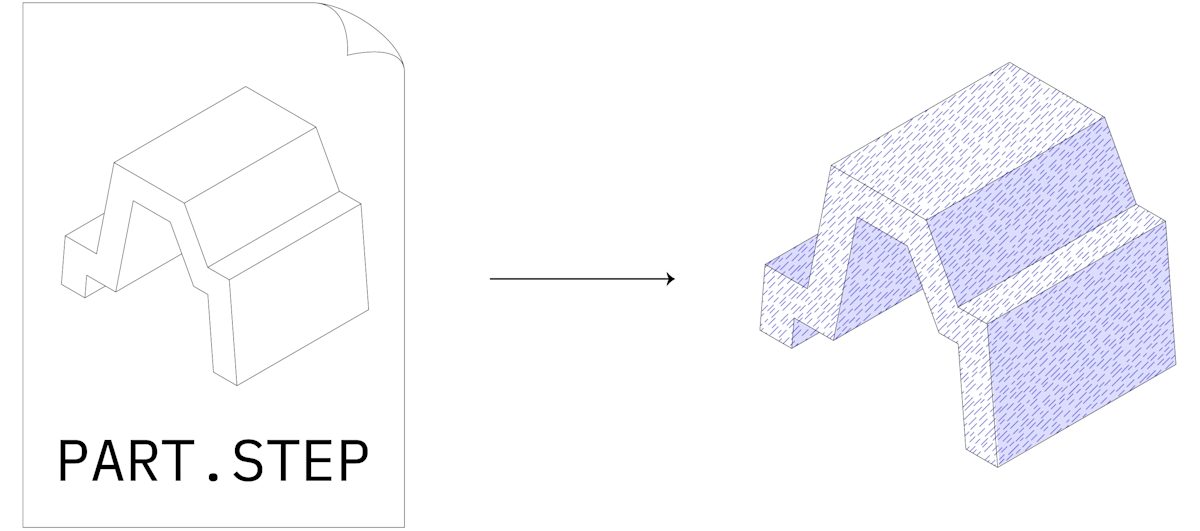
Bevor Sie sich für teure Spritzgusswerkzeuge entscheiden, erstellen und testen Sie zunächst einen funktionalen Prototyp Ihres Designs.
Dieser Schritt ist entscheidend für die Einführung eines erfolgreichen Produkts. Auf diese Weise können Entwurfsfehler frühzeitig erkannt werden, während die Änderungskosten immer noch niedrig sind.
Es gibt drei Lösungen für das Prototyping:
- 3D-Druck (mit SLS, SLA oder Material Jetting)
- CNC-Bearbeitung für Kunststoff
- Kleinserien-Spritzguss mit 3D-gedruckten Formen
Diese drei Prozesse können realistische Prototypen für Form und Funktion erzeugen, die dem Aussehen des fertigen Spritzgussprodukts sehr ähnlich sind.
Verwenden Sie die nachstehenden Informationen als schnelle Vergleichsanleitung, um zu entscheiden, welche Lösung für Ihre Anwendung am besten geeignet ist.
Prototyping mit 3D-Druck
Mindestmenge: 1 Teil
Typische Kosten: $ 20 - $ 100 pro Teil
Vorlaufzeit: 2 - 5 Werktage
Erfahren Sie mehr über diesen Prozess hier →

Prototyping mit CNC-Bearbeitung
Mindestmenge: 1 Teil
Typische Kosten: $ 100 - $ 500 pro Teil
Vorlaufzeit: 5 - 10 Tage
Erfahren Sie mehr über diesen Prozess hier: →

