Additieve technologieën vergeleken
Metaal 3D-Printen

Klaar om uw onderdelen te laten printen?
Ontvang direct een offerte voor 3D-printen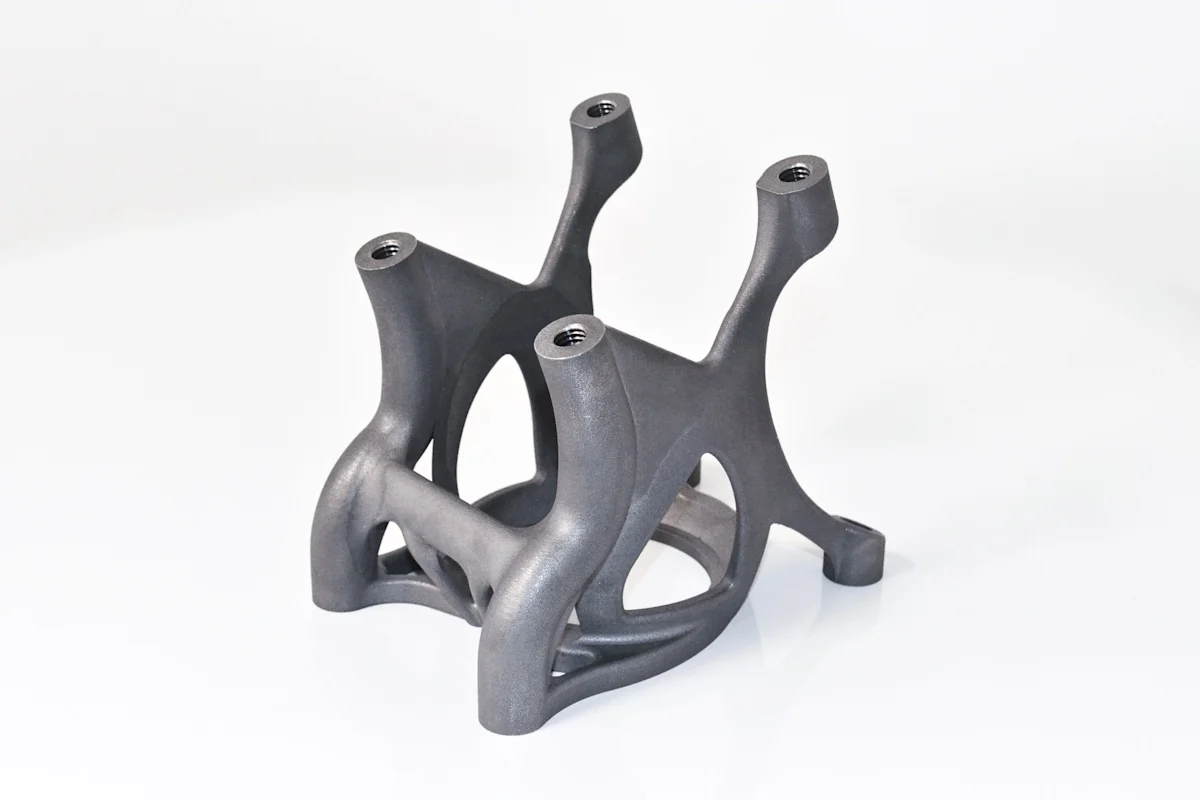
3D printen met metaal is in opkomst. In deze handleiding lees je hoe je deze techniek optimaal gebruikt. Met een compleet overzicht van de huidige stand van zaken, de unieke voordelen van 3D printen met metaal (maar ook de beperkingen) en hoe je de drie populairste vormen van 3D printen met metaal gebruikt: DMLS/SLM, binder jetting en metaalextrusie. Wil je 3D geprinte onderdelen in metaal? Check dan wat Protolabs je kan bieden.
Part 1
De Basisprincipes
Hoe werken metaal 3D-printers? Wat zijn de belangrijkste voordelen en beperkingen? Hoe gebruikt de industrie 3D-printen met metaal momenteel?
In dit deel geven we antwoord op deze vragen en komen we meer te weten over de basismechanica van de verschillende 3D-printprocessen voor metaal. Op basis van een vergelijking met “traditionele” productie, krijgt u meer inzicht in de huidige stand van zaken van 3D-printen met metaal en het grote potentieel dat het heeft.
Hoe werken 3D-printers voor metaal?
Vergelijkbaar met alle andere 3D-printprocessen, 3D-printers voor metaal bouwen onderdelen door materiaal laag-voor-laag toe te voegen op basis van een digitaal 3D-ontwerp - vandaar de alternatieve benaming Additive Manufacturing.
Zo kunnen onderdelen worden gebouwd met geometrieën die niet kunnen worden geproduceerd door “traditionele” subtractieve (CNC-frezen) of formatieve (Spuitgieten) technologieën, en zonder de noodzaak van speciale tooling (zoals een matrijs).
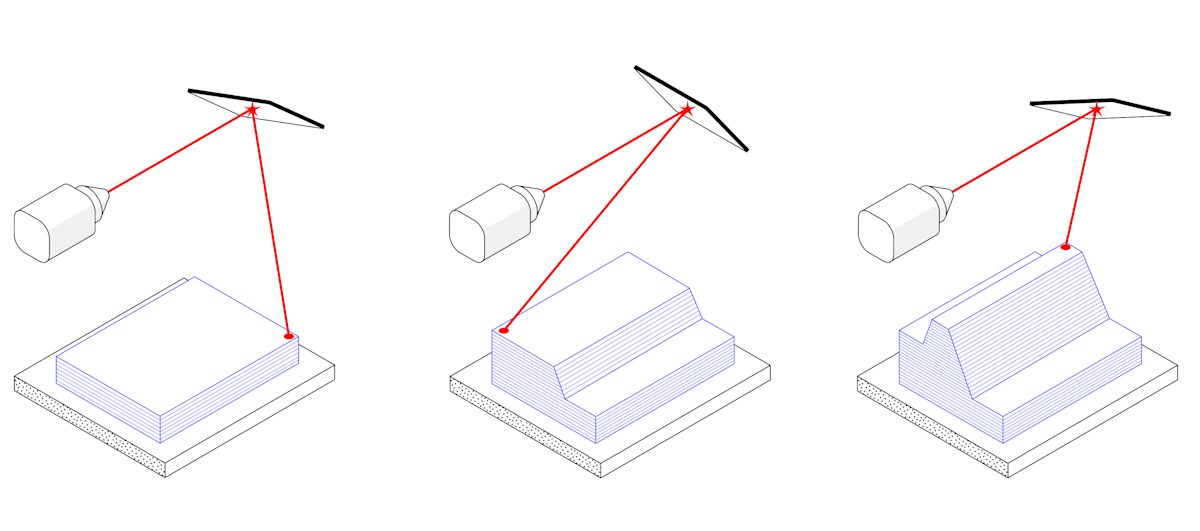
Vanaf hier zijn er aanzienlijke verschillen in de specifieke stappen die elk type 3D-printer voor metaal volgt om een onderdeel te produceren:
Powder Bed Fusion
Een krachtige laser (bij DMLS/SLM) of een elektronenstraal (bij EBM) wordt gebruikt om metaalpoederdeeltjes selectief, laag-voor-laag, aan elkaar te binden, zodat een metalen onderdeel wordt gevormd.
Producenten: EOS, 3D Systems, Renishaw, SLM Solutions, Concept Laser, Arcam
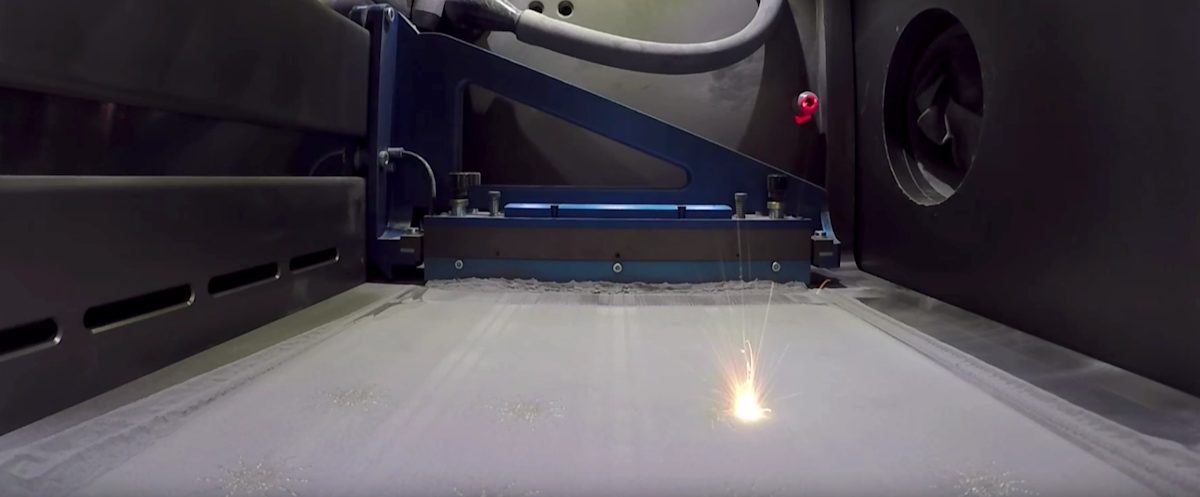
Binder Jetting
Metaalpoederdeeltjes worden laag-voor-laag verlijmd met een bindmiddel, waardoor een “groen” onderdeel gevormd wordt dat thermisch moet worden nabewerkt (gesinterd) om het bindmiddel te verwijderen en een volledig metalen onderdeel te creëren.
Producenten: Desktop Metal, ExOne, Digital Metal, HP
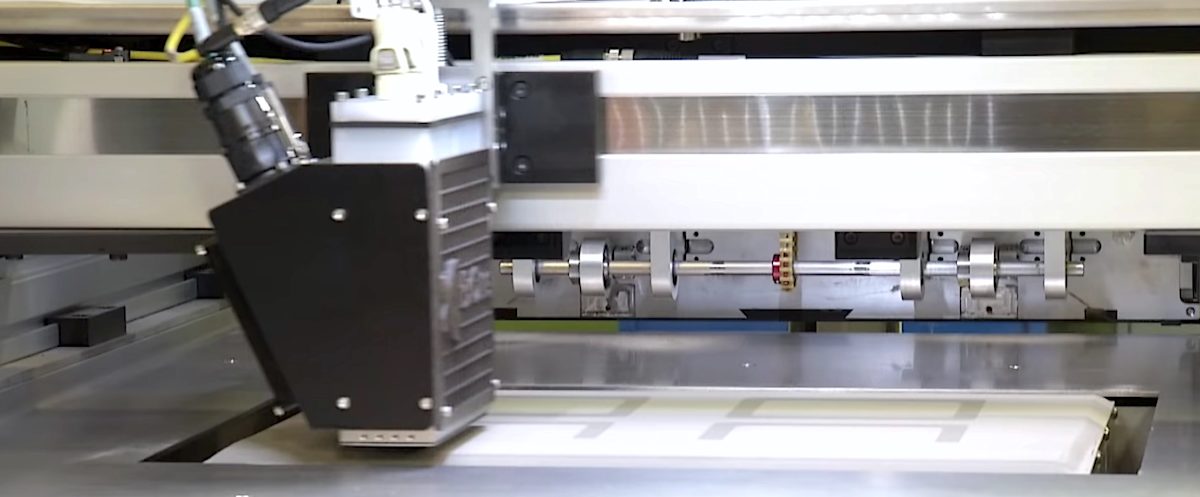
Metal Material Extrusion
Een filament of staaf, gemaakt van polymeer en zwaar beladen met metaalpoeder, wordt geëxtrudeerd via een sproeistuk (zoals bij FDM) om het “groene” onderdeel te vormen dat wordt nabewerkt (ontdaan van bindmiddel en gesinterd) om een volledig metalen onderdeel te creëren.
Producenten: Desktop Metal, Markforged
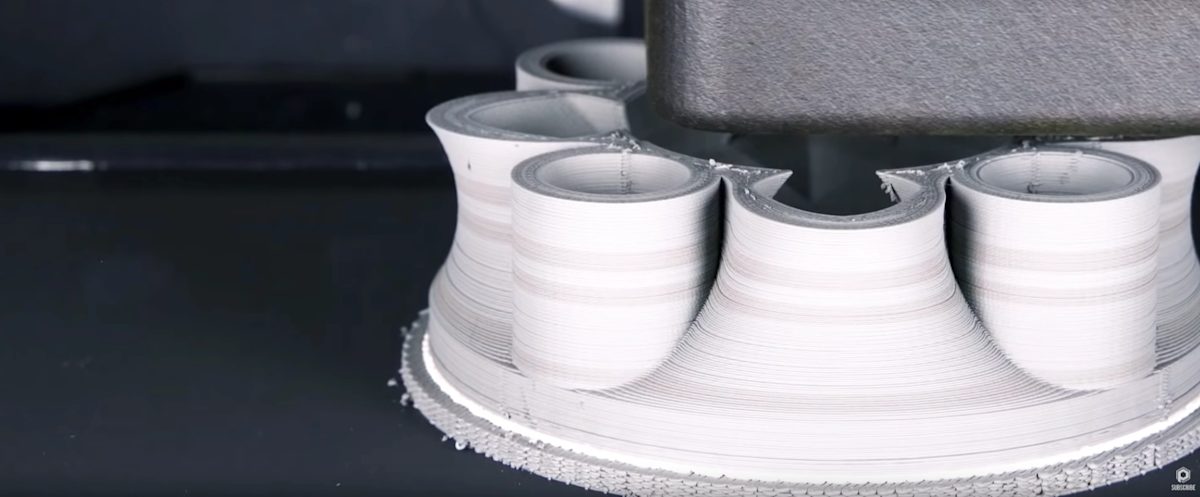
Ultrasonic Additive Manufacturing
Metaalfolies worden laag-voor-laag gebonden middels ultrasonisch lassen en vervolgens met CNC-frezen bewerkt tot de ontwerpvorm.
Producenten: Fabrisonic
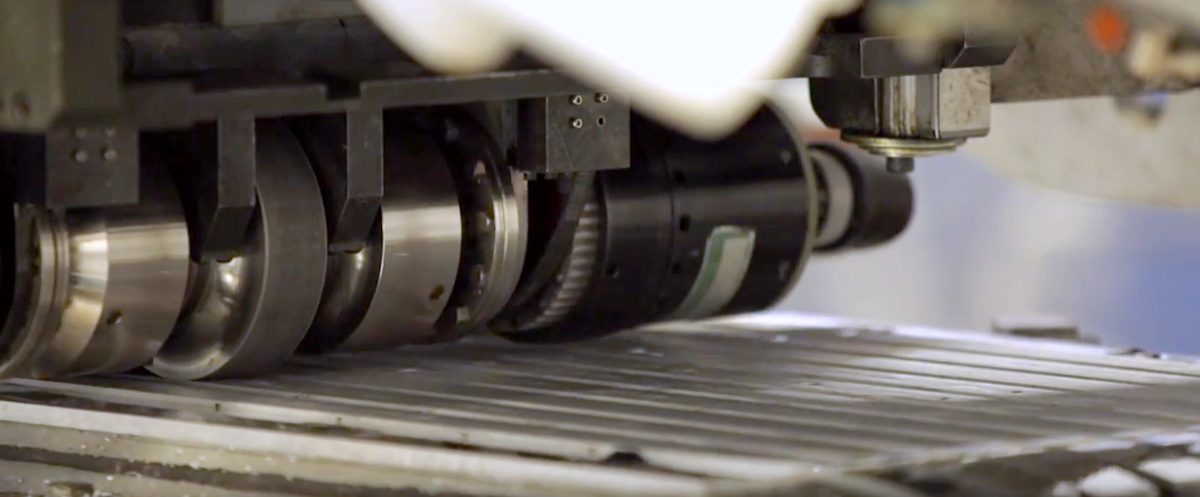
Andere processen
Door de jaren heen zijn, op basis van gevestigde 3D-printtechnologieën voor kunststof (zoals Material Jetting en SLA), andere 3D-printsystemen voor metaal ontwikkeld.
3D-printen wordt ook gebruikt om tooling to creëren voor “traditionele metaalproductie, zoals zandgieten of verlorenwasgieten.
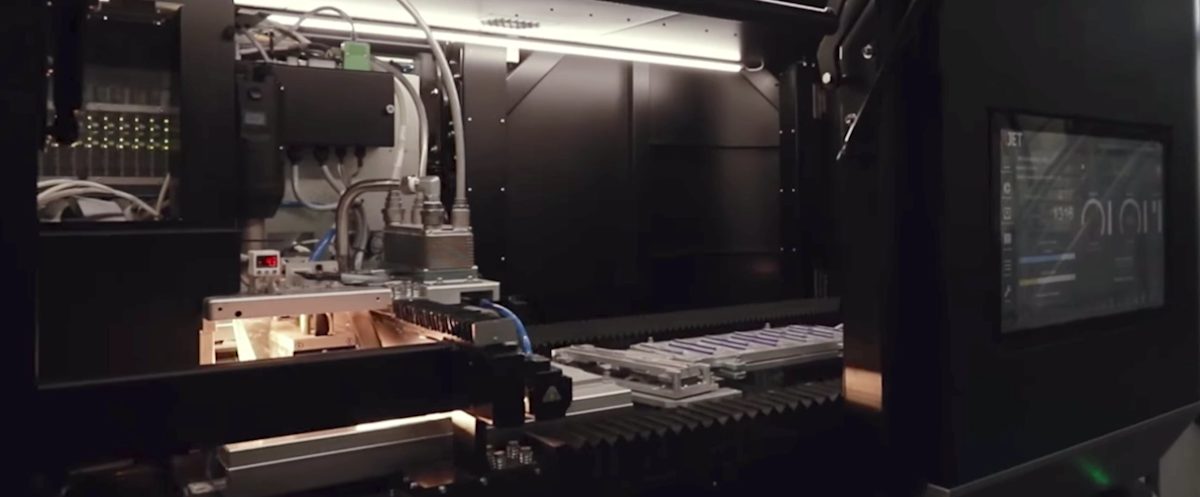
Vandaag de dag zijn de meestgebruikte 3D-printprocessen voor metaal Direct Metal Laser Sintering (DMLS) / Selective Laser Melting (SLM), gevolgd door Binder Jetting en Metal Extrusion.
Als u dieper wilt ingaan op de basismechanica en/of specifieke voordelen, beperkingen en capaciteiten van elk van deze technologieën, ga dan direct door naar het volgende deel van deze handleiding.
In het restant van dit deel zullen we ons richten op de algemene aspecten van 3D-printen met metaal, die op alle processen van toepassing zijn. Ook zullen we kijken hoe deze in verhouding staan tot “traditionele” productieprocessen. Zo ontwikkeld u een breder inzicht in hoe u het meeste uit deze unieke productietechnologie kunt halen. Maar eerst en korte geschiedenisles…
Een beknopte geschiedenis van 3D-printen met metaal
- Eind jaren ’80 ontwikkelde Dr. Carl Deckard van de University of Texas de eerste laser-sinter 3D-printer voor kunststoffen. Deze uitvinden was het begin van de weg naar 3D-printen met metaal.
- Het eerste voor patent voor het lasersmelten van metalen werd in 1995 ingediend door het Fraunhofer Instituut in Duitsland. Bedrijven als EOS en veel universiteiten zijn de voornaamste ontwikkelaars van dit proces.
- In 1991 introduceerde Dr. Ely Sachs van MIT een 3D-printproces dat we vandaag de dag kennen als Binder Jetting. Vervolgens werd, in 1995, een licentie voor Binder Jetting van metaal toegekend aan ExOne.
- 3D-printen met metaal maakt sinds het begin van de 21e eeuw een langzame maar gestage groei door. Dit is na 2012 veranderd, toen de oorspronkelijke patenten begonnen te verlopen en door bedrijven als GE, HP en DM grote investeringen zijn gedaan.
- Het Wohler’s rapport schat dat de snel groeiende markt van 3D-printen met metaal vandaag de dag goed is voor zo’n $720 miljoen. Alleen al in 2017 steeg de verkoop van 3D-printers voor metaal met 80%.

Voordelen & beperkingen van 3D-printen met metaal
Het is belangrijk om te begrijpen dat 3D-printen met metaal een krachtig instrument is dat veel unieke voordelen biedt. Echter maken de huidige beperkingen dat het niet altijd de beste optie is als het aankomt op het produceren van metalen onderdelen.
Hier volgt een samenvatting van de belangrijkste voor- en nadelen van 3D-printen met metaal. Gebruik deze voor een inzicht in hoe 3D-printen met metaal er momenteel voor staat en welke richting het op gaat in de nabije toekomst.
Voordelen van 3D-printen met metaal
Het grootste voordeel van 3D-printen met metaal, vergeleken met “traditionele” productie, is de uitzonderlijke ontwerpflexibiliteit. Omdat er geen specifieke tooling vereist is (zoals een matrijs of snijgereedschap), kunnen geometrieën die in andere processen onmogelijk zijn, eenvoudig 3D-geprint worden.
Belangrijker nog, het verhogen van de geometrische complexiteit van een onderdeel heeft vrijwel geen effect op de productiekosten ervan. Dit betekent dat organische, topologisch geoptimaliseerde constructies kunnen worden gebruikt bij 3D-printen met metaal, waardoor de prestaties van de geproduceerde onderdelen aanzienlijk kan worden verbeterd.
De grote ontwerpflexibiliteit van 3D-printen met metaal gaat hand-in-hand met de creatie van lichtgewicht constructies. Sterker nog, het volgen van de beste ontwerppraktijken voor 3D-printen met metaal levert altijd een lichtgewicht oplossing op.
Normaliter wordt voor dit doel gebruik gemaakt van geavanceerde CAD-technieken, zoals topologische optimalisatie en generatief ontwerp.
Dit resulteert in onderdelen met zowel minder gewicht (doorgaans 25% tot 50% minder) en hogere rigiditeit. Dit is zeer belangrijk voor hoogwaardige industriële toepassingen zoals lucht- en ruimtevaart.
Omdat toegang van het gereedschap geen probleem is bij 3D-printen met metaal, kunnen onderdelen met interne structuren worden geproduceerd.
Interne kanalen voor gelijkmatige koeling, bijvoorbeeld, zijn een uitstekende manier om de prestaties van een onderdeel te verbeteren. Spuitgietkernen met gelijkmatige koeling - geproduceerd middels DMLS/SLM - kunnen de injectiecyclusduur tot wel 70% verminderen.
Nog een voorbeeld van verbeterde onderdeelfunctionaliteit is afkomstig uit Metal Extrusion. Met dit proces kunnen aangepaste mallen en armaturen met complexe geometrieën op aanvraag worden gecreëerd, wat leidt tot hogere efficiëntie van de operaties in andere industriële processen op de productievloer.
Nog een grote kracht van 3D-printen met metaal is de mogelijkheid om een assemblage samen te voegen tot één geheel.
Hierdoor zijn geen bevestigingsmiddelen vereist, wat resulteert in onderdelen die tegelijkertijd meerdere functies kunnen vervullen. Bovendien worden de arbeidskosten en levertijden geminimaliseerd en de onderhouds- en servicevereisten verminderd.
Bijkomend voordeel is dat de verminderen van het totaal aantal onderdelen nog een methode is om lichtgewicht constructies te creëren.
Zelfs als een onderdeel met complexe geometrie kán worden geproduceerd via “traditionele” methoden, kunnen daar zomaar 20 of meer productiestappen voor nodig zijn.
In die gevallen zou 3D-printen moeten worden overwogen als een reële productieoptie. Met Binder Jetting, bijvoorbeeld, kan het totaal aantal stappen worden teruggebracht tot vijf of minder (inclusief nabewerking en afwerking). Zo kan de complexiteit van de toeleveringsketen voor productie aanzienlijk worden verminderd.
In tegenstelling tot 3D-printen met kunststoffen, vertonen onderdelen die middels DMLS/SLM of Binder Jetting zijn geproduceerd anisotroop mechanisch gedrag. Ook is hun materiaalsterkte vergelijkbaar met smeedmetaal (en in sommige gevallen zelfs beter). Om die reden zijn voor 3D-geprinte metalen onderdelen toepassingen gevonden in de meest veeleisende industrieën, zoals de luchtvaart.
Let er echter op dat 3D-geprinte onderdelen doorgaans minder moeheidsweerstand hebben. Dit komt door hun oppervlakteruwheid en interne porositeit (doorgaans hebben DMSL-/SLM-onderdelen < 0,2% porositeit en Binder Jetting-onderdelen < 2%).
Beperkingen van 3D-printen met metaal
Vergeleken met traditionele productiemethoden, zijn de kosten voor 3D-printen met metaal momenteel (nog) aanzienlijk hoger. Gemiddeld zal een typisch DMLS/SLM-onderdeel u ongeveer $5.000 tot $10.000 kosten om te 3D-printen en af te werken. Het is dus belangrijk om te onthouden dat het gebruik van 3D-printen met metaal economisch verantwoord is als het een aanzienlijke verbetering in de prestaties oplevert.
Er is echter wel vraag naar betaalbare 3D-printoplossingen met metaal. De nieuwe Metal Extrusion-systemen die op de werkbank passen en Binder Jetting-productiesystemen zouden dit gat in de markt in de nabije toekomst kunnen gaan invullen.
Nog een beperking van 3D-printen met metaal is dat het nog niet kan concurreren met traditionele productie als het om grotere aantallen gaat.
Het gebrek aan aangepaste tooling betekent dat de opstartkosten laag zijn, maar ook dat de totale productiekosten niet aanzienlijk beïnvloed worden door de productieaantallen. Met andere woorden, de stuksprijs blijft bij grotere aantallen vrijwel onveranderd en er is geen schaalvoordeel te behalen.
De industrie werkt echter toe naar 3D-printsystemen die de productie kunnen stroomlijnen. Zo maken, bijvoorbeeld, DMLS-/SLM-machines met meerdere lasers en Binder Jetting-systemen met doorlopende productiecapaciteit momenteel hun intrede in de markt.
Onderdelen ontwerpen voor 3D-printen met metaal is onderhevig aan een andere set regels dan “traditionele” productie. Vaak betekent dit dat bestaande ontwerpen opnieuw moeten worden ontworpen.
Bovendien kan het zijn dat de instrumenten die oudere CAD-software aanbiedt niet volstaan om de voordelen van 3D-printen met metaal ten volste te benutten. Raadpleeg het laatste deel van deze handleiding voor een uitgebreide introductie van de voornaamste ontwerpoverweging, geavanceerde CAD-tools en ontwerpregels voor 3D-printen met metaal.
Vrijwel elk 3D-geprint metalen onderdeel zal enige vorm van nabewerking vereisen voordat het klaar is voor gebruik. Dit draagt bij aan de totale kosten en de levertijd.
Combinaties van thermische behandelingen, frezen, polijsten en andere afwerkingsmethoden zijn, ongeacht de gekozen technologie, vrijwel altijd vereist om het eindproduct te produceren. In latere delen volgen meer details over de benodigde nabewerkingsstappen voor de verschillende technologieën.
Toepassingen van 3D-printen met metaal
Hier hebben we een aantal voorbeelden verzameld van de belangrijkste industriële toepassingen van 3D-printen met metaal. Deze illustreren een aantal van de voornaamste voordelen en beperkingen van de technologie. Gebruik ze om beter te begrijpen waarom ingenieurs 3D-printen met metaal kiezen voor hun specifieke toepassing.
Materialen voor 3D-printen met metaal
Het aantal metaalmaterialen dat voor 3D-printen kan worden gebruikt neemt snel toe. Ingenieurs kunnen vandaag de dag kiezen uit o.a. de volgende legeringen:
- RVS
- Gereedschapsstaal
- Titaniumlegeringen
- Aluminiumlegeringen
- Superlegeringen op basis van nikkel
- Kobaltchroomlegeringen
- Legeringen op basis van koper
- Edelmetalen (goud, zilver, platina…)
- Exotische metalen (palladium, tantaal…)
De kosten van 3D-printen met metaal
De kosten van een 3D-printer voor metaal variëren aanzienlijke, afhankelijk van de technologie. De gemiddelde verkoopprijs voor een DMLS-/SLM-printer is zo’n $550.000 en kan oplopen tot $2 miljoen USD. Metal Binder Jetting-systemen kosten ongeveer $400.000. Voor een Metal Extrusion-printer bent u rond de $140.000 kwijt, inclusief apparatuur voor de nabewerking.
De productiekosten van een typisch DMLS/SLM-onderdeel bedragen ongeveer $5.000-$10.000 (inclusief afwerking). Voor Binder Jetting en Metal Extrusion kunnen de kosten per onderdeel tot 5 á 10 keer lager uitvallen dan voor DMLS-/SLM-onderdelen. Op het moment van schrijven is het echter nog te vroeg om de volledige operationele kosten voor deze systemen te beoordelen.
Onderstaande tabel zet de gemiddelde kosten van de verschillende productiestappen voor DMLS/SLM uiteen. Kijk vooral naar de aanzienlijke bijdrage van de materiaalkosten en de nabewerkingskosten in de totale kosten.
Productiestap | Handeling | Kosten |
---|---|---|
Productie | Materiaalkosten | $200 - $500 per kilo |
DMLS-/SLM-kosten | $2,000 - $4,000 per productie † | |
Nabewerking | Spanningsontlasting | $500 - $600 per productie † |
Verwijderen van onderdeel/ondersteuningen | $100 - $200 per onderdeel | |
Thermische behandeling / HIP | $500 - $2,000 per productie † | |
CNC-frezen | $500 - $2,000 per onderdeel | |
Oppervlaktebehandeling | $200 - $500 per onderdeel |
† Doorgaans passen er zes tot twaalf onderdelen op dezelfde bouwplaat.
De snelheid van 3D-printen met metaal
Los van het proces, vereist de productie en afwerking van een 3D-geprint onderdeel tenminste 48 uur en gemiddeld 5 dagen.
Het printen zelf neemt ongeveer 50% van de totale productietijd in beslag. Dit is natuurlijk afhankelijk van het volume van het onderdeel en of er ondersteuningsconstructies nodig zijn. Ter referentie, de huidige productiesnelheid van een moderne 3D-printsysteem voor metaal ligt tussen de 10-40 cm³/uur.
De resterende productietijd houdt verband met nabewerking en afwerkingseisen. Thermische behandelingen dragen aanzienlijk bij aan de totale productietijd: een typische thermische cyclus duurt zo’n 10 tot 12 uur. Mechanische oppervlakteafwerking kan ook een tijdrovende stap zijn als er input van een expert (5-assig CNC-frezen) of handmatig werk (met de hand polijsten) bij komt kijken.
3D-printen met metaal vs traditionele productie
Begin altijd met een Kosten-batenanalyse , als u de keuze maakt tussen 3D-printen met metaal en een subtractieve (CNC-frezen) of formatieve (metaalgieten) technologie.
In het algemeen houden de productiekosten voornamelijk verband met het productievolume, terwijl de prestaties van een onderdeel sterk afhankelijk zijn van de geometrie ervan.
De voornaamste kracht van 3D-printen met metaal is de capaciteit om onderdelen te creëren met complexe & geoptimaliseerde geometrieën. Dit betekent dat het ideaal is voor het produceren van hoogwaardige onderdelen. Anderzijds biedt het voor grotere aantallen niet de schaalvoordelen die te behalen zijn bij CNC-frezen of metaalgieten.

Als vuistregel:
De hoge kosten van metaal 3D-printen zijn alleen financieel verantwoord als het verband houdt met een aanzienlijke verbetering van de prestaties of operationele efficiëntie.
Uiteraard voorziet elk 3D-printproces met metaal in andere industriële behoeften en eisen. Gebruik onderstaande tips als algemene richtlijnen om te begrijpen welk proces voor u het meest geschikt is:
- DMLS/SLM is de beste oplossing voor onderdelen met hoge geometrische complexiteit (organische, topologisch geoptimaliseerde constructies) die uitstekende materiaaleigenschappen vereisen om de efficiëntie van de meest veeleisende toepassingen te verhogen.
- Binder Jetting is de beste oplossing voor de productie van kleine tot middelgrote aantallen, waarvoor de grote economische investering van een formatieve methode niet kan worden verantwoord en voor onderdelen met geometrieën die niet efficiënt kunnen worden geproduceerd met een subtractieve methode.
- Metal Extrusion is de beste oplossing voor prototypes van metaal en losse onderdelen met geometrieën die anders met een 5-assige CNC-machine zouden moeten worden geproduceerd.
De onderstaande tabel is een matrix die de Complexiteit van het onderdeel afzet tegen het volume , waarin kan worden afgelezen in welk segment de verschillende productieprocessen (additief, subtractief of formatief) het beste presteren. Gebruik deze als snelle verwijzing:
Kwantiteit | Lage complexiteit | Gemiddelde complexiteit | Hoge complexiteit |
---|---|---|---|
< 10 onderdelen | CNC-frezen | Metal extrusion CNC-frezen |
DMLS/SLM |
< 100 onderdelen | CNC-frezen | Binder Jetting CNC-frezen |
Binder Jetting DMLS/SLM |
< 1,000 onderdelen | CNC-frezen Metaalgieten |
Binder Jetting CNC-frezen |
Binder Jetting |
1,000+ onderdelen | Plaatstaal Metaalgieten |
Metaalgieten | - |
Part 2
DMLS & SLM
Direct Metal Laser Sintering (DMLS) en Selective Laser Melting (SLM) zijn momenteel de meest gebruikte 3D-printprocessen voor metaal. Ze zijn vooral geschikt voor hoogwaardige toepassingen, omdat ze uitstekende ontwerpvrijheid & geavanceerde materiaaleigenschappen bieden.
In dit deel gaan we dieper in op het productieproces, de technische eigenschappen en de voordelen en beperkingen van deze twee, heel vergelijkbare, processen.
Wat is DMLS/SLM 3D-printen?
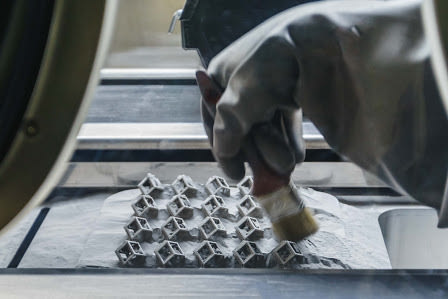
DMLS (Direct Metal Laser Sintering) of SLM (Selective Laser Melting) zijn twee 3D-printtechnologieën voor metaal die werken op basis van poederbed versmelting (Powder Bed Fusion). Het praktische verschil tussen SLM en DMLS is erg klein. Voor ontwerpdoeleinden zijn de twee technologieën hetzelfde.
Ze maken beide gebruik van een krachtige laser om metaalpoederdeeltjes te binden om laag-voor-laag een onderdeel te vormen. Bij SLM wordt volledig gesmolten, terwijl DMLS de metaaldeeltjes op moleculair niveau laat versmelten door de zeer hoge temperaturen. De meeste metaallegeringen kunnen in het DMLS-proces worden gebruikt, terwijl slechts bepaalde (pure) metalen kunnen worden gebruikt voor SLM.
Hoe werkt DMLS/SLM?
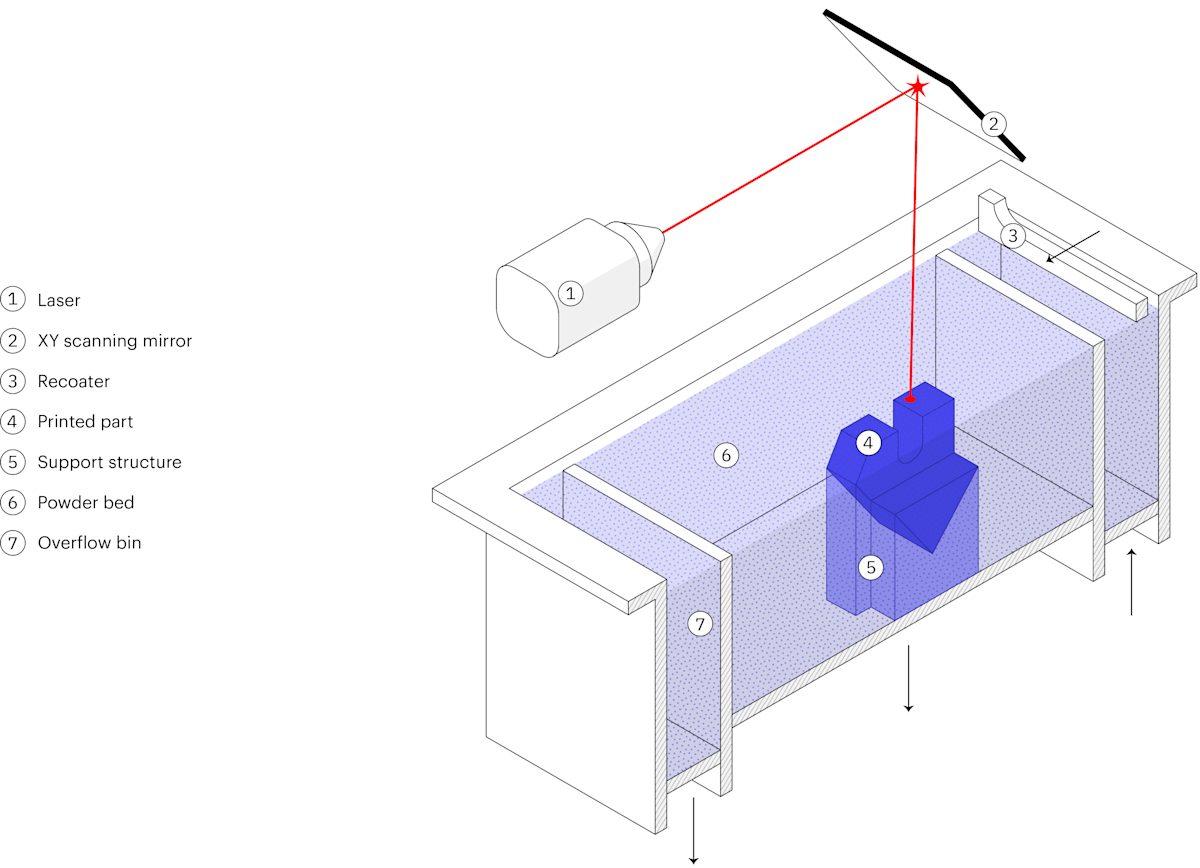
Hier volgen de basisstappen voor het DMLS/SLM 3D-printproces:
- De bouwkamer wordt eerst gevuld met inert gas en verwarmd tot de optimale printtemperatuur.
- Een dun laagje metaalpoeder (normaliter 50 μm) wordt over het bouwplatform verspreid.
- De laser scant de doorsnede van het onderdeel waarbij de metaaldeeltjes selectief worden gebonden.
- Als een stuk volledig gescand is, verplaatst het bouwplatform een laagje omlaag waarna dit proces zich herhaalt tot de bouw helemaal klaar is.
- Na het printen, moet de bouw eerst afkoelen en daarna wordt het losse poeder verwijderd.
De 3D-printstap is slechts het begin van het DMLS-/SLM-productieproces. Nadat de print klaar is, zijn meerdere (vereiste of optionele) nabewerkingsstappen vereist voordat het onderdeel klaar is voor gebruik. Vereiste nabewerkingsstappen zijn, o.a.:
- Spanningsontlasting: Door de zeer hoge verwerkingstemperaturen tijdens het printen, kunnen interne spanningen ontstaan. Deze moeten worden ontlast middels een thermische cyclus voordat andere verwerking of behandeling plaatsvind.
- Verwijdering van de onderdelen: Bij DMLS/SLM worden de onderdelen in feite op het bouwplatform gelast. Hier wordt een lintzaag of EDM-draadvonken op toegepast.
- Verwijdering van de ondersteuning: Ondersteuning is bij DMLS/SLM altijd vereist om de vervorming en verdraaiing tegen te gaan die zich tijdens het printen voordoet. Ondersteuning wordt handmatig of middels CNC-frezen verwijderd.
Om aan de technische specificaties te voldoen, zijn er vaak aanvullende nabewerkingsstappen vereist. Dit kan o.a. zijn:
- CNC-frezen: Als kleinere toleranties dan de standaard ± 0,1 mm vereist zijn, wordt frezen toegepast als afwerkingsstap. Deze methode verwijderd slechts minimale hoeveelheden materiaal.
- Thermische behandelingen: Om de materiaaleigenschappen van het onderdeel te verbeteren, kan thermische behandeling of Heet Isostatisch Persen (HIP) worden toegepast.
- Afvlakking/Polijsten: Bepaalde toepassingen vereisen een gladder oppervlak dan de standaard RA 10 μm van onderdelen rechtstreeks uit het DMLS-/SLM-printproces. CNC-frezen en handmatig, vibro- of chemisch polijsten zijn allen mogelijke oplossingen.
Metaalpoeders voor 3D-printen
Het ruwe materiaal dat bij DMSL/SLM en veel andere 3D-printprocessen wordt gebruikt, wordt in poedervorm aangeleverd.
De eigenschappen van de metaalpoeders zijn van groot belang voor het eindresultaat. Om een goede doorstroming en dichtheid te garanderen, moeten de metaaldeeltjes bolvormig zijn, en tussen de 15 en 45 microns groot. Om aan deze strenge eisen te voldoen, wordt veelal gebruik gemaakt van methoden zoals gas- of plasmaverstuiving.
De hoge kosten van het produceren van deze metaalpoeders is een belangrijke factor in de totale kosten voor 3D-printen met metaal.

Voordelen en beperkingen van DMLS/SLM
De voornaamste kracht van DMLS/SLM is de capaciteit om sterk geoptimaliseerde organische constructies van hoogwaardige metaallegeringen te produceren.
Onderdelen die met DMLS/SLM worden geproduceerd kunnen complexe, organische vormen hebben die geoptimaliseerd zijn voor minimaal gewicht in combinatie met maximale rigiditeit. Of ze kunnen interne geometrieën hebben die met geen enkele andere methode kunnen worden geproduceerd.
De materiaaleigenschappen van DMLS-/SLM-onderdelen zijn uitstekend. Onderdelen met vrijwel geen interne porositeit worden geproduceerd uit een breed assortiment metaallegeringen, van aluminium en staal tot de sterkste superlegeringen.
In een vorig deel zagen we echter dat de kosten in verband met DMLS/SLM hoog zijn. Om die reden is het alleen economisch verantwoord om deze processen te gebruiken voor geoptimaliseerde onderdelen voor hoogwaardige technische toepassingen.
Vanuit technisch oogpunt is de voornaamste beperking van DMLS en SLM de noodzaak om uitgebreide ondersteuningsconstructies toe te passen. Deze zijn nodig om vervorming te voorkomen en om het onderdeel op het bouwplatform te verankeren. Ook is de oppervlakteruwheid van de geproduceerde onderdelen, op het moment dat ze uit de printer komen, relatief hoog voor de meeste technische toepassingen, dus nabewerking is vereist.
Technische eigenschappen van SLM & DMLS
Onderstaande tabel toont de technische basiscapaciteiten van een gemiddelde hedendaagse DMLS/SLM 3D-printer voor metaal. Meer ontwerprichtlijnen vindt u onder de ontwerpregels.
Eigenschap | DMLS/SLM |
---|---|
Materiaalkeuze | Groot assortiment van materialen direct beschikbaar Aluminium of kobaltchrome legeringen, titanium, RVS, gereedschapsstaal, nikkel superlegeringen, edelmetalen, enz. |
Dimensionale nauwkeurigheid | ± 0,1 mm |
Gebruikelijk bouwformaat | 250 x 150 x 150 mm (tot 500 x 280 x 360 mm) |
Gebruikelijke laagdikte | 20 - 50 μm |
Gebruikelijke oppervlakteruwheid | RA 8 - 10 μm |
Ondersteuning | Altijd vereist |
Interne porositeit | Minder dan 0,2 - 0,5% |
Kosten per onderdeel | $$$$$ |
Part 3
Metal Binder Jetting
Metal Binder Jetting neemt snel in populariteit toe. De unieke eigenschappen ervan, maken het bijzonder geschikt voor de productie van kleine tot middelgrote aantallen.
In dit deel gaan we dieper in op de stappen die bij Binder Jetting worden gevolgd en de basiseigenschappen van de geproduceerde metalen onderdelen.
Wat is Metal Binder Jetting?
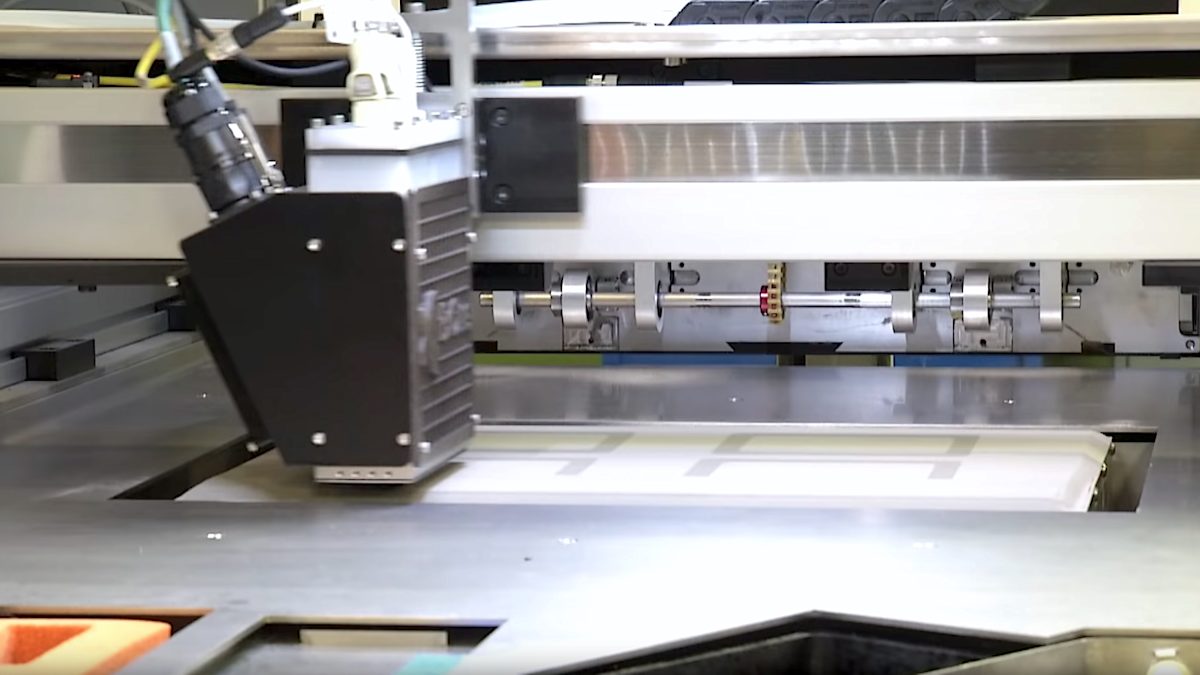
Binder Jetting bouwt onderdelen door via inkjet-sproeistukken een bindmiddel te deponeren op een dun laagje poeder. Het werd oorspronkelijk gebruikt om volledig gekleurde prototypes en modellen van zandsteen te creëren. Een variatie op het proces neemt momenteel toe in populariteit omdat het batch-productiecapaciteiten biedt.
De printstap bij Metal Binder Jetting-printen vindt plaats bij kamertemperatuur. Dit betekent dat thermische effecten (zoals vervorming en interne spanningen) geen probleem zijn, zoals bij DMLS/SLM, en dat er geen ondersteuningen nodig zijn. Een extra nabewerkingsstap is vereist om een volledig metalen onderdeel te creëren.
Hoe werkt Metal Binder Jetting?
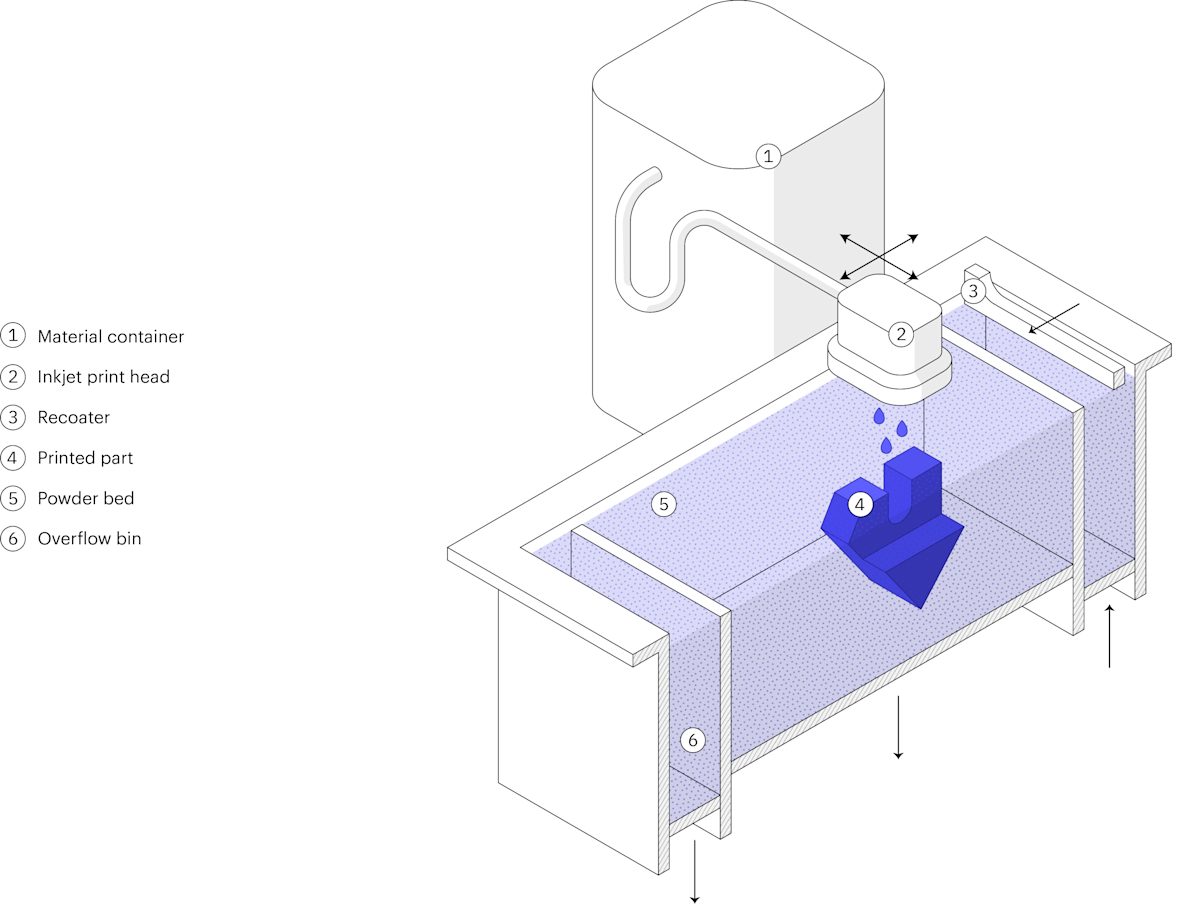
Metal Binder Jetting is een proces met twee stappen. Het heeft een printstap en een essentiële nabewerkingsstap. Dit is hoe het printproces in zijn werk gaan:
- Een dun laagje metaalpoeder (normaliter 50 μm) wordt over het bouwplatform verspreid.
- Een kar met inkjet-sproeistukken beweegt zich over het bed en deponeert selectief druppels bindmiddel (polymeer en was) om de metaalpoederdeeltjes te binden.
- Als er een laag af is, verplaatst het bouwplatform omlaag waarna dit proces zich herhaalt tot de bouw helemaal klaar is.
Het resultaat van het printproces is een onderdeel in de zogenaamde “groene” staat. Een nabewerkingsstap is vereist om het bindmiddel te verwijderen en volledig metalen onderdelen te creëren.
Er zijn twee varianten voor deze nabewerkingsstap:
- Infiltratie: Het “groene” onderdeel wordt eerst gewassen om het bindmiddel te verwijderen, waardoor het “bruine” onderdeel ontstaat dat aanzienlijke interne porositeit heeft (~70%). Het “bruine” onderdeel wordt vervolgens verhit in een industriële oven, in het bijzijn van een metaal met een laag smeltpunt (normaliter brons). De interne leemten worden gevuld, met een bimetalen onderdeel als resultaat.
- Sinteren: Het “groene” onderdeel wordt in een industriële oven geplaatst. Daar wordt eerst het bindmiddel weggebrand en vervolgens worden de resterende metaaldeeltjes aan elkaar gesinterd. Het resultaat is een volledig metalen onderdeel met ongeveer 20% kleinere afmetingen dan het oorspronkelijke “groene” onderdeel. Het onderdeel wordt groter geprint om dit te compenseren.
Vandaag de dag wordt sinteren in het merendeel van de toepassingen gebruikt, omdat infiltratie onderdelen creëert met inferieure materiaaleigenschappen en slecht gedocumenteerd mechanisch en thermisch gedrag.
Binder Jetting & Spuitgieten met metaal (Metal Injection Molding, MIM)
Na het sinteren, hebben Binder Jetting-onderdelen zeer vergelijkbare eigenschapen als die van onderdelen die middels MIM zijn geproduceerd. MIM is een productieproces dat wordt gebruikt voor de massaproductie van vrijwel elk klein metalen onderdeel dat is terug te vinden in hedendaagse consumentenelektronica en auto’s.
MIM is een variant op het spuitgietproces met kunststof. Metaalpoeder, vermengd met een kunststof bindmiddel, wordt in een matrijs geïnjecteerd om het “groene” onderdeel te vormen, dat vervolgens wordt gesinterd om metaal te worden.
Metal Binder Jetting bouwt dus voort op de praktische kennis van het MIM-proces.
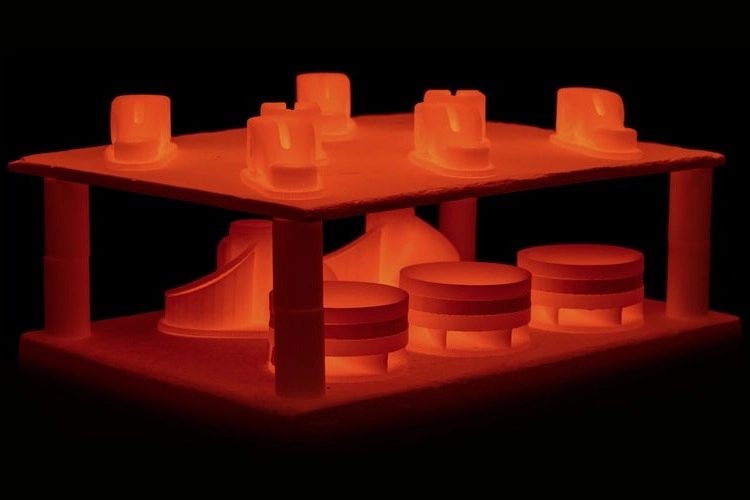
Voordelen en beperkingen van Metal Binder Jetting
Binder Jetting is op dit moment de enige 3D-printtechnologie die kosteneffectief kan worden ingezet voor de productie van kleine tot middelgrote aantallen metalen onderdelen.
Omdat er geen ondersteuningsconstructies vereist zijn voor het printen, kunnen Binder Jetting-systemen hun hele bouwruimte benutten. Hierdoor kan het op prijs concurreren met traditionele productie, zelfs voor de productie van kleine tot middelgrote aantallen.
Bovendien hebben Binder Jetting-onderdelen een gladdere afwerking en scherpere randen dan DMLS-/SLM-onderdelen, waardoor aanvullende afwerking niet altijd nodig is. Vergeleken met DMLS/SLM, zijn ook de kosten van het ruwe metaalpoeder lager, wat een belangrijke factor is in de stuksprijs.
Anderzijds zullen onderdelen die middels Binder Jetting worden geproduceerd altijd een interne porositeit hebben van ongeveer 0,2 tot 2%. Let op dat de interne holtes mogelijk geen invloed hebben op de trekkracht die in de technische gegevens vermeldt staat, hoewel het de moeheidsweerstand van een onderdeel wel aanzienlijk kan verminderen.
Onthoud dat het sinteren gemoeid gaat met aanzienlijk krimpen van het onderdeel. Dit krimpen is niet-homogeen en is moeilijk met hoge nauwkeurigheid te voorspellen. In de praktijk zullen meerdere testprints moeten worden gemaakt om tot een CAD-bestand te komen dat het onderdeel in de gewenste uiteindelijke afmetingen zal produceren. Echter is de herhaalbaarheid van dit proces uitstekend. Dat betekent dat, na succesvolle kalibratie, grotere volumes van dit onderdeel kunnen worden geproduceerd.
Technische eigenschappen van Metal Binder Jetting
Onderstaande tabel toont de technische basiscapaciteiten van een gemiddelde hedendaagse Metal Binder Jetting 3D-printer. Meer ontwerprichtlijnen vindt u onder de ontwerpregels.
Eigenschap | Metal Binder Jetting |
---|---|
Materiaalkeuze | Momenteel beperkt RVS, gereedschapsstaal, Wolfraamcarbide |
Dimensionale nauwkeurigheid | ± 0,2 mm (± 0,1 na proeven) |
Gebruikelijk bouwformaat | 400 x 250 x 250 mm (-20% effectief bouwformaat na sinteren) |
Gebruikelijke laagdikte | 35 - 50 μm |
Gebruikelijke oppervlakteruwheid | RA 6 μm |
Ondersteuning | Niet vereist voor printen |
Interne porositeit | Tussen 0,2 - 2,0% |
Kosten per onderdeel | $$$ |
Part 4
Metal Extrusion
Metal Extrusion is een alternatief, voordelig 3D-printproces voor metaal dat voornamelijk geschikt is voor prototyping-doeleinden of voor losse, op maat gemaakte onderdelen.
Hier gaan we dieper in op de kenmerken en belangrijkste voordelen en beperkingen van dit additieve proces om u te helpen begrijpen hoe u dit het meest effectief kunt gebruiken.
Wat is Metal Extrusion 3D-printen?
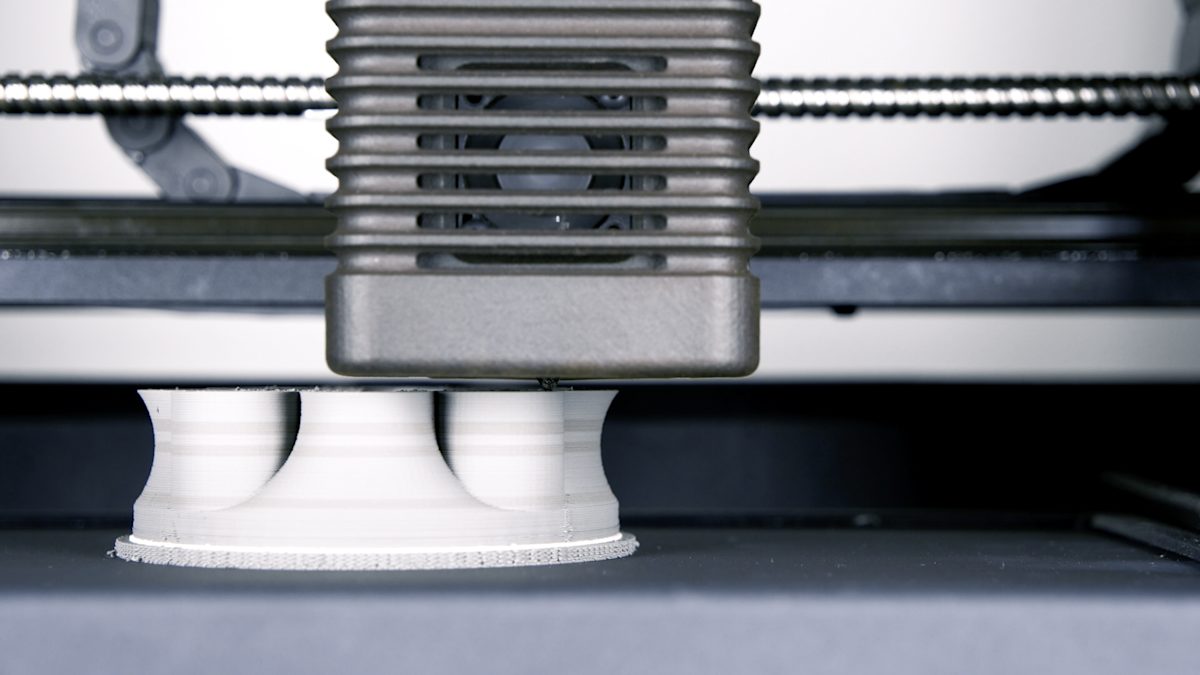
Metal Extrusion is een variant van het klassieke FDM-proces voor kunststoffen. De eerste Metal Extrusion 3D-printers kwamen in 2018 op de markt. De technologie wordt ook wel Bound Metal Deposition (BMD) of Atomic Diffusion Additive Manufacturing (ADAM)
Net als bij FDM, wordt het onderdeel laag-voor-laag gebouwd door materiaal via een sproeistuk te extruderen. In tegenstelling tot FDM, is het materiaal geen kunststof maar een metaalpoeder dat met een polymeer bindmiddel bij elkaar wordt gehouden. Het resultaat van de printstap is een “groen” onderdeel dat moet worden ontdaan van bindmiddel (de-binded) en gesinterd zodat het volledig van metaal is.
Hoe werkt Metal Extrusion?
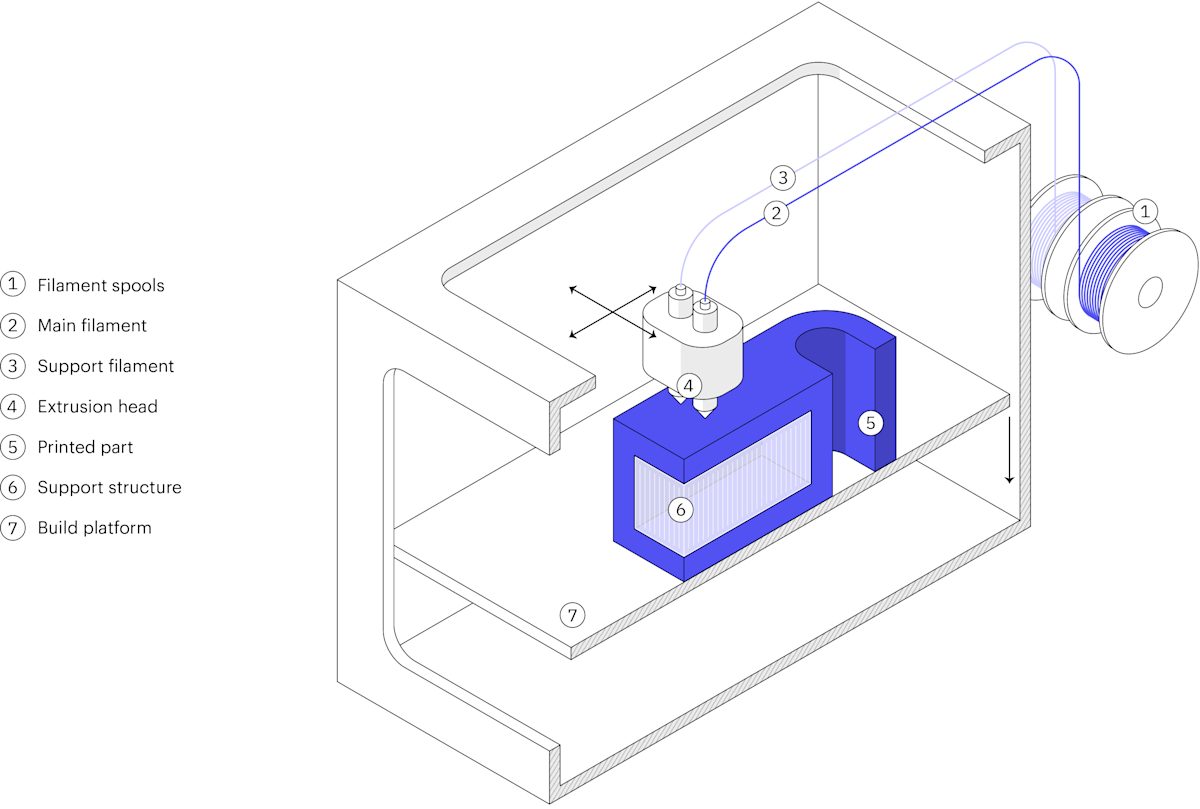
Metal Extrusion is een proces met drie stappen. Er is een printstap, een stap voor het verwijderen van bindmiddel (de-binding-stap) en een sinter-stap. Dit is hoe de printstap werkt:
- Het ruwe materiaal heeft de vorm van een filament of staaf die normaliter bestaat uit metaaldeeltjes die met polymeer en/of was aan elkaar gebonden zijn.
- Deze staaf of filament wordt geëxtrudeerd door een verhit sproeistuk en laag-voor-laag gedeponeerd, waardoor op basis van een CAD-model een onderdeel wordt gebouwd.
- Tegelijkertijd worden, indien nodig, ondersteuningsconstructies gebouwd. De interface tussen de ondersteuning en het onderdeel wordt geprint van een keramische ondersteuningsmateriaal dat later eenvoudig met de hand kan worden verwijderd.
Als de print klaar is, moet het resulterende “groene” onderdeel, met vergelijkbare stappen als bij Binder Jetting, worden nabewerkt om metaal te worden. Het “groene” wordt eerst enkele uren in een oplossing gewassen om het merendeel van het bindmiddel te verwijderen. Vervolgens wordt het gesinterd in een oven, om de metaaldeeltjes te binden en een volledig metalen onderdeel vormen.
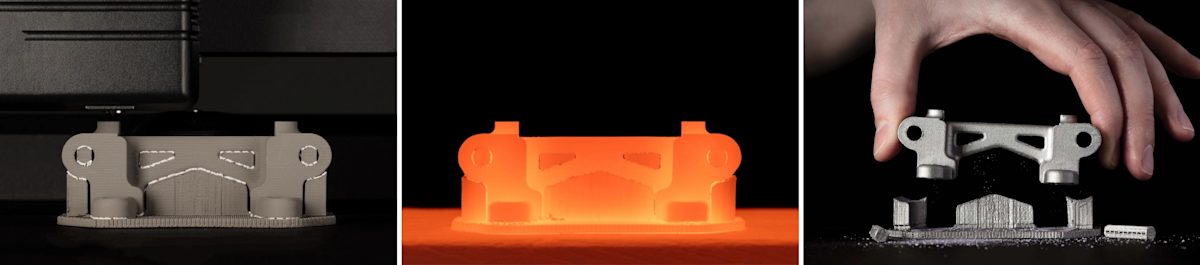
Tijdens het sinteren worden de afmetingen van het onderdeel ca. 20% kleiner. Het onderdeel moet groter worden geprint om dit te compenseren. Net als bij Binder Jetting, is deze inkrimping niet homogeen. Dit houdt in dat enige mate van uitproberen (‘trial and error’) vereist is om een bepaald ontwerp nauwkeurig te kunnen produceren.
Metal Extrusion vs. FDM van kunststoffen
De wijze waarop Metal Extrusion en kunststof FDM printers werken is redelijk vergelijkbaar. Beide processen printen onderdelen bijvoorbeeld hol, met een celomtrek en infill.
Behalve het materiaal zijn er twee andere, belangrijke, praktische verschillen tussen Metal Extrusion en FDM die u in gedachten moet houden. Beide zijn verbonden aan de mechanica van het proces van ontdoen van bindmiddel (de-binding) en sinteren.
- Wanddikte: In Metal Extrusion, moeten onderdelen altijd een consistente wanddikte hebben (bij voorkeur kleiner dan 10 mm). Als dit niet het geval is, dan kan de tijd die nodig is voor het volledig ontbinden en sinteren van de onderdelen enkele uren langer zijn.
- Ondersteuningsconstructies: Net als bij FDM, is in Metal Extrusion vaak ondersteuningvereist tijdens het printen. Bij Metal Extrusion echter, is ondersteuning ook vereist tijdens het sinteren. Bij deze zeer hoge temperaturen wordt het metaal zacht en kneedbaar en kan het onder zijn eigen gewicht bezwijken.
Voordelen & beperkingen van Metal Extrusion
Metal Extrusion is uitstekend voor functionele prototyping en kleine producties van metalen onderdelen waarvoor anders een 5-assige CNC-frees zou moeten worden gebruikt.
Tegen slechts een fractie van de kosten van DMLS/SLM of Binder Jetting, zijn Metal Extrusion-printers de meest economische systemen voor metaal tot nu toe. Daardoor heeft een breder publiek toegang tot de voordelen van 3D-printen met metaal (geoptimaliseerde structuren, assemblage consolidatie, interne kanalen), vooral voor prototyping-doeleinden en de productie van kleine aantallen. Bovendien maken het gebruiksgemak van deze systemen, en de lage gezondheids- en veiligheidseisen die ervoor gelden, hen aantrekkelijk voor het intern produceren van aangepaste onderdelen of tooling om andere activiteiten te ondersteunen.
Vergeleken met andere productietechnologieën echter (zoals CNC-frezen en plaatstaal), zijn de kosten van Metal Extrusion nog altijd aanzienlijk. Voor eenvoudige geometrieën is het voordeliger (en vaak sneller) om te kiezen voor een traditioneel productieproces, zelfs bij het outsourcen van productie. De grootste factor in deze uiteindelijke kosten is de tijd die nodig is voor het verwijderen van het bindmiddel (de-binding) en het sinteren van de geprinte “groene” onderdelen. Dit duurt gemiddeld 24 tot 72 uur.
Vanuit een technisch perspectief zijn de onderdelen die met deze systemen worden geproduceerd niet geschikt voor veeleisende toepassingen, omdat ze minder goede mechanische eigenschappen hebben dan smeedmetaal (~33% minder sterk), als gevolg van de interne porositeit (ca. 2-4%).
Technische eigenschappen van Metal Extrusion
Onderstaande tabel toont de technische basiscapaciteiten van een gemiddelde hedendaagse Metal Extrusion 3D-printer. Voor meer ontwerprichtlijnen verwijzen wij naar de ontwerpregels.
Eigenschap | Metal Extrusion |
---|---|
Materiaalkeuze | Momenteel zeer beperkt RVS |
Dimensionale nauwkeurigheid | ± 0,5% met een ondergrens van ± 0,5 mm (± 0,020”) |
Gebruikelijk bouwformaat | 300 x 200 x 200 mm (-20% effectief bouwformaat na sinteren) |
Gebruikelijke laagdikte | 50 - 200 μm |
Ondersteuning | Vereist voor printen en sinteren |
Interne porositeit | Tussen 2,0 - 4,0% |
Kosten per onderdeel | $$$ |
Part 5
Ontwerpen voor 3D-printen met metaal
Ontwerpen voor 3D-printen met metaal vereist een andere mentaliteit en kent een unieke set ontwerpregels en beste werkwijzen.
In dit deel laten wij u kennis maken met de basisprincipes en gereedschappen die u zullen helpen het meeste uit uw ontwerpen te halen, zoals topologische optimalisatie.
Belangrijke ontwerpoverwegingen
Ontwerpen voor een additief proces is onderhevig aan een andere set regels dan ontwerpen voor “traditionele” productie. De unieke ontwerpvrijheid, maar ook de unieke set beperkingen, vereisen een andere denkwijze van de ontwerper.
Hier volgt een lijst met belangrijke suggesties die u in gedachten moet houden bij het ontwerpen voor 3D-printen met metaal:
Belangrijke ontwerpoverwegingen
Vanwege de hoge kosten is het zelden economisch verantwoord om 3D-printen met metaal in te zetten om onderdelen te produceren die zijn ontworpen voor traditionele processen.
Sterker nog, vaak is het technisch onmogelijk om diezelfde geometrieën zo te produceren. Delen die dikker zijn dan 10 mm, bijvoorbeeld, zijn gevoeliger voor vervorming of andere productiedefecten en moeten dus worden vermeden.
Ontwerpcomplexiteit wordt vaak als schadelijk gezien omdat het verband houd met hogere kosten. In 3D-printen met metaal is dit niet het geval. In tegendeel, manieren vinden om de toegevoegde waarde die geometrische complexiteit aan een systeem toevoegt, is aan belangrijk aspect in het volledig benutten van de voordelen van 3D-printen met metaal.
Als u begint met het herontwerp van een onderdeel of assemblage voor 3D-printen met metaal, is het doorgaans een goed idee om helemaal van voor af aan (‘met een leeg canvas’) te beginnen. Zo voorkomt u beperkingen als gevolg van bestaande ontwerpen.
Het duidelijk definiëren van ontwerpvereisten (draagkracht, randcondities, gewicht van het onderdeel, enz.) is hierbij zeer belangrijk. In het volgende deel zullen we zien dat moderne CAD-software deze gebruiken als input om geoptimaliseerde constructies met organische vormen te creëren.
Het is goed om een helder beeld te hebben van de oriëntatie van het onderdeel in de machine. Printoriëntatie is belangrijk omdat het de positie en de behoefte aan ondersteuningsconstructies bepaalt.
Het doel van de ontwerper zou moeten zijn om onderdelen te creëren met zelf-ondersteunende eigenschappen, zodat zo min mogelijk extra ondersteuning vereist is en bouwsucces wordt gegarandeerd.
Ongeacht het proces, bij 3D-printen met metaal is nabewerking altijd vereist. Dit kan een verplichting zijn (zoals de verwijdering van ondersteuning in DMLS/SLM of sinteren voor Binder Jetting en Metal extrusion) of optioneel (zoals een CNC-frees om kleinere toleranties te realiseren of thermische behandeling om de materiaaleigenschappen te verbeteren).
Het is dus essentieel om de nabewerkingsvereisten en de beschikbare opties in gedachten te houden bij het ontwerpen van een onderdeel voor 3D-printen met metaal.
Instrumenten & software voor ontwerpoptimalisatie
Moderne CAD-pakketten bieden instrumenten om u te helpen de geometrische vrijheid van 3D-printen met metaal volledig te benutten. Met deze door algoritmes aangestuurde ontwerpinstrumenten kunt u orgaan-achtige constructies creëren die beter presteren dan onderdelen die met traditionele methoden zijn ontworpen.
Er zijn momenteel drie voorname strategieën die kunnen worden toegepast. Die strategieën kunnen of de prestaties van een bestaand ontwerp optimaliseren, of helpen bij de creatie van geheel nieuwe constructies op basis van een set ontwerpeisen.
Rasterconstructies
Het toepassen van een rasterpatroon is een hele goede manier om een bestaand ontwerp te optimaliseren.
Rasterconstructies kunnen lichtgewicht onderdelen opleveren, de warmtewisselaars in oppervlakken maximaliseren of voor een bestaand ontwerp de printbaarheid verbeteren en de productiekosten verlagen.
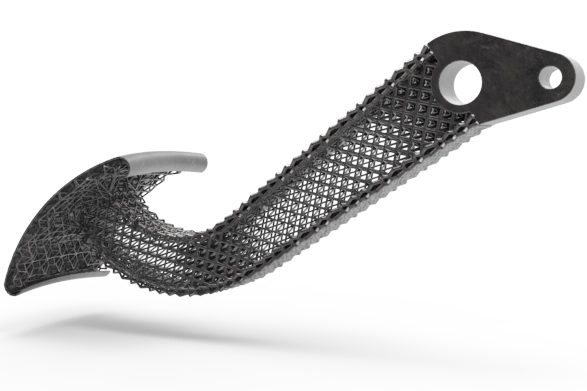
Topologische optimalisatie
Simulatie-gestuurde topologische optimalisatie ondersteunt de creatie van constructies met minimale massa en maximale rigiditeit.
Bij topologische optimalisatie worden de door de gebruiker gedefinieerde ontwerpruimte en de belastingsscenario’s geanalyseerd om te bepalen op welke plekken materiaal kan worden verwijderd. Het resultaat van de simulatie kan dan worden gebruikt om onderdelen te ontwerpen voor optimale prestaties in die belastingsscenario’s.
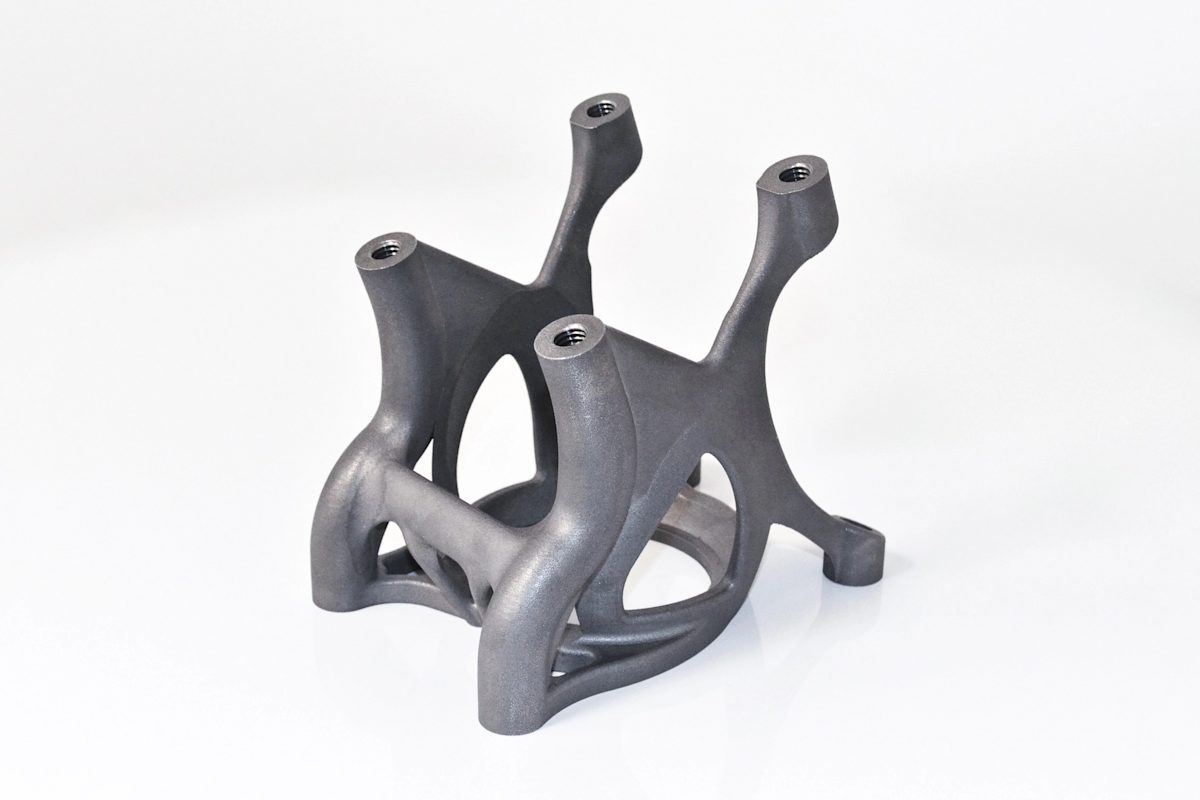
Generatief ontwerp
Generatief ontwerp is een variant op het door simulatie gestuurde topologisch optimalisatieproces.
Bij generatief ontwerp komen, in plaats van een enkele uitvoer, meerdere ontwerpkandidaten voort uit de analyse. De resulterende ontwerpen zijn allen produceerbaar en voldoen aan de ontwerpeisen. Zo kan de ontwerper verschillende oplossingen verkennen en die optie kiezen die past bij de toepassing (bijvoorbeeld, op basis van secundaire afwegingen).
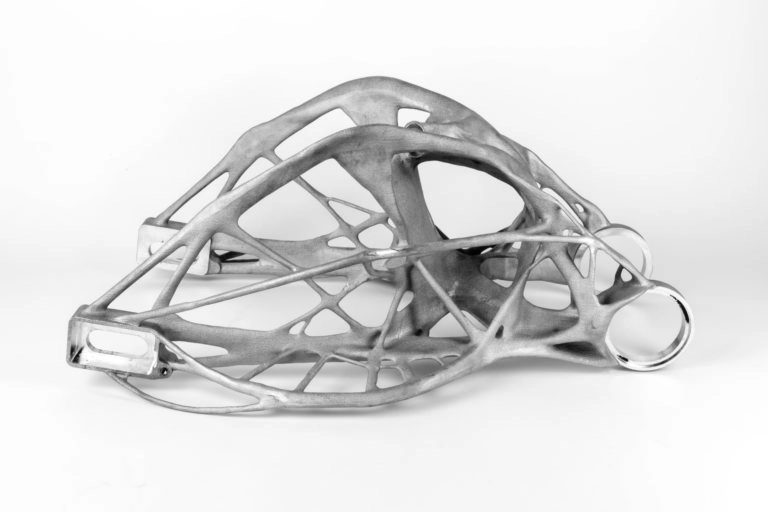
Het wordt sterk aanbevolen gebruik te maken van een van deze geavanceerde CAD-technieken - zeker voor het ontwerpen van DMLS-/SLM-onderdelen. Hieronder hebben we een korte lijst verzameld van CAD-pakketten die instrumenten bieden voor ontwerpoptimalisatie om aan de slag te gaan met het 3D-printen van metaal:
Ontwerpregels
Zelfs bij gebruik van geavanceerde CAD-tools, moet u zich aan bepaalde ontwerprichtlijnen houden. Deze hebben betrekking op de basismechanica van 3D-printprocessen voor metaal. Hier volgt een lijst van de belangrijkste ontwerpregels:
Minimale wanddikte
DMLS/SLM: 0,4 mm
Binder Jetting: 1,0 mm
Metal Extrusion: 1,0 mm
In het “groene” stadium zijn Binder Jetting- & Metal Extrusion-onderdelen breekbaar. Met dikkere wanddelen is de kans dat ze breken kleiner.

Maximum hoogte-breedteverhouding
DMLS/SLM: 8:1
Binder Jetting: 8:1
Metal Extrusion: 8:1
Ondersteunende ribben kunnen extra stabiliteit toevoegen aan lange aspecten (net als bij spuitgieten).

Minimum kenmerkformaat
DMLS/SLM: 0,6 mm
Binder Jetting: 2,0 mm
Metal Extrusion: 3,0 mm
Geïsoleerde kenmerken zijn gevoeliger voor fouten tijdens het printen of verwerken dan wanddelen. Overweeg voor pinnen gebruik te maken van kant-en-klare inzetstukken.

Minimaal detailformaat
DMLS/SLM: 0,4 mm
Binder Jetting: 0,1 mm
Metal Extrusion: 0,5 mm
Het minimale detailniveau is afhankelijk van het formaat van de laser, binddruppels of het sproeistuk.

Minimale diameter voor gaten
DMLS/SLM: Ø1,5 mm
Binder Jetting: Ø1,0 mm
Metal Extrusion: Ø1,5 mm
Overweeg, voor gaten die niet zijn uitgelijnd op de bouwrichting, een traanvormig ontwerp om te voorkomen dat ondersteuning vereist is.
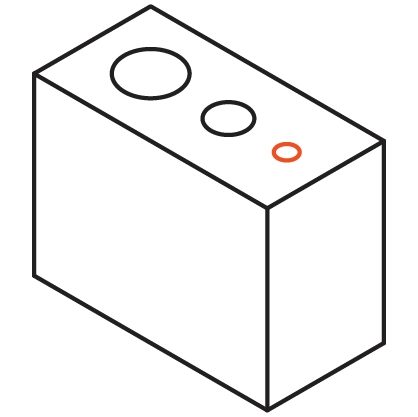
Maximale overhanghoek
DMLS/SLM: 50°
Binder Jetting: N/A
Metal Extrusion: 45°
Bij Binder Jetting en Metal Extrusion kan extra ondersteuning vereist zijn bij het sinteren.

Niet-ondersteunde randen
DMLS/SLM: 0,5 mm
Binder Jetting: 20 mm
Metal Extrusion: 0,5 mm
Overweeg de overhang te elimineren door een afschuining van 45° toe te voegen onder de niet-ondersteunde randen.
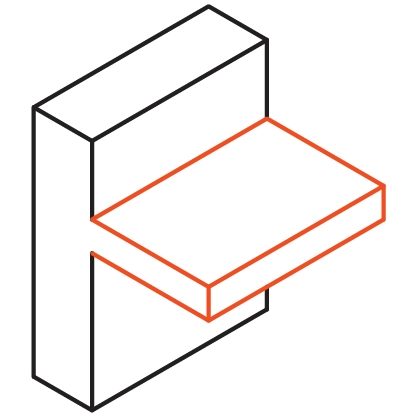
Volg onderstaande links om meer te leren over het maken van ontwerpen voor de verschillende 3D-printprocessen voor metaal:
Part 6
Nuttige hulpmiddelen
In deze handleiding hebben we alles behandeld dat u nodig hebt om aan de slag te gaan met 3D-printen met metaal, maar er valt nog veel meer te leren.
Hieronder vermelden we, voor degenen die dieper op de stof in willen gaan, een lijst met de beste en nuttigste hulpmiddelen voor 3D-printen met metaal en andere digitale productietechnologieën.
Kennisbank
Hier hebben we alles benoemd dat u nodig hebt om te beginnen met 3D-printen. Er is echter nog veel meer te leren in onze Kennisbank - een verzameling technische artikelen over alle productietechnologieën, geschreven door experts van Protolabs Network en de productie-industrie.
Hier volgt een selectie van onze populairste artikelen over 3D-printen:
Handleidingen voor andere productietechnologieën
Wilt u meer te weten komen over digitale productie? Er zijn meer technologieën om te verkennen:
3D geprinte onderdelen nodig?
Ga naar Protolabs.com