Prototyping mit Kleinserien-Spritzguss
Mindestmenge: 10 - 100 Teile
Typische Kosten: $ 1000 - $ 4000 insgesamt
Vorlaufzeit: 5 - 10 Tage
[Erfahren Sie mehr über diesen Prozess hier: →] (https://www.hubs.com/de/spritzguss/)
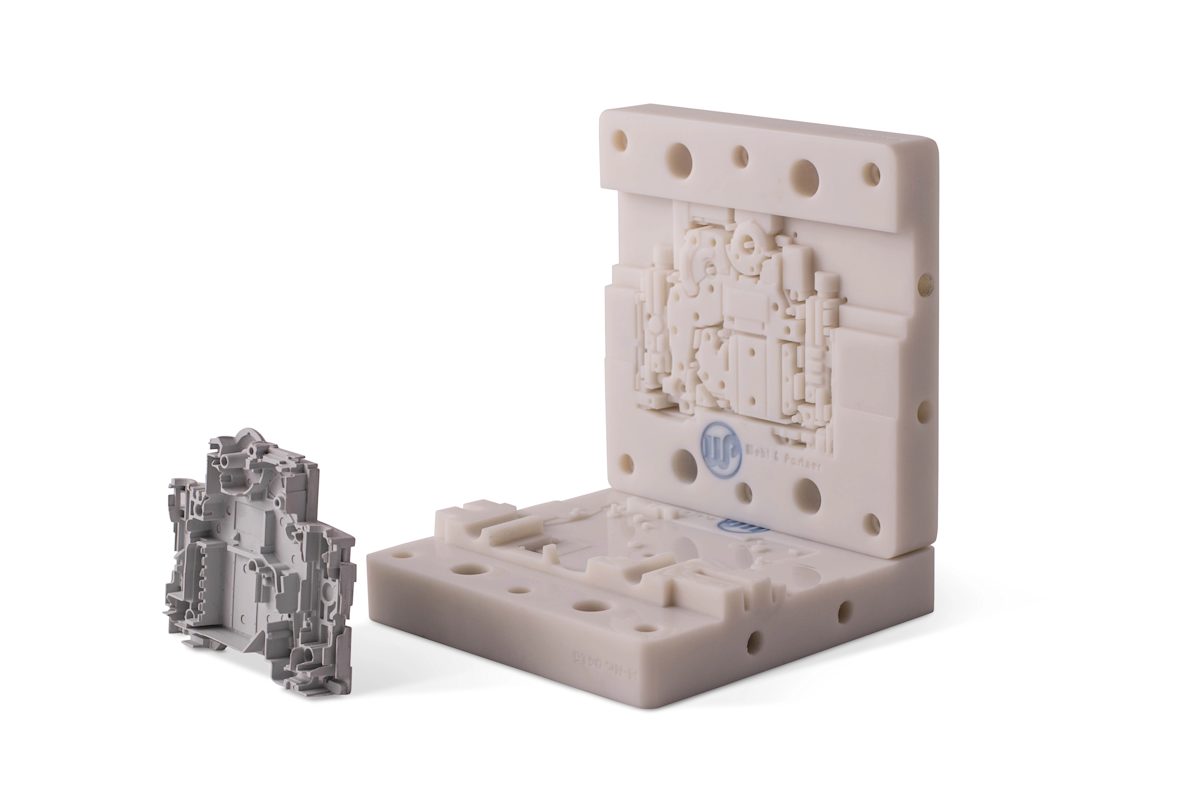
Schritt 2: Führen Sie einen „Probelauf“ durch (500 - 10.000 Teile)

Nachdem das Design fertiggestellt ist, ist es an der Zeit, mit dem Spritzgießen in einem kleinen Pilotlauf zu beginnen.
Das Mindestbestellvolumen für das Spritzgießen beträgt 500 Stück. Für diese Mengen werden die Formen normalerweise aus Aluminium CNC-gefräst. Aluminiumformen sind relativ einfach herzustellen und kostengünstig (ab etwa 3.000 bis 5.000 USD), können jedoch bis zu 5.000 bis 10.000 Spritzzyklen standhalten.
Zu diesem Zeitpunkt variieren die typischen Kosten pro Teil zwischen 1 USD und 5 USD, abhängig von der Geometrie Ihres Designs und dem ausgewählten Material. Die typische Fertigungszeit für solche Bestellungen beträgt 6-8 Wochen.
Lassen Sie sich nicht durch den Begriff „Probelauf“ verwirren. Wenn Sie nur einige tausend Teile benötigen, ist dies Ihr letzter Produktionsschritt.
Die Teile, die mit „Probe“-Aluminiumformen hergestellt wurden, haben dieselben physikalischen Eigenschaften und Genauigkeiten wie Teile, die mit Werkzeugstahlformen in „Großserienfertigung“ hergestellt wurden.
Schritt 3: Produktionssteigerung (über 100.000 Teile)

Wenn Teile in großen Mengen von identischen Teilen hergestellt werden (von 10.000 bis über 100.000 Stück), sind spezielle Spritzgusswerkzeuge erforderlich.
Für diese Volumina werden die Formen aus Werkzeugstahl CNC-gefräst und halten Millionen von Spritzgusszyklen stand. Sie sind außerdem mit fortschrittlichen Funktionen ausgestattet, um die Produktionsgeschwindigkeit zu maximieren, z. B. Hot-Tip-Gates, also beheizte Angusskanäle, und komplizierte Kühlkanäle.
Die typischen Stückkosten variieren zu diesem Zeitpunkt zwischen einigen Cent und 1 USD, und die typische Vorlaufzeit beträgt 4 bis 6 Monate, da die Entwicklung und Herstellung der Form komplex ist.
Part 6
Hilfreiche Ressourcen:
In diesem Führer haben wir alles angesprochen, was Sie für den Einstieg in das Spritzgießen benötigen. Es gibt jedoch noch viel mehr zu lernen.
Im Folgenden finden Sie die besten und nützlichsten Ressourcen zum Spritzgießen und zu anderen digitalen Fertigungstechnologien für diejenigen, die sich eingehender mit dem Thema befassen möchten.
Protolabs Network Wissensbasis
Hier haben wir alles angesprochen, was Sie für den Einstieg in das Spritzgießen benötigen. In unserer Wissensbasis gibt es noch viel mehr zu erfahren - eine Sammlung technischer Artikel zu allen Fertigungstechnologien, die von Experten von Protolabs Network und der Fertigungsindustrie verfasst wurden.
Hier finden Sie eine Auswahl unserer beliebtesten Artikel zum Thema Spritzguss:
Andere Leitfäden
Möchten Sie mehr über die digitale Fertigung erfahren? Es gibt noch mehr Technologien zu erforschen